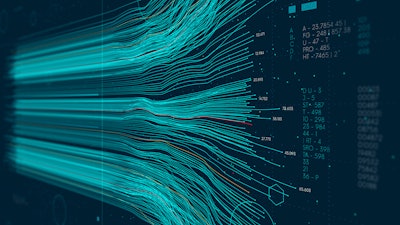
In the fast-paced world we live in — where next-day delivery is king and supply chain challenges are, unfortunately, prevalent — warehousing and distribution operations, above all, need products out the door. This is where data can help. While it’s true these facilities generate data and may already collect and track baseline statistics, it requires a strategic decision for facilities to take that data to the next level so it can be used to measure performance, establish benchmarks and identify improvement opportunities and then for facilities to act on those focus areas.
But even after organizations determine performance improvements are necessary and achievable for a given facility or operation, the path forward can seem unclear. How do you achieve an optimized, data-driven operation?
Data Collection Through Optimization
How are you measuring the performance of your labor and assets? Do you know where the inefficiencies are, how they’re allocating their time and what it’s costing you? If not, how are you narrowing your focus to implement change? And, more important, how do you know if the changes you are making are working?
Modern material handling equipment and technologies make it easier than ever to capture the real-time machine, labor and facility performance data that can help answer critical questions like these. But even if your operation isn’t using the latest technologies, you can make a lot of progress by using the most basic form of data gathering: data collection through observation.
It can start as a simple crawl-walk-run scenario. Start with an observation. Perhaps it is something as small as trash receptacles that are located at the far end of a lot instead of closer to the door that could be costing your employees time and effort. While the small things add up and are important, it is key to note that they are just the beginning.
Using the above trash receptacle situation as an example, this discovery and analysis of unnecessary travel, time and other impacting variables could further scale into all travel inefficiency, including driving. Each of these areas impact your cost. Now we are walking. For example, if we continue to focus on travel, product velocity-based reslotting may be your next focus area, with data from warehouse management systems, location systems and equipment decreasing your overall cost to serve. It can also reduce congestion and get a clear analysis on proper equipment utilization. Ready to run? When you are able to have a clear analysis, you can start to standardize data to use as a networkwide benchmarking tool against your own operations and industry-equivalent activity to further identify opportunities. This isn’t a linear process but rather an iterative one. You can take this businesswide view to help identify where to restart the optimization process.
Once you are able to identify small and large areas of optimizations, other questions naturally come to mind: How far are charging stations from the main area of operations? Can lift trucks be routed around pedestrian crossings to help eliminate stopped time? Are the fastest, most-accurate workers bogged down with routine tasks and responsibilities? Answering and addressing basic questions like these don’t require special equipment or technology and can lay the groundwork for more-robust data-gathering and process-improvement initiatives in the future.
For operations with the ability and the motivation to incorporate the latest technologies, data-driven insights can enhance the productivity of operators and lift trucks and help drive down costs. How? As you scale, you are able to balance your people, equipment and automated solutions simultaneously when you have data on them all. This can open the door to not only managing product velocity but also how your fleet and people interact with each other. After all those are optimized, the resulting data can help you justify future system enhancements and investments.
So Where Do We Start?
Equipment management and analytics systems offer an easy, low-impact entry into the world of telematics-based data acquisition. Asset management systems can give managers critical performance data that can help optimize the performance of a facility’s fleet of lift trucks and other equipment. Maintenance, service and material costs can be tracked and analyzed for trends.
After the Hardware? Focus on People With Labor Management
In the same way that asset management systems can help optimize equipment performance and utilization, labor analytics can offer insight into a wide range of personnel-related productivity data — including, and especially, time. By tracking employee utilization and taking into consideration additional variables, a labor management system can offer a more complete picture of unaccounted-for time, of efforts related to support functions and of overall labor efficiency and effectiveness when core processes are being performed.
Once the data is captured, facility managers can use this data to identify both training opportunities as well as recognize top performers. Data-feeding incentive programs can help you reward your top performers and attract/retain top talent. This data also has the hidden benefit of providing you the activity and customer-based cost data needed to make strategic pricing and negotiation decisions.
Throughout the process, a more complete picture begins to come into focus. The value of a holistic operational picture of equipment, automation, systems and people is that you can start simple and scale into an operational methodology of continuous improvement driven by data.
A Shared Commitment
You have a need. You have asset and personnel data. What’s missing? Even the most advanced telematics and data-acquisition technologies can’t produce the desired results without strong buy-in from the team, an effective change-management effort, and an enterprisewide commitment to making the best decisions for the business and the labor force. It’s that dedication to success that, along with solid, actionable data, can take your operation to higher levels of efficiency, productivity and profitability.