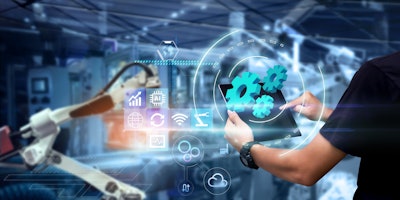
It is a remarkable and somewhat concerning fact that some forecasts project that the manufacturing sector could have a shortage of 2.1 million skilled jobs by 2030.
One of the ways that manufacturers can adapt to the looming labor shortage is by becoming more efficient, and one of the best ways to make that happen is by continuing to be smarter and more strategic about integrating technology into manufacturing environments. That process is already well underway with the implementation of Industry 4.0, a collection of emerging technologies that includes cyber-physical systems, the Internet of Things (IOT), cloud computing and cognitive computing/artificial intelligence (AI).
What gives manufacturers reason for optimism in the face of a potentially significant labor shortage is the next step in that evolution: Industry 5.0. The promise and potential of Industry 5.0 heralds a potentially transformative moment for an industry that is (somewhat belatedly) becoming more sophisticated in deploying technology in game-changing new ways.
Here's how we got here and what that next step could look like:
Meaningful change
The most significant impact from the implementation of Industry 4.0 in the manufacturing space was not from the raw power of the technology alone, but from the way in which those technologies can be seamlessly integrated together. The result is a newfound ability to create manufacturing environments that are virtual, interchangeable, more decentralized and more modular—providing real-time data and flexibility in a newly connected production environment.
Those elements—connectivity, transparency and immediacy—lead to newfound capabilities. Companies can operate faster, more efficiently, and more flexibly, with newly nimble customization capabilities and data-gathering that unlocks the ability to make continuous refinements over time. Essentially, Industry 4.0 brings IT together with engineering and operations in newly impactful and synergistic ways, giving industry decision-makers not only new clarity on their operations, but a drastically expanded ability to make thoughtful changes and improvements.
The next big thing
If Industry 4.0 was the introduction of new technologies into the manufacturing space, Industry 5.0 represents something very different, but equally ambitious: bringing technology into the human space. That critical connection is particularly important in a manufacturing environment, where even the most powerful technologies have limitations, and human judgement and decision-making remain critically important. While digital tools can heighten efficiency and promote process optimization, no tool can entirely replace human operators. Which is what makes Industry 5.0 so important.
At the heart of Industry 5.0 advances is the application of user experience (UX) methodologies to human machine interfaces (HMI)—something that was largely overlooked in Industry 4.0’s emphasis on emerging technologies. In simple terms, the UX describes how humans interact with the tech tools designed to make their work easier. The Manufacturing UX Revolution is an acknowledgement that automations, digital tools and robotics may have fundamentally transformed how manufacturing environments function, but operators remain the ultimate interface between people and plant. While intelligent machines, IoT and AI can have profound impacts on manufacturing processes, the technology alone cannot ensure that operators see streamlined experiences.
An emphasis on UX design (specifically visualization tools, control, and information systems) will present cyber-physical systems with intuitive interfaces that enable operator success by making manufacturing processes more natural, more intuitive and more user friendly, shortening both the literal and figurative distance between man and machine.
The way forward
Industry 5.0 is less a revolution than an evolution, but it’s a critically important step because it connects two formerly disparate pieces in a formula for smooth and seamless functionality.
Even more exciting, bridging the gap between technology and people has the potential to mitigate the worsening labor shortage—not just by boosting efficiency, but by aiding in talent and labor recruitment. Because Industry 5.0 is more adaptable to human needs. Every facility is different, and every manufacturing professional plays a different role. The ability to adapt a specific piece of tech to each company and each facility—and to subsequently build unique user experiences for the variety of plant personas and create the most simplified/ streamlined experience possible—is a game-changer. When done well, it brings people into the center of Industry 4.0 innovations and prioritizes their health and wellbeing—not to mention their workplace experience.
To some extent, the labor shortage isn’t so much that we’re missing humans, but rather lacking preparedness. Industry 5.0 encourages bringing the technology to the human. By breaking down training barriers and making technology and manufacturing markets and environments more human friendly, we increase utility—but also comfort and connection.
Traditionally, part of the hesitancy for current manufacturers looking to upgrade their technology stack is the perception that it requires a great deal of overhead and costly investment without a clear ROI. The good news is that the value proposition is becoming clearer. Even better news is that even slow adopters can now implement powerful tech with a highly developed UX already in place. Manufacturers are unlikely to get to 5.0 alone. They would be wise to partner with a proven HMI specialist with a demonstrated track record of anticipating Industry 5.0 changes and consistently putting people at the center of technology. That notion—human-centered tech—is at the heart of Industry 5.0 and will almost certainly shape the future of the manufacturing space for decades to come.