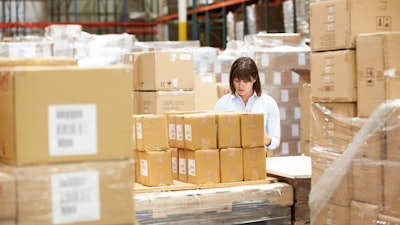
Two years into the pandemic era, manufacturers continue to struggle with massive disruptions to supply chains. The causes run the gamut, from lingering COVID-19 shutdowns and labor shortages, to a scarcity of semiconductors and other critical parts, to transportation bottlenecks and more. Perhaps the only thing these supply chain disruptions have in common is that most of them originate outside a particular company’s factory environment, leaving plant managers struggling for ways to cope with factors largely outside of their control.
The good news is that resilience can nonetheless be achieved through strategic transformation efforts within the factory – specifically, investments to modernize shop floor technology and data for enhanced production agility. Let’s explore how the solution to supply chain planning lies in digitally transforming shop floor operation – helping companies reap more insight and value from their shop floor data.
Modern supply chain challenges require agility with shop floor technology
Modern supply chains rely on global partnerships, so external data will always be important for a company’s supply chain planning. But supply chain organization leaders can’t predict global events beyond their control. What they can predict, and control, are the technologies and processes within their facilities on the shop floor, including metrics around quality, compliance, runtimes, throughput and more.
This level of visibility and control can be achieved through digital transformation of shop floor data and systems. The investment focus should be targeted to some all-too-common pain points. For instance, many factory floors are running on too many multiple generations of technology. This complexity results in misaligned processes and workflows – variances that create inefficiency and waste, and ultimately lead to increased production costs and reduced profitability.
In addition, many companies rely excessively on paper-based processes that can’t support real-time reporting and insights. The reality is that most data used in supply chain planning is at risk of being outdated or inaccurate. Analysis of any at-risk information, from capacity definitions to maintenance shutdowns to routings, may produce unreliable plans if the data is inaccurate. This leads to reactive issue management, inconsistent production schedules and more missed delivery dates – all of which erodes trust in customers and supply chain partners who may scale back business relationships or switch to competitors as a result.
Holistic transformation of shop floor tech
Given the breadth of these challenges, the digital solution for shop floor transformation must be comprehensive, providing a unified view of manufacturing processes, enterprise resources and the entire supply chain ecosystem.
The key to making this a reality is to ensure strong integration between the three pivotal systems that most impact shop floor operations -- the manufacturing execution system (MES), the enterprise resource planning (ERP) system and the supply chain planning (SCP) system. The good news is that these systems typically already exist in some form at the vast majority of facilities, which means that shop floor transformation teams don’t have to start from scratch. It's more a question of enhancing the capabilities and alignment of these systems by connecting SCP systems to MES’ in a closed loop. This ensures that information used to develop supply chain plans is realistic.
Your optimized ERP system should ideally enable a single source of truth and enterprise-wide visibility in one holistic view. This removes barriers that silo data into separate systems and interconnects the shop floor and the top floor. It should be purpose-built and specifically designed for manufacturing settings, including the appropriate business context needed to minimize risks by staying in compliance with statutory and industry regulations. At the same time, a modernized MES can reduce manual and paper-based processes, automating tasks to prevent human errors and increase productivity. An advanced MES can also mitigate compliance risk through database-driven traceability and direct, in-line quality control.
Data-driven agility for supply chain planning
The benefits of optimized ERP and MES are magnified when both are closely integrated together for a real-time view of your entire production lifecycle across all plants. The final step is to then focus these capabilities on optimization of supply chain planning and operations. No matter how much supply chain chaos is raging outside the factory, maximum resilience comes when shop floor data systems are strongly integrated with advanced supply chain planning capabilities.
A modernized supply chain planning platform – backed by well-integrated ERP and MES – can move seamlessly from forecasting to finished goods storage, from complex bill of materials (BOM) to optimized transportation planning and more. This holistic smart factory environment can allow a company to automate purchasing and make transfer recommendations with the ERP solution to stay ahead of demand. Or, it can help the MES prioritize operations by margins to aggressively protect the most profitable product lines.
Throughout, enhanced analytics provides unprecedented levels of insight from Industrial Internet of Things (IIoT) data to monitor floor production and asset management, with centralized machine data collection from programmable logic controllers (PLC) for additional operational insights. Seamless connectivity and data synchronization across systems provides the ability to respond to market demands or customer changes without interrupting production. The best news of all is that such capabilities can increasingly be provided through secure cloud deployments.
Control the unexpected
Supply chain disruptions may be inevitable, but manufacturing leaders are realizing the keys to resilience are in their hands, and within the proverbial four walls of the company. The more manufacturers understand the solution to supply chain planning may reside in the data coming from the shop floor, the more they can focus investments for digital transformation. The result is an enhanced ability to connect processes, resources and supply chain intelligence across the organization – seamlessly uniting the business, from the plant floor to the executive suite, for increased resilience, productivity and value generation.