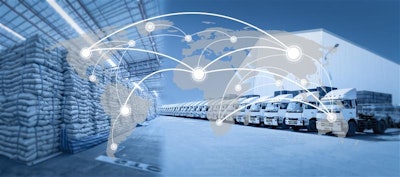
Critical Manufacturing has announced the most advanced and disruptive release of its Industry 4.0 Manufacturing Execution System (MES). Critical Manufacturing MES V8 reveals a revolutionary new IoT Data Platform that merges IoT with MES and, two significant new modules that advance smart manufacturing in areas of Materials Logistics and Factory Automation to enable manufacturers to move closer to ‘Lights-Out’ factories. The release represents a step change for manufacturers to accelerate progress towards Industry 4.0.
Industry is pursuing Industrial Internet of Things (IIoT) projects at a staggering pace, yet despite having the highest share of IoT devices of any business segment, manufacturing still lags behind in being able to seize the full value of the data, due to a lack of focused solutions. Critical Manufacturing’s new IoT Data Platform is designed to solve the manufacturing data challenge with a new approach that combines IIOT, MES, equipment integration and data platform elements for processing, and analytics that promises to accelerate the future of true manufacturing insights and intelligence to drive better business outcomes.
"Whether you call it IIoT, Big Data, Artificial Intelligence or Industry 4.0, we are witnessing an authentic revolution where the asset at the center of everything is data. We believe that by combining IoT with our modern MES we have created a pioneering solution. Our new IoT Data Platform is designed specifically for manufacturers to rapidly gain invaluable knowledge from insights that were previously impossible to unlock, and turn them into action and rapid ROI in the context of manufacturing operations,” Francisco Almada Lobo, Critical Manufacturing CEO said.
An end-to-end data solution providing deeper insights into manufacturing processes
The Critical Manufacturing IoT Data Platform is a complete, highly scalable solution that includes all the necessary capabilities for end-to-end data management and analysis with Edge Processing, Data Ingestion, Data Brokering, Data Processing, and Serving and Output. The IoT Data Platform differentiates from other solutions with its unique MES data enrichment process, contextualization and closed loop outputs with MES, ensuring that problems are being resolved holistically. The Platform can ingest massive amounts of data, both structured and unstructured, from IoT devices, from the MES and from other data sources such as ERP and PLM. Moreover, the solution contains a common data model, a unique MES enrichment process and also allows 3rd party solutions to integrate with the data platform, mitigating some of the biggest causes of failure when deploying IIoT projects. The IoT Data Platform is anchored on two widely proven universal technologies, and leverages the Apache Kafka™ streaming data platform and Apache Spark™ unified analytics engine, which also help companies avoid high data storage and IT costs. These technologies enable all data to be stored and processed immediately and also events can be replayed as needed at a later time. Data Scientists and engineers can access the data to understand what is happening and what may happen in the future. Manufacturers can benefit from faster decision making and on-time problem solving as data is analyzed in their context. Cost of data storage is reduced and data security assured, with the solution being deployable on premise or in cloud environments.
“The new Critical Manufacturing IoT Data Platform has all the main building blocks to transform connectivity and deliver data that is detailed enough to create machine learning models and predictive and prescriptive analytics. With access to powerful new insights, manufacturers can drive fast ROI with use cases that drive initiatives such as predictive maintenance and yield improvement, and bridge the divide between IT and OT to connect all the data that matters. The common IoT and MES data model plays an essential role with the IoT Data Platform to deliver contextualized information and allow true insights to be derived,” Almada Lobo continued.
The latest Critical Manufacturing MES V8 also includes the new ‘Factory Automation’ and ‘Material Logistics’ modules. The Factory Automation module is a factory level workflow engine designed to coordinate different systems and applications to achieve higher levels of automation. A step towards ‘lights out’ manufacturing, this new module provides high-tech manufacturers with greater resiliency and responsiveness to guard against disruptions and reduce dependency on human resources.
The Factory Automation module can improve operational efficiency, productivity, product quality and equipment utilization while shortening cycle times and reducing labor costs. It can monitor all factory events and orchestrate the right response from different systems and applications. Users can create and execute specific workflows, including calculating next equipment process steps of in-process or completed lots and guide automated transport vehicles or material handling systems. The complete flexibility of this module means manufacturers can progressively increase their automation capabilities, mixing automated and manual scenarios to suit their manufacturing processes.
The new Material Logistics module manages all business processes related to material movements, providing an integrated warehouse management for just-in-time manufacturing and supporting the full material logistics lifecycle, maintaining optimum material availability and flow. The functionality provides manufacturers with improved visibility and tracking of materials, reduces material shortages, quickens material request fulfillment times, improves inventory management, reduces scrap, and lowers overall material handling costs.
Overall, the new Critical Manufacturing MES V8 is one of the most complete and advanced manufacturing solutions available, designed to redefine the future of manufacturing and provide businesses with the flexibility to grow and change at a pace and level that suits their changing business needs.
“This new software release is one of the most exciting steps forward to help manufacturers achieve integrated smart factory capabilities that will help them compete now and in the future. Its fully integrated IOT and MES capabilities fill a gap that could not be fulfilled by generic IoT platforms and, I believe, will truly accelerate the future of manufacturing data insights that are the foundation for realizing the benefits of Industry 4.0. Manufacturers no longer need to choose between investing in an IoT Platform or in a MES - they can leverage them both in one complete solution. It is a real game-changer,” Almada Lobo concluded.