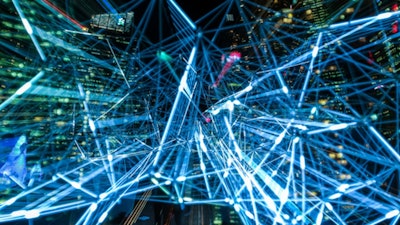
Industry 4.0 isn’t a new term. Remarkably, the cluster of technologies it describes—which includes cyber-physical systems, the Internet of Things (IoT), cloud computing and cognitive computing/artificial intelligence (AI)—is nearly 10 years old. And, while significant technical advances continue to be made on a nearly daily basis, many of the most exciting developments in this space have less to do with the technology itself, and more to do with how that tech is integrated and applied to optimize utility and maximize impact.
The coveted digitalization or digital transformation that many companies are striving for requires not just the technical architecture, but also a deeper understanding of how to leverage the unique potential of Industry 4.0 technology. It begins with recognizing that seamless integration, real-time communication and the ability to create manufacturing environments that are virtual, interchangeable, more decentralized and more modular has the potential to radically reshape the industry landscape.
With that big picture in mind, let’s take a closer look at how those trends are playing out, and what kind of Industry 4.0 advances will shape the months and years ahead.
Misunderstanding—and a gradual realization
General uncertainty and lack of understanding about exactly what Industry 4.0 is and how best to deploy it has slowed the rollout and blunted the impact for some early adopters. The technology has matured in recent years, but more importantly, growing numbers of companies are recognizing that it’s not enough to invest large amounts of time and money installing smart sensors and new systems without first taking the time to make sure those upgrades are both smart and strategic. The insight that the technology is just one piece of the puzzle has been a critical development in unlocking the full potential of Industry 4.0-driven digital transformations. Greater connectivity, transparency and immediacy are achievable. Greater speed, enhanced flexibility and customization and extraordinary new efficiencies are possible. But, only for those who spend less time asking what and more time asking why—and how.
Information is power
One of the signature game-changing elements of Industry 4.0 is its ability to unite IT with engineering and operations in ways that create valuable new synergies between two formerly separate operational spheres. Which is why data gathering, data management and data analysis have proven to be pivotal when it comes to helping companies take big leaps forward using Industry 4.0 solutions. Growing numbers of businesses are investing in the infrastructure and expertise required to do just that. Using real-world metrics and measurables to understand what tech upgrades will have the biggest impact and how they can best be integrated into existing systems is one of the most important and impactful new Industry 4.0 trends.
Pandemic purpose
The historic and unprecedented challenges businesses have had to grapple with as a result of the ongoing COVID-19 crisis have made it clearer than ever that Industry 4.0 advances are urgently needed. Virtual workforce models, unreliable supply chains and unavoidable operational interruptions have highlighted the value of whole-process visibility. In the chaos and uncertainty of a pandemic, access to holistic real-time business info isn’t a luxury, it’s a necessity. Ironically, the silver lining of pandemic-driven challenges has been the fact that most companies have been forced to endure a kind of involuntary stress test -- ultimately providing decision-makers with new insights into their systems and operations. Armed with this sophisticated new understanding and self-awareness, they can make smarter decisions about the connectivity solutions required to meet their needs.
Game-changers
Among the most important and impactful Industry 4.0 trends are the steps that prospective adopters are taking to enhance their understanding and successfully identify and deploy game-changing new tech tools:
· Holistic modeling. Decision-makers are taking a clear-eyed look at their operations before investing in any new tech. That self-examination extends well beyond the manufacturing floor and should ultimately include a details model of front-, back- and middle-office functionality. In other words, not just technical architecture, but functional workflow. The most successful digital transformations may start at the top, but are cohesive and connected to all facets of the business, from customer relations, marketing and sales to IT, manufacturing and distribution.
· Speed and agility. In a space that continues to evolve with impressive speed, traditional five- and 10-year corporate planning is simply obsolete. The best adopters of Industry 4.0 tech solutions are replacing long-term planning with long-term vision. They establish long-term goals and have a clear sense of the big picture, but also develop specific short-term plans as part of an attempt to become more agile and responsive to emerging trends and technologies.
· The human element. Finally, and perhaps most importantly, is the recognition that an optimized, seamless and impactful digital transformation is less about Industry 4.0 tech and more about the people using it. From interface designs to enterprise rollouts, the best new Industry 4.0 tools and strategies are based on an approach that puts the user first and recognizes that fully leveraging the human potential of next-generation systems and solutions is the most effective path to sustainable success.
Click here to hear more about how humans and automation can work together: