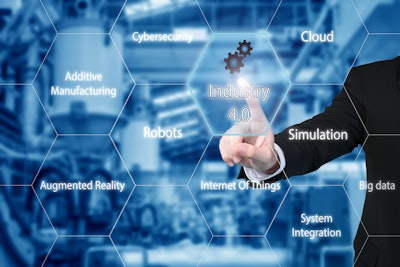
Recently, an explosion of technology has affected the industrial and manufacturing sector. These technologies are designed to assist in repetitive tasks, reduce mistakes and provide wider opportunities for employees to be more strategic. These solutions include:
- Cyber-physical systems
- Artificial intelligence
- Adaptive robotics
- Additive manufacturing
- Internet of Things
- Internet of Services
Combined, these technologies are the pillars of Industry 4.0, which refers to the fourth industrial revolution that leverages these platforms to create smarter and more connected factories that can operate autonomously and adapt to changing market demands. While it is tempting to focus on the technologies themselves, what’s more important is the value that technology-enabled systems deliver. These systems should focus on empowering the human decision-making process to give people more information and choices.
While Industry 4.0 principles are typically associated with manufacturing and production processes, they can also improve back-office business functions, such as finance, human resources and supply chain management. This adaptability is especially important as businesses continue to struggle to attract and retain workers to support their growth objectives. A recent RSM Middle Market Business Index survey showed the increasingly tight market for
- Hiring is a challenge for nearly all middle market companies, and needed skills are in short supply
- Existing workers are burning out, creating a vicious cycle of employee turnover
- Companies are being hardest hit in their most critical areas
To combat the struggles to find talent, maintain their current knowledge and drive operational efficiencies, organizations need to adopt Industry 4.0 principles in all areas of their operations. Using these technologies to their full extent can free existing, valuable knowledge workers from repetitive tasks to higher level functions, creating more satisfied staff and higher organizational value.
Streamlining the back office
There are numerous ways Industry 4.0 technologies can improve back-office functions for manufacturing companies. We take a look at some specific examples below:
Automation: Like the integration of robotics in manufacturing processes, companies can automate repetitive and rule-based back-office processes with robotic process automation to reduce errors and increase efficiency. For example, RPA can reduce invoice processing cycle times by automatically transferring invoice data from PDFs to an enterprise resource planning accounts payable process, reducing data entry time and data entry errors while strengthening regulatory compliance. Also, functions like new customer credit approval processes can be time-consuming and RPA bots can accomplish this task efficiently.
Intelligent workflows: An intelligent workflow is an orchestration method that integrates analytics, artificial intelligence (AI), machine learning (ML)and automation to help organizations perform diverse and complex activities. Industry 4.0 technologies can create intelligent workflows that automate tasks, streamline processes and reduce manual intervention.
In the current digital era, there are opportunities for enterprises to embrace a modern data and technology transformation strategy. This strategy extends existing intelligent workflows by methodologically stitching together various intelligent workflows such as strategic planning and tactical decision-making down to operational workflows across all players in a supply chain ecosystem.
Predictive analytics: Back-office teams can leverage technology to analyze vast amounts of data to identify patterns and trends. For example, predictive analytics can help forecast demand for materials. Demand sensing relies on ML techniques to generate short-term predictions in response to diverse market changes. ML can also drive predictive analytics that combine historical and current data to generate more accurate customer behavior trend forecasts.
For example, due to the COVID-19 pandemic and subsequent supply chain disruptions, businesses found themselves scrambling to find inventory. As a result, many procurement teams rapidly grew inventories and now find themselves overstocked, which has tied up their working capital. An effective predictive analytics approach could help to avoid repeating this mistake, accurately forecasting demand and related inventory needs.
Cloud computing and big data: Cloud-based solutions can centralize data and make it accessible anywhere and anytime. This data availability provides improved insights through analytics into an organization’s operation in near real-time. The ability to deliver this data with real business context is the foundation for delivering a competitive advantage.
System integration: A significant obstacle to operational efficiency is the fragmentation of enterprise data models. Companies often select and/or design systems with a siloed view of their role in the enterprise, which leads to duplication of data. Often, teams make more decisions from Excel spreadsheets than from the formal enterprise systems. The proliferation of sensors and edge computing, which are generating even more data, exacerbates these integration challenges.
Organizations have a tremendous opportunity to drive efficiencies through faster, accurate and consistent decisions by capitalizing on an integrated data model. Smart manufacturing is based on a convergence of connected operational and IT systems and those same concepts can be applied in the back office. Difficulties do exist in integrating layers of technology and systems from different manufacturers of different eras, but this is improving as more vendors work within industry frameworks such as ISA-95.
Enhanced decision making: Many companies have adapted to a data-informed approach for operational decision making. Data can improve decisions, but it requires the right processor. Mainly, the processor of the data is human. However, to fully leverage the data assets available, organizations need to evolve to AI-driven decision making. This shift from individuals’ data processing abilities to determining how to interpret the data improves decision making.
The next wave of decision making includes embedded machine learning and AI in workflows as the primary data processor. Because AI has the capability and capacity to deal with millions of data groupings, the use of such technologies will enable companies to harness a much wider array of data sources. Additionally, AI is less prone to human biases, meaning its use can drive more consistent and objective decisions.
It must be noted that the objective is not to remove humans from the process, but to better equip them for decision making. For example, companies may use AI to predict inventory levels to maximize cash investment and profits, but only a human can factor in the business strategy of providing better customer service, resulting in higher inventory levels.
The bottom line
Industry 4.0 principles have the potential to streamline decision making based on real-time customer and operational data and dramatically improve process efficiency. While the factory floor will undoubtedly benefit greatly from these principles, the greatest gains may occur in non-production functional areas such as the back office. Organizations embracing these principles in areas such as product launches, pricing, operational planning and inventory planning can fuel a cross-functional efficiency revolution.
These principles and technologies will likely cause disruption but also create new avenues for workers willing to gain digital knowledge and skills.