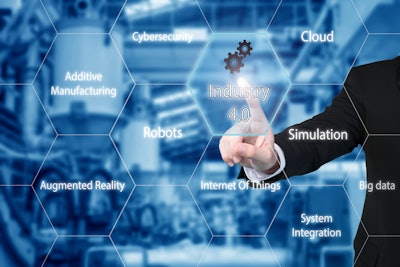
Long before the days of the pandemic and industry disruption, manufacturing businesses were already realizing the benefits that Industry 4.0 technologies can provide when adopted at scale. Benefits like downtime reduction, throughput increases, labor productivity improvements and more can be seen when leveraged correctly. In fact, one survey indicated that 94% of manufacturing companies credited Industry 4.0 with helping keep operations running smoothly during crisis, in addition to boosting efficiency and safety.
Much of this efficiency can be attributed to the hallmark of Industry 4.0 – increased communication capabilities. At its core, Industry 4.0 allows information to be transmitted like never before, relying on foundational infrastructure to connect all the pieces of a completely interconnected manufacturing and supply chain system. When all the components of a business can share data and talk to each other, a more holistic view of operations is available and better business decisions are made.
So, where does this leave the businesses that haven’t prioritized digital transformation until today? Automation, mobilization and interconnectivity are critical components of modern operations, and Industry 4.0 promotes the integration of all these pieces. The good news is that operations don’t have to come to a screeching halt to implement Industry 4.0 technologies into a facility.
Here are three steps to consider to bring your operations into the future with Industry 4.0 – and keep your business moving during the process.
1. Create your vision.
It’s essential to first consider your end goal for Industry 4.0. Take stock of your business challenges. Where can automation, mobilization and interconnectivity support operations? What parts of your facility and processes could use updating, including needs and wants? Where do you have disparate data that needs to connect? Think about where you lack visibility. Make note of any current pain points that must be addressed, like repeated failures in a particular workflow.
At the same time, think beyond the “need-to-haves” and consider “nice-to-haves,” too. For example, even if you’re satisfied with your current fulfillment efficiency, it’s possible that Industry 4.0 could drive improvements and enable growth.
This contemplation will determine your vision for where Industry 4.0 can be reflected in your unique setting. Once you have a vision for your Industry 4.0 adoption, it’s time to evaluate your parameters.
2. Evaluate your parameters.
You can move on to more granular characteristics once you’ve determined the ideal “big picture.” Assess your current systems, requirements for new technology and potential challenges. Looking at your existing infrastructure, how is power or data transmitted? Are there any gaps in the current infrastructure that would need to be addressed? In many cases, there are Wi-Fi dead zones or areas with RF noise, which are important factors. Assess your current systems, requirements for new technology and potential challenges. Looking at your existing infrastructure, how is power or data transmitted? Are there any gaps in the current infrastructure that would need to be addressed? In many cases, there are Wi-Fi dead zones or areas with RF noise, which are important factors.
Physical parameters come into play, as well. If mobile devices are part of your vision, would their travel paths be consistent or variable? What about obstacles, like workers operating in the same environments? When considering requirements for new technology, think about any data and security needs. This step is crucial because it establishes the differences between your vision and current processes, systems and capabilities.
3. Determine your infrastructure needs.
After outlining your operation’s future and present in the first two steps, infrastructure will bridge the gap. Think about implementing Industry 4.0 like conducting roadwork. If a highway needs to be updated, it’s not shut down completely. Traffic continues to flow while an old road is repaired or a new road is built, albeit with modified traffic patterns or minor inconveniences. As parts of the project are completed, they are opened to traffic. Once the project is finished, the benefits ultimately outweigh the disadvantages, like obstacles that workers had to overcome or drivers' annoyance during construction.
Both roadwork and Industry 4.0 are gradual, necessary processes that involve detailed planning, intentional execution and undeniable benefits. In manufacturing and distribution, your infrastructure is like a highway, allowing information to flow between various sources and destinations. Your pieces of equipment are like cars on the road, added to the new highway over time. Establishing the appropriate infrastructure lays the foundation for success.
Expert partners are especially beneficial during this step, as they can share options and advise about what is most compatible with your vision, current systems, logistical considerations and more. It’s common that Industry 4.0 is strongly associated with Wi-Fi infrastructure.
However, Wi-Fi can have drawbacks, like the potential for outages, cybersecurity risks, inconsistent coverage and limited range. Depending on your previously defined needs and challenges, it might be wise to consider infrastructure options beyond Wi-Fi. Additionally, many providers can leverage or expand your current systems to incorporate modern technology more seamlessly, reducing the impact on productivity and budget. Educate yourself about infrastructure options and consult a trusted, skilled partner to choose the best foundation for your success.
Whether to optimize throughput, safety, asset performance or other components of your operation, Industry 4.0 enables connectivity between devices and their operators. As a result, companies across manufacturing and distribution are opening the door to a diverse range of newfound capabilities. By preparing infrastructure for the incorporation of Industry 4.0, you can start your transformation journey on the right foot and keep your business moving into the future.