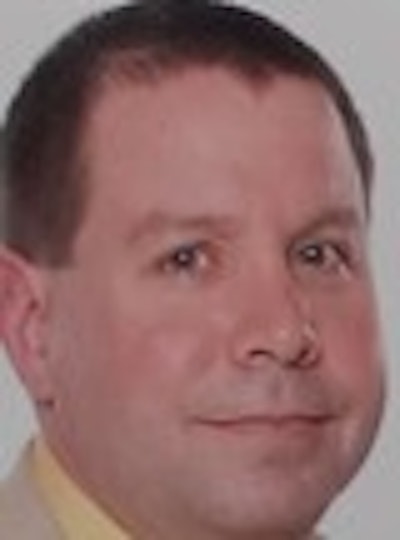
Reducing inventory while maintaining customer service levels is a must for all companies to stay competitive. It’s a challenge that companies face every day, and supply chain professionals like me are always searching for a new technique or solution that can help us gain better use of our inventory.
In 2013, one of our business units was in need of an inventory reduction. The specific business unit has 35 locations, about 15,000 shelf-keeping units (SKUs) and is 15 to 20 levels deep in bill of materials. As if the supply chain wasn’t complex enough, customer service levels needed to be maintained above 90 percent on time.
Safety stock was an area that seemed to have opportunity. The purpose of safety stock is to offset the variability of demand and supply to have goods available when the customer wishes, and to maintain the flow of operations so as not to lose uptime or incur large costs waiting on key inputs. The question of how to have the right mix of safety stock across the entire supply chain network was one that needed to be answered. However, there were cultural and technical roadblocks.
Culturally, various departments, such as the supply chain, commercial, operations and product management, had different approaches and beliefs on where to hold safety stock and how much to hold. As a result, inventory was often times misplaced or duplicated, which resulted in too much safety stock within the system.
Technically, our analytical tool was based on a single-echelon approach, and was used incorrectly or not at all, which resulted in safety stock calculations being viewed as a mistrusted black box.
This single-echelon approach treated the network as a collection of independent single entities. The individual nodes of material-location combinations were not affected by any other material location. Each material location would look at the demand and supply variability in isolation, and calculated the safety stock independent of the upstream or downstream location. We found that using a single-echelon approach led to higher overall safety stock and resulted in the innermost node having the highest inventory requirements as the demand on this node was the highest, but often had the least impact on the end customer.
Different opinions and a single-echelon approach was proving to be detrimental to our business as we soon learned. My organization agreed that enough was enough, and this was our opportunity to make some drastic changes. We decided to approach the problem with a two-step solution.
Our first step was to establish an internal team, consisting of schedulers, production engineers, product management and commercial management, and tasked it with determining what factors were to be used to set safety stock as well as validating the results from the analysis tool. The internal team partnered with Arkieva/Solventure and jointly developed a tool that took a holistic view of safety stock levels and considered the finished inventory at the site level, as well as the intermediates and raw materials using the bill of material. This interactive process allowed us to translate business requirements and knowledge into analytics, and convert the Arkieva/Solventure expertise back into the business process through education.
The second step was to develop a multi-echelon inventory optimization tool. As compared to a single echelon, a multi-echelon approach considers the entire network and differentiates between the service levels at the internal nodes from the service level at the node adjacent to the customer. Different internal service levels can lead to different overall targets to reach the objective. Another benefit to using a multi-echelon approach is it keeps more inventory at the outer nodes to help keep the customer service level the same, but lower the overall inventory. As the internal service level goes down, the multi-echelon model pushes more inventory closer to the customer to retain the same customer service level.
Two major outcomes occurred from this initiative: the first being that, as an organization, we built a common understanding of the purpose, placement and optimal amount of safety stock.
When safety stock is used for the customer, the stock only helps the customer when it is located at the end of the distribution chain. It can be placed upstream to optimize cost, but only to the degree that the production lead time is within the customer lead time. When safety stock is used to maintain flow of operations, it should be placed on the materials preceding the step you wish to maintain flow. It is critical that this is used sparsely for critical operations in which capacity lost or costs become unacceptable. The quantity of safety used to offset the variability of demand is generally best to be a data-driven exercise looking at a number of factors.
The second outcome was the delivery of an analytical tool. The interactive design process with Arkieva/Solventure resulted in a tool that had a multi-echelon approach due to the size and complexity of the supply chain. Additionally it had a tailored safety stock calculation including elements such as forecast accuracy (under forecast, customer lead time, manufacturing lead time and order pattern variables). The tool has the ability to properly understand make-to-order, as well as other nodes in which stock cannot be held. The ability to identify and protect bottleneck materials from stock-out and the ability to deal correctly with sparse data, including items that were always over-forecasted, was included. Lastly, the tool had the ability to solve safety stock based on either or both service level or acceptable late days at the SKU supply point level. Macro level targets do not yield desired results. Overall, building business intelligence into the model was key.
By including the cross-functional team in the development and validation of the tool, confidence was built in the tool and it also facilitated the need to educate themselves about the tool. More importantly, this business unit was able to experience a $5.9 million dollar decrease in safety stock setting, which resulted in an $8.5 million total inventory decrease. The inventory reductions were obtained by removing the unneeded safety stocks and repositioning the stocks where it would do the most good. As a result, there was no impact on customer service levels.
Through various simulations in service levels, bottleneck materials and lead times, we were able to truly understand the levels. The cross-functional team provided multiple insights. The production engineers brought technical aspects, such as determining how much to hold on intermediates and raw materials to make worthwhile usage. Commercial groups aided greatly in understanding what is important from a customer standpoint. All functions provided thoughts on how to best educate the business functions on the purpose and use of safety stocks. The project began in 2013 and, in 2014, the tool and process was expanded across multiple businesses within Momentive.