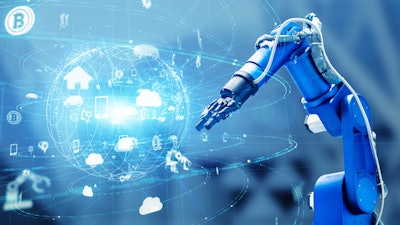
Has productivity reached its limits?
Nearly 250 years of manufacturing evolution led to massive productivity gains, but manufacturers must now ask themselves: What happens when you can’t produce more with the assets and people you have? At the same time, the Coronavirus disease (COVID-19) pandemic has demonstrated how a global crisis can throw supply chains into chaos, thus accelerating interest in creating automated systems that don’t require human beings to be put at risk to keep businesses running.
The manufacturing industry is betting that “Industry 4.0” – sometimes called the Fourth Industrial Revolution – holds the solution to both these issues. McKinsey has predicted that Industry 4.0 will have a $3.7 trillion economic impact by 2025. A combination of smart devices, analytics, artificial intelligence (AI) and machine learning, Industry 4.0 enables manufacturers to optimize maintenance, intelligently schedule workflows and, when combined with robotics, achieve the ultimate goal of Industry 4.0: “lights-out manufacturing.”
Imagine a future where production can be run at all times with minimal human intervention. Using machine learning and a workflow platform, intelligent decisions can then be made for scheduling to improve efficiency. Machines already being used for production can be connected with automation on the factory floor to keep humans out of dangerous situations. When combined with advanced robotics, this could mean a future where factories hum along day and night, without need for workers who could be injured – or infected – on the job.
Of course, achieving smart manufacturing is easier said than done. Businesses often have to contend with disconnected business systems patched together over years, if not decades. There may be a lack of a unified data strategy, reluctance from executives to race toward this ambitious future, and a lack of long-term planning to achieve this lofty goal.
However, as we have seen across many industries, goals that once seemed decades away are now being fast-tracked, as the fall-out from the COVID-19 pandemic forces businesses to rethink how they operate and what they prioritize. Lights out manufacturing is now within reach, especially if businesses take advantage of existing technology to prepare themselves for the next step. Here are three ways that companies can prepare for the future of manufacturing today.
The future of productivity is now
First and foremost, manufacturers must realize that they cannot wait to begin their transition to Industry 4.0. According to the Manufacturing Report of 2020, more than 90% of consumer goods manufacturers see digital transformation as a top priority.
What does it mean to think about Industry 4.0? It doesn’t require an immediate jump to radical futurization, as some executives fear. It means embracing the steps we can take today to make greater transformations possible in the future. Taking advantage of automation, intelligent systems, and connectivity on the manufacturing floor now will pave the way to greater use of automation in the future. Linking operational and IT systems together today will provide greater insights into what your business needs will be in the future, so that your business can take advantage of innovations that speak directly to your future goals.
Investing in technology now can feel like a risky strategy when so many of the benefits will be reaped down the line. But when it comes to preparing for Industry 4.0, that’s not necessarily the case. As the Manufacturing Report points out, the MIT Center for Information Systems Research (MIT CISR) finds that future-ready companies enjoy margins 16% higher than the industry average. However, as the report goes on to say, “43% of businesses are encountering so many roadblocks, they’re now reporting digital transformation fatigue.”
Manufacturers looking to thrive in the future must push through these roadblocks, which takes me to my next point.
Take advantage of the changing environment to embrace innovation
The COVID-19 outbreak has been a great catalyst for change across industries. Manufacturers must embrace this moment to take stock of their strategy from a long-term perspective. Companies must pause to consider how they will compete in the new environment in which we all find ourselves.
To give one example, many manufacturers have realized that an inability to have front-office staff control operational issues remotely is a great disadvantage.
Focus on what productivity means to you
There are many measures for productivity: perhaps you are hoping Industry 4.0 will lead to lower overhead, greater flexibility or higher quality. Whatever the answer, making Industry 4.0 work for you is not about digital for digital’s sake: it’s about connecting your corporate strategy to the benefits connectivity can provide.
To take one of the above examples, one benefit manufacturers can expect from their future-ready work is increased quality. By leveraging artificial intelligence and IoT device data, companies can easily do more analysis of products to inform quality. Imagine being able to monitor not only major indicators, but smaller, industry-specific indicators, such as the sound a piece of ceramic makes when hit with a small hammer. This type pf precise monitoring will enable manufacturers not only to reduce breakage and other issues, but also to provide more value-added services based on the data drawn from those products.
Or perhaps you’re concerned about security. More and more manufacturers are beginning to understand that cloud-based solutions, vital to the eventual move to Industry 4.0, provide a more secure environment. Many manufacturers, which have experienced ransomware attacks, move to the cloud because cloud-hosting companies are built to ensure a secure environment.
Whatever your productivity needs, embracing incremental moves toward Industry 4.0 today will help you achieve more tomorrow, while improving your bottom line in the short term.