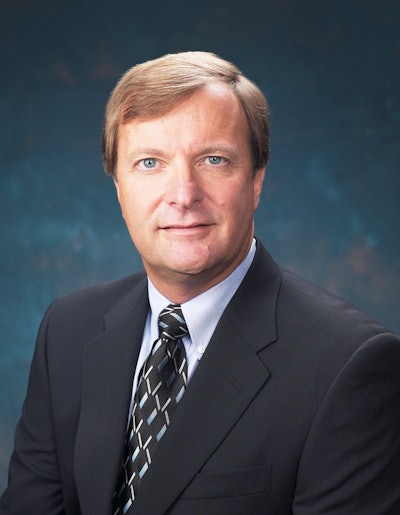
Chemical safety touches us all. It impacts the food we eat, our health and our lifestyle. Impediments to safety can endanger individuals, businesses and society in general. Common sense dictates that sound chemical management should rely on a single classification and labeling system to address specific use patterns and groups of chemicals at the national, regional and international levels.
Such a need especially rings true when you consider that some of the world’s largest economies produce more than $2 trillion while many fair-size countries’ economies produce less, which helps put in perspective the impact of the global chemical business. According to the Occupational Safety & Health Administration (OSHA), chemicals are an enterprise that generate more than $1.7 trillion per year. In the U.S., chemicals are more than a $450 billion business and exports are greater than $80 billion per year.
As such, companies urgently need to execute their compliance initiatives, especially since some of those that have begun the transition compare it to withstanding a tidal wave. By December 1, 2013, employers are required to train employees on the new label elements and Safety Data Sheet (SDS) format. As of June 1, 2015, chemical manufacturers, importers and employers are required to comply with all modified provisions of the final rule—distributors may ship products labeled by manufacturers under the old system until December 1, 2015.
If the appropriate tools and methods are in place to ride the wave, the volume and scope of change ahead will not be as daunting. But noncompliance with those initiatives carries a tremendous amount of risk throughout the supply chain. Upstream, noncompliance could result in significant fines and penalties and damage to the company’s reputation. Downstream, noncompliance may directly impact safety in the workplace. Conversely, compliant companies may realize reduced risk as a result of proper training and education of employees on the various aspects of the new standard.
Adoption across the masses
The need for a single chemical classification system was the impetus behind the creation of the Globally Harmonized System of Classification and Labeling of Chemicals (GHS), an international mandate adopted at the 1992 United Nations Conference on Environment and Development (UNCED), also known as the “Earth Summit.”
OSHA published its revised Hazard Communication Standard, known as HazComm 2012, in the Federal Register on March 26, 2012, aligning the standard with GHS. The standard has profound implications for supply chain professionals and requires extensive planning and preparation.
But the U.S. was not an early adopter of GHS. New Zealand led the way in 2001 and was quickly followed by a wave of Asia-Pacific nations. The European Union adopted the Classification, Labeling and Packaging (CLP), its version of GHS, along with the Registration, Evaluation, Authorization and Restriction of Chemicals (REACH) regulation in 2009. Many countries have pending revisions under current consideration, while other nations require legislative action to enact such sweeping reforms. The varying implementation timetables for GHS across the world point to the need for supply chain professionals to assess their global supply chain operations and take into account GHS implementation timing in countries where they have operations or conduct business.
As much as GHS is meant to drive global harmonization, its various implementations lack consistency as individual countries are allowed to select the physical hazards; health and environment classes; and associated categories within each class they wish to adopt. Most countries that did implement GHS chose to keep some of their existing hazard classifications and communication standards that are not part of GHS. As a result, there is less harmonization among countries than originally anticipated.
For example, in Europe, companies will be required to follow a harmonized (mandatory) classification of specific substances. That may differ from South Korea and Japan, which also have official lists of recommended GHS classifications for substances.
Though the harmonized system is often disjointed, the intention is to encourage participation through flexibility with the goal of continuous movement toward a true GHS. The challenge for risk professionals and supply chain managers is to decipher how the various global adaptations and implementations of GHS will impact their businesses from a risk management perspective.
Preparing for HazComm 2012
Managing the standard’s classification requirements will be particularly challenging for risk professionals and supply chain managers. Manufacturers and importers will need to reclassify their hazardous materials and capture additional data for publication on labels and safety data sheets (SDS’). New criteria for classifying human health and physical hazards as well as OSHA-defined hazards and hazards not otherwise classified (HNOC) have far-reaching implications for the data contained within SDS’ and product labels. In many instances, SDS’ and shipping labels will need to be re-authored to comply with the new guidelines set forth in HazComm 2012.
Key components to enact for a successful risk management strategy include:
Analyze SDS management initiatives—Encouraging risk and supply chain managers to conduct a thorough analysis of SDS management initiatives is an excellent starting point. This reassessment includes reviewing the source of relevant SDS’ for all hazardous products on site. Accurate inventory management is the cornerstone of any comprehensive SDS management program. Managers should know exactly which products are on the shelves and ensure each one has a corresponding SDS.
Ensure access to SDS’—Another critical component of HazComm 2012 is enabling access to the relevant information when it is most needed. To ensure compliance with this requirement, new SDS’ should be effectively distributed throughout the company, especially to employees who work with hazardous chemicals. Store SDS’ in paper and/or electronic repositories so they are easily accessible by employees.
Understand the changes—Following the receipt of an SDS with GHS information, managers should review the new SDS and compare it with the previous version to evaluate changes. For the comparison and evaluation of the SDS information, put in place a structured, streamlined process to extract and view old and new information. Once this process is in place, evaluate each SDS to see whether the reclassified product has any business ramifications. Impacts can range from purchasing decisions—such as increased cost of handling a hazardous product on site through storage, personal protective equipment (PPE) and disposal—to a formula evaluation if the classification changes for a raw material.
Use new GHS information—One of the intents of GHS is to improve the understanding of hazard information available to employees. Employee comprehensibility helps prevent accidents through proper understanding of the hazards and the required precautionary measures.
Prepare and train—It’s vital for risk and supply chain managers to become familiar with both the upstream and downstream responsibilities under HazComm 2012. Employees should know where to find information on new GHS-formatted SDS’ and labels and how to interpret GHS information. Manufacturers, wholesalers and retailers may also play a voluntary role in educating customers as they navigate new information filtering through the supply chain. Different parties may need to explain classifications for the products purchased by consumers.
Achieving compliance with GHS across global supply chains can indeed feel like being hit by a tidal wave. Nevertheless, risk professionals and supply chain managers are taking action and conforming to this complex new initiative. Strong processes, applications, systems and service providers can support the various aspects of compliance management for GHS. By recognizing their obligations, companies can help promote chemical safety while at the same time, boost compliance, minimize corporate risk and protect their brands.
Robert S. Christie is Chief Executive Officer and President of 3E Company, a business unit of Verisk Analytics.