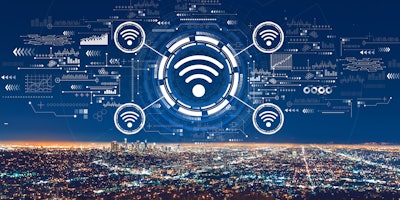
Historically, the manufacturing industry has avoided widespread integration of automation or Industry 4.0 technologies within their operations, feeling like the process would mean increased costs for implementation or starting from square one. But more recently, the industry has recognized the benefits of automation for increasing throughput, reducing staff burnout, and improving operational efficiency. In fact, a recent study and survey found that the warehouse automation market is set to expand to over $69 billion by 2025, and 85% of respondents plan to deploy some sort of automation in the next 12 months.
Deploying Automated Guided Vehicles (AGVs) and Automated Mobile Robots (AMRs) within manufacturing operations is a huge organizational and economic growth opportunity. AGVs and AMRs ensure the seamless transportation of materials throughout warehouses and help reduce overall operational costs. Echoing that sentiment, 70% of companies that have deployed AMR technology recorded considerable improvements to performance metrics, including productivity, cycle time, and inventory efficiency.
While there is growing adoption of mobile robot technology throughout the industry, one piece of the puzzle that requires increased education is mobile robot charging strategies. Charging is a significant consideration when integrating mobile robots within a facility. Wireless charging – or inductive charging – in particular, is becoming more popular as it cuts down on the need for manual charging equipment, but there are still challenges that come with ensuring seamless integration.
In this piece, we will look at ways that original equipment manufacturers (OEMs) can proactively solve these challenges, keep mobile robots running efficiently, and help facilities capitalize on the benefits of the equipment.
Start with an Integration Plan
Before choosing a wireless charging system, OEMs need to work with facility managers to set an integration plan to ensure that the charging infrastructure seamlessly fits into the existing or planned AGV/AMR systems and the overall facility environment. Integration planning involves determining whether a wireless charging solution will be compatible with the AMR and AGV models that an OEM is working with. If significant modifications need to be made to fit with the mobile robot models, that charging solution may not be the best fit as it could require expensive changes or could mean that the infrastructure will simply be incompatible with the mobile robots.
Additionally, a successful integration plan includes considering where a wireless charger should be placed on the manufacturing floor. This will minimize downtime and support the continuous and efficient operation of the robots.
Consider Flexible and Modular Charging Solutions
Another important factor for OEMs that can reduce problems with integrating wireless charging infrastructure is looking for flexible and customizable solutions. Space on mobile robot vehicles is limited, and charging solutions are often one of the last pieces OEMs consider. Therefore, it is essential to work with vendors to find flexible solutions. In this case, it might look like a charging solution that can be mounted below, on the sides of, or even integrated into the body of the vehicles. These different mounting types also transfer to different mounting needs for stationary charging. Identifying solutions that have different power connection selections and the ability to support different travel requirements allows OEMs to find the perfect fit for their vehicle.
As mentioned above, significant modifications to charging infrastructure can be costly and unnecessary. Finding a supplier who proactively offers customization in wireless chargers, like charging pad cables that can be cut to length at a customer site for flexible charging station mounting locations or different communication protocol support, making it easy to integrate into OEM-specific vehicles, is a big advantage for OEMs.
Prioritize Data Security
As the manufacturing industry increasingly relies on automation, data security will remain a crucial piece of the puzzle to ensure that mobile robot vehicles run efficiently, and information is safeguarded. Communication between a wireless charger and a vehicle must be secure. This security helps to minimize disruptions in operations, which is essential for keeping production schedules on track. Disruptions also lead to unnecessary downtimes, as facility managers must ensure the charging pad is functioning correctly and that the AGV can complete its tasks.
Data is fundamental to the efficiency of a facility as it can help to identify bottlenecks, support future decision-making, and keep operations running. As an OEM, look for wireless charging infrastructure with inductive communication in the charging pad that is isolated from the facility's Wi-Fi network to keep the flow of communication under control.
Future-Proof Operations
While many manufacturing facilities rely on standard equipment and processes, innovation will inevitably continue to arise and pave the way for more efficiency and growth. It’s critical for OEMs and facility managers to anticipate change and implement infrastructure and processes that can be updated and changed with the times.
When it comes to wireless charging infrastructure, OEMs should look at deploying opportunity charging solutions, which take advantage of any natural pauses in the workflow to charge the battery or supercapacitors. This maximizes the availability of the equipment for a positive ROI. Additionally, these solutions tend to scale very well, allowing users to add vehicles quickly and utilize distributed charging systems.
Find a Trusted Partner
As the manufacturing industry evolves and AGVs and AMRs are increasingly implemented into warehouses, it will be more important than ever for OEMs to partner with suppliers who understand the challenges they face regarding equipment compatibility, data security and safety, and what will be coming down the pike. Charging infrastructure is an integral part of making sure AGVs and AMRs carry out the correct tasks, so finding a partner who keeps a finger on the pulse of the industry and works directly with OEMs and facility managers to find the best solution for their needs will help anticipate future problems and solve them proactively.