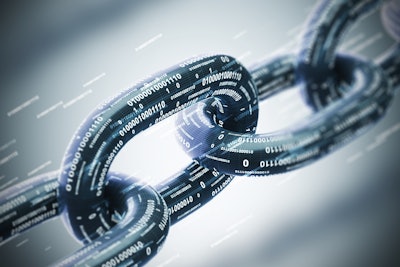
Managing the supply chain of critical industries in the midst of the Coronavirus disease (COVID-19) outbreak has proven to be one of the more challenging aspects of the pandemic and economic crisis. Shortages in supplies such as masks and ventilators have been mirrored by distribution constraints in getting critical supplies where they need to be and products on the shelves where they should be. The fragility of “just-in-time” production and delivery and the downside to high distribution capacity utilization has been front and center in much of the news media.
The potential for Internet of Things (IoT), artificial intelligence (AI), the cloud and distributed supply chain has the potential to transform much of this moving forward.
This point is highlighted by two seemingly unrelated events that happened a few years back.
First, back in 2016, an earthquake hit Japan that significantly disrupted Toyota’s supply chain. Japan’s just-in-time (JIT) production made it such that any disruption at all -- let alone one as large as the series of earthquakes -- would often lead to disastrous production delays. In this case, Toyota temporarily shut down 26 car assembly lines in Japan. Lean assembly without disruption can be incredibly efficient, but disruption in one part of the chain can reverberate throughout the entire chain and lead to costly delays.
The second event (really a series of related business moves) was Airbus’ joint venture to produce small (around 300 pounds) advanced satellites at a rate never before even remotely achieved -- as many as 15 satellites per week. The facility is now located at the Kennedy Space Center next to Jeff Bezos’ Blue Origin LLC.
How are these two events related?
Because the old model of production efficiency is rapidly giving way to IoT, cloud-based interconnectivity led by automated robotics, AI, additive manufacturing (3D printing) and interconnected devises resulting in supply chain efficiencies and factory automation in ways we’ve never seen before.
Gartner estimates that the “Industrial Internet” will dwarf the “Consumer Internet,” generating a staggering $37 trillion in revenue by 2025. The JIT production that made Japan great in the 1970s and 1980s is rapidly giving way to IoT interconnected devises so that the supply chain -- now interconnected through the cloud and guided by AI optimization algorithms -- adjusts to any supply chain disruption automatically.
How are all of these processes connected globally?
Through the IoT interoperability provided by the satellite communications that Airbus, Boeing, Google, Facebook, Amazon and others are frantically fighting for, the winners in this battle will be the backbone of future production, just like Japan’s Lean Six Sigma and JIT production efficiency transformed factories worldwide back in the 1980s.
The lessons we can take from this include:
1. Source supply automatically. Ideally, an AI-based IoT connected supply chain can shift production, sourcing and production capacity during normal times, as well as during a period of crisis. In principal, spikes in demand can be seen early with production adjusted automatically and quickly.
2. Invest in this now. It is difficult, and in some instances impossible, when trying to keep your doors open or struggling to meet demand in critical sectors, but now is the time to transform your business.
3. Use of a key strategic control point. Use supply chain and IoT as a strategic control point -- something you can leverage, own or control for extraordinary margins. Use your development of IoT interconnected supply chain as a point of strategic control. Make this happen now.
4. Plan your supplier base in a way to align incentives. P&G did this with Walmart in the early 1990s to its advantage using a concept called “asset specificity” (a joint investment that aligns the interests of two or more parties). You can use this as an opportunity now to align the interests of your supplier and customer base with your own.
In the end, after the current crisis has passed, the winners will be global growth and companies that have used this time to disrupt themselves.