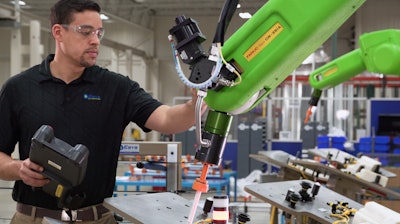
Consumer demand is driving a fast pace of new technology adoption in the supply chain industry. In the pursuit of increased accuracy, speed and safety on the warehouse floor, supply chain companies are increasingly adding wearables and robotics to tasks such as loading, unloading, picking, packing, shipping and receiving. Within warehouse and distribution center management, companies are using wearable and robotic hardware and software systems to move the needle on productivity and efficiency.
Tech companies are scaling up what their devices and software programs can offer and have identified several industry trends that will likely unfold in coming years.
“We're already seeing a huge shift at the EHS (environment, health, safety) level, in large part enabled by biometric wearables, from accidents to near misses and prediction and prevention based on the individual,” says Heidi Lehmann, co-founder of Kenzen. “Trend data that can be truly used to optimize health, safety and productivity, at both the human and machine/operational levels are truly transforming the worksite at a rapid pace. Some analysts are calling this the fourth industrial revolution. It's quite exciting.”
A recent report published by Research and Markets predicts the industrial wearable devices market to exceed $2.78 billion by 2024.TeamViewer
Growing market for robotics, wearables
Devices and software designed to increase efficiency and improve safety on the warehouse floor are growing in popularity in the supply chain.
Industrial wearables track activities and tasks, help workers complete tasks faster and measure health and safety parameters, resulting in fewer injury reports. Most industrial wearables provide real-time data and analytics, allowing employers and managers to tweak workflows on the fly, leading to improved numbers in profitability and productivity.
A report published by Research and Markets in June 2019 predicts the industrial wearable devices market to exceed $2.78 billion by 2024, increasing annually at a rate of 9.2%, with smart watches holding the largest share of growth.
In January, Gartner, Inc. published a report forecasting an $81.5 billion global spend on wearable devices in 2021. This includes spending on smartwatches, wristbands, ear-worn devices, head-mounted displays, smart clothing and smart patches used for health monitoring. In 2020, the greatest increase in spending was on headphones for video calling and use with smartphones, largely due to pandemic-related workflow changes. The report partly credits improvements in sensor accuracy as why the devices are growing in popularity. Advancements in miniaturization have also played a role in the growth.
Similar market growth is expected with industrial robots, commonly used for mundane tasks, picking, loading orders and transportation, among other order fulfillment jobs. A McKinsey & Company report noted that $2.4 billion is spent annually on industrial robotic arms and automation machines. Since 2010, the spend has increased 10% annually, and as of a few years ago, there were at least 2 million robots in use on factory floors, warehouse and similar locations. The report predicted that number to increase to 4.4 million by 2023.
Through the increased use of autonomous robots, which use machine learning and artificial intelligence (AI) to complete tasks, and collaborative robots, or cobots, designed to work alongside humans, the market segment for industrial robots is forecasted to grow to $14.9 billion globally in logistics, according to a report by Fortune Business Insights.
TeamViewer uses AI, Internet of Things (IoT) and augmented reality (AR) in its technology.TeamViewer
Wearable tech will advance to next levels
TeamViewer uses AI, Internet of Things (IoT) and augmented reality (AR) in its technology.
“TeamViewer helps companies like DHL, Coke or Airbus to improve quality, speed and safety of their logistics, manufacturing and maintenance operations,” says Percy Stocker, TeamViewer’s executive vice president, AR Americas. “Using AR-guided workflows and ad-hoc video collaboration, companies can digitize and streamline their processes, while offering a more ergonomic and intuitive solutions to their frontline workers.
Companies also use TeamViewer to improve quality, speed and safety in their operations.
“For example, DHL managed to improve the speed of their logistics operation by 15% on average. Coke significantly improved their quality to 99.99% accuracy level,” Stocker says.
TeamViewer’s technology is advanced enough to now be considered turnkey.
“We did not stop at the minimal viable product; we added all the required features to make the frontline platform truly enterprise ready to support deployment at scale,” Stocker says.
The company is expanding its technological capabilities to make wearables more comfortable to use and provide real-time support and training.
“We will offer ad-hoc support on the spot with the right information and connect them to the most helpful experts as needed,” Stocker says. “This will be a game changer and make companies truly agile with their frontline workers floating to wherever they may be needed most and with the help of our solutions dynamically adjusting to whatever challenge they may be facing.”
Kenzen produces wearable devices and a monitoring platform designed to predict and prevent injuries on the jobsite. The device is worn on the upper arm and samples a worker’s physiology every five seconds.Kenzen
Greater adoption of safety wearables
Wearables, devices that use sensors to monitor worker health, environmental hazards and other issues, received a nod of approval from the Centers for Disease Control and Prevention in a 2019 report that noted that the tools can be a valuable in maintaining the safety of workers in industrial settings.
Kenzen produces wearable devices and a monitoring platform designed to predict and prevent injuries on the warehouse floor. The device is worn on the upper arm and samples a worker’s physiology every five seconds.
“The system sends alerts in real time to workers and safety managers, alerting them when a worker is reaching an unsafe level physiologically,” Lehmann says. “The solution provides protection and intervention in the moment at the worksite, as well as informs changes and planning at one or multiple worksites to enable a safer and more productive workforce.”
Monitoring a worker’s health is important when working in high temperatures, with tasks requiring physical exertion, when employees have pre-existing medical conditions or are dehydrated, she says.
“As individuals, we are all different physiologically depending on gender, age, cardiovascular health, preexisting medical conditions and medications,” Lehmann says. “This is why monitoring workers on sites at the individual level is so important. Customized work/rest schedules, hydration plans, as well as shift changes at the site level, all contribute greatly to total worker health.”
Managers who are monitoring data across worksites receive insights into worker safety and health, but at that level, workers’ names and identities are kept private.Kenzen
More workers will realize wearables can maintain privacy
Workers need to know their privacy is maintained while wearing the devices, she adds.
“We need to make sure the worker is very comfortable with our solution,” Lehmann says. “This begins with the actual comfort of the device when worn by a worker, to worker privacy and making sure the worker understands that the platform has been designed with their privacy in mind.”
According to Lehmann, the worker is the only one who can see their own biometric information in detail and in real time.
“Other user groups only see the information they need to keep the worker safe,” she says. “For example, a safety manager would understand, through the team dashboard, when a worker is calibrating in a dangerous direction and needs assistance or needs to rest, yet they don't see any specific personal health details, only that an intervention may be needed.”
Managers who are monitoring data across worksites receive insights into worker safety and health, but at that level, workers’ names and identities are kept private.
“Leaders see all data across a worksite, or many worksites, but data is deidentified and retrospective, providing insightful, yet non-individualized site insights such as core body temperature risk levels, productivity levels, microclimates, and heat alert frequencies,” Lehmann says.
Using connected wearables on the jobsite is still new, she says, and some companies need to augment their connectivity capabilities if they want to outfit dozens of workers.
“There can be challenges at the IT level to ensure scale across hundreds or even thousands of workers,” she says. “However, worksites are changing very rapidly as the industrial internet of things becomes more and more prolific across commercial sites of all types.”
Wearables can also be used to create social distancing among employees, says Stocker.
“Workers can be trained on the job with limited classroom training or supervisor shadowing,” he says. “If a new associate needs further help, it is easy to just loop the expert in virtually using an ad-hoc video call. This allows companies to implement social distancing guidelines and keep their workers safe, while reducing onboarding efforts by about 60%. On top of that, there is no need to take off safety gear, as the solution is no touch and fully voice controlled.”
Wearables will likely be considered essential to warehouse and distribution center operations, according to ProGlove.ProGlove
More companies will realize wearables can improve efficiency
Just as barcode scanners are essential in moving items within the supply chain, wearables too will be considered essential to warehouse and distribution center operations, says Ilhan Kolko, chief product officer at ProGlove.
“Wearable scanners enhance these processes at large because they easily cut the total scanning time in half,” Kolko says. “Aside from the massive time gain, workers always have their hands free, which is tremendous relief when you load or unload a truck.”
Using wearables and leveraging a more IoT work environment can lead to significant upticks in productivity, he says.
“We recently had a customer who introduced our solutions in their warehouses and found that they increased efficiency by as much as 20%,” Kolko says. “Their first reaction was to assume that the data must have been wrong. But, sure enough, the data was right.
Collaborative robots, or cobots as they’re commonly referred, work alongside humans in industrial settings to complete tasks more quickly.FANUC
Upping automation in robotics
FANUC expects to see an increase in the use of collaborative robots in the industry, says Robert McElmurry, executive director – global accounts, FANUC America. That's because cobots work alongside humans in industrial settings to complete tasks more quickly.
“We're seeing tremendous growth in robotics adoption uptake in terms of those organizations’ ability to deploy that automation,” he says. “We have a very broad range of collaborative arms that are more user friendly and have a lower adoption cost that are more designed for small and medium enterprise users.”
Incorporating automation into the supply chain space will continue to become easier and simpler, McElmurry predicts.
Supply chain companies are increasingly using system integrators to help integrate robotics into business operations, he says. In the future, companies will design warehouses around automation and robotics instead of what is more common now, which is adding robots as needed.
“The industry is still in the initial adoption stages,” he says. “Once the industry matures some and moves toward more automated processes, they will start designing for the automation instead of putting the automation where it would need to exist in today’s processes.
Part of the challenge of incorporating robots into the workplace is getting workers to accept the machines, even when it comes to completing tasks in an unstructured environment, such as a warehouse, says Evan Drumwright, CEO at Dextrous Robotics.
“The biggest problem is how do you get people to accept the machines because the robots aren’t super smart yet,” Drumwright says. “Really what you're doing is, you're just eliminating drudgery. So, then the question is what kinds of drudgery can you eliminate? It all comes down to how structured can you make the task. How easy for the robot can you make it? That has historically been the biggest challenge and will continue to be the biggest challenge.”
E-commerce use increased tremendously due to the Coronavirus disease (COVID-19) pandemic, and as that activity escalates, robotics will aid that growth, he adds.
“There's been a gradual shift in retail sales toward e-commerce, and it just got moved up by about 3-4 years,” Drumwright says. “Companies that we talk to in the logistics industry say they were doing basically seasonal levels of shipments in non-seasonal times, in their volume of business. It's just so much higher, and they don't have the labor pool to deal with it. From a robotics perspective, three years ago, robotics in the supply chain was still relatively nascent. We’re definitely seeing more people looking at robotics as a solution to that issue, not only for safety and disease issues, but for workforce shortages and that sort of thing.”
Upskilling workers for robotics
As companies incorporate more technology and automation into their warehouses and distribution centers, more workers will need to learn how to use it. Companies can bring in outside workers who are trained in automation, but what will more likely happen is the upskilling of current employees, McElmurry says.
“Some of these companies may be able to upskill their workforce somewhat to be able to handle these robotics,” he says. “One of the benefits of that is these types of jobs tend to be higher paying positions. If you have people who are upwardly mobile in the warehouse, this is potentially a nice career path.”
He’s seeing many companies experience growing pains as they add more automation and train workers to handle equipment differently.
“There’s at least some degree of robotic proficiency that's required within those companies in order to continue to expand the degree of automation,” McElmurry says.
FANUC is increasingly training clients’ workers on robotics and automation. The company partnered with 1,300 schools and educational organizations and has trained more than 300,000 people on robots.
“It's a big, important endeavor for us,” he says. “We think it really helps anyone who’s new to this world because there really is a shortage of people who understand how to work with it.”
Fetch Robotics builds autonomous mobile robots (AMRs) and an associated cloud software platform for fulfillment, distribution and manufacturing companiesFetch Robotics
Robotic vision system upgrades
Throughout the next several years, robotics technology is expected to advance significantly. Computer vision systems, too, will advance, improving the speed and accuracy of assembly robots and automated material handling equipment, according to a Mordor Intelligence report.
AI and machine learning is enabling continued upgrades to robotics, which are helping vision systems recognize unknown objects, McElmurry says.
“Those applications are going to continue to open up over the next several years,” he says. “Over that time, there's a set of things that are going to be automated in the future that weren't automatable today.”
Fetch Robotics builds autonomous mobile robots (AMRs) and an associated cloud software platform for fulfillment, distribution and manufacturing companies. Using the Fetch Robotics system, AMRs can be deployed within hours to improve efficiency. The system integrates robotics and wearables to direct robots throughout a warehouse or similar facility.
“For example, simple integration with a connected voice picking system like Vocollect allows a warehouse associate to drop a cart at the end of an aisle and then speak a command that the voice system will pass to the AMR system that triggers an AMR to go pick up that cart and take it to another zone or to packout,” says Stefan Nusser, chief product officer at Fetch. “Similarly, a warehouse associate can also use a wearable scanner to do the same thing. A barcode placed on the floor at the end of an aisle is associated with a specific workflow. The associate simply scans the barcode of the workflow he or she wants triggered and an AMR will perform that workflow. There can be multiple barcodes, each labeled with the workflow that will be triggered. In either case, this functionality enables warehouse associates to use the devices that they use every day and also allows them to spend all of their time doing productive work instead of 50% of the time manually moving material all over the warehouse.”
Nusser predicts that vision assistance innovations, such as head-ups displays will become more common in the future in the supply chain industry.
“Within the next year or two, they will be prevalent for certain processes where spatial arrangement is particularly important,” he says. “A relevant use case is around case picking, where headset displays help associates better visualize placement of cases on pallets.”