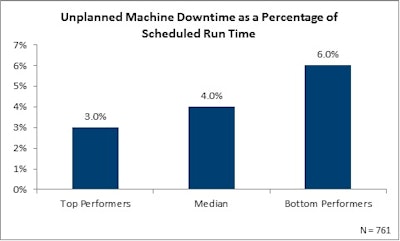
A multimillion dollar investment in new facilities and equipment can create enormous pressure to get it right in terms of cost, deadlines and return on investment (ROI). If unplanned machine downtime occurs, it can drastically reduce ROI by causing disruptions in quality, cost and cycle time. The American Productivity and Quality Center (APQC) defines unplanned machine downtime as the time a machine is not operating against its scheduled run time. This does not include downtime for preventive maintenance or unscheduled use.
As the chart above shows, the gap between top and bottom performers for unplanned machine downtime is 3 percent of scheduled run time. That unexpected downtime can wreak serious havoc on an organization’s production schedule.
Once an organization determines the frequency of such downtime, it can begin tracing and addressing the source or sources of the interruptions. Preventive maintenance programs protect investments in equipment, thereby reducing the cost of delays resulting from unscheduled downtime and/or quality slippage.
The data above originated from APQC’s Open Standards Benchmarking in manufacturing, which contains metrics related to manufacturing performance as collected from participating organizations. These metrics can help your organization see where it stands in relation to its peers and identify potential areas for improvement.