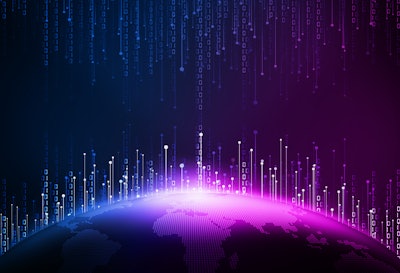
Although not as common as at the height of the COVID-19 pandemic, local, regional, national and international supply chain disruptions remain a concern for manufacturers, their customers and consumers. To overcome these challenges, the logistics process has become smarter, faster, and more efficient by automating operations, adopting technology, and forging partnerships that build resiliency.
Automating Operations
Manufacturers continue to expand the use of automation on the production line and are adopting it in the warehouse.
Robotics is often the automation tool of choice for applications from initial input to pallet unitizing. Most consumer-packaged goods (CPG) companies (84%) use robotics in their operations, and this number will rise to 93% by 2027 as forecast in an infographic.
Implementing robotics can achieve multiple goals:
- Reduce labor and repetitive tasks
- Increase speed and productivity
- Achieve repeatable quality and consistent product handling
- Improve operator safety
- Minimize waste and human error.
Today’s robots and collaborative robots (cobots) cost less and are more intelligent and durable, significantly faster, and easier to program and operate, reducing the operator skill level required for successful deployment. New artificial intelligence (AI) capabilities and accelerated computing power have substantially accelerated path planning, optimizing, and running. This has opened the door to installing robots for applications in processing, primary packaging, secondary packaging and transport packaging, where automation was not previously feasible.
There is a wider array of systems designed to food industry standards and more choices for smaller firms, who are new to robotics and need systems that can be installed and run with minimal training. Human/machine interfaces are more user-friendly and often include resident support documentation such as setup and operation instructions, schematics, training manuals, troubleshooting tools, and access to OEM support. Setting up and running some systems right out of the box is possible without any special training. If the operator is familiar with a tablet or smartphone, programming and reprogramming can be accomplished quickly. This easy programmability is especially helpful in addressing the rising demand for more mixed packaging and smaller volumes.
Modular design allows systems to be scaled up as needs change. More functional end-of-arm tooling (EoaT) can pick a larger variety of shapes, reach deeper, and change more quickly from one tool to another.
The report predicts cobot sales will grow particularly strongly, with usage doubling from 27% in 2022 to 57% in 2027. Functional improvements such as vision, feedback sensors, self-learning, mobility and AI will spur adoption. Systems are increasingly compact, and many newer units are designed to handle heavier payloads at higher rates. Some systems can move payloads of 30 kilograms or more and automatically switch between standard and collaborative modes. On-board data collection enables operators to identify fault trends to improve productivity.
Material handling applications are expanding with the development of more flexible autonomous mobile robots (AMRs). Equipped with vision systems and 3D LiDAR (light detection and ranging), today’s AMRs can modify routes to avoid obstacles and move in tight spaces in dynamic environments. Mapping enables quicker commissioning. Narrow-width units navigate space-constrained floor space, and AMRs with all-metal bodies are designed to withstand harsh environments. Fast charging capability minimizes downtime.
Despite strong interest in robotics and lower prices, the report notes that challenges to adoption remain, including ROI justification and identifying appropriate applications. Additional hurdles to implementing robotics include supply chain delays and long lead times; internal shortfalls (time, skills, budget); calculating the total cost of ownership; scheduling downtime and resources for equipment implementation, training and performance testing; difficulty in recruiting skilled and unskilled labor; and OEM support for integration, training and service.
In the warehouse, direct-to-consumer (D2C) business models and labor shortages are spurring investment in advanced automation technology to enhance efficiency, quality and productivity, according to another report. Robotics, particularly automated guided vehicles (AGVs) and AMRs, supported by coding, labeling, and scanning technology, streamline material handling and help address demands for a greater variety of stock-keeping units and smaller, more frequent orders.
Building Resiliency
As manufacturers work to eliminate and overcome supply chain disruptions and meet rising demand for D2C shipments, manufacturers need to know where their products are at all times. Traceability technology, including labeling, scanning, and digitalized data capture and analysis, gives production, inventory and shipment visibility. This capability makes it possible to follow a product as it moves through the supply chain, identify potential problems, proactively prevent delays, expedite product replenishment and automate reordering.
Equipping labels with scannable barcodes, radio frequency identification tags or near-field communication technology, installing associated scanning equipment, and implementing data capture and analysis software make it possible to identify the correct package for an order, organize the shipment and track the package throughout its travels.
Working together, these technologies can:
- Improve business transparency
- Drive performance improvements and more effective integration across the value chain
- Enable new business models
- Support and drive innovation and sustainability.
According to the 2023 World Packaging Machinery report from PMMI Business Intelligence, this so-called “smart” packaging can also provide access to information about the raw materials used, facilitate recycling, and foster consumer engagement.
Implementing traceability and digitized inventory management and control in-house offers many benefits, but for smaller firms or warehouses that aren’t set up to efficiently accommodate D2C shipments, hiring a third-party logistics (3PL) or fourth-party logistics (4PL) provider may offer a better business case.
A 3PL provider can perform an array of transportation, warehousing and value-added functions such as customer service, order management, sales support, e-commerce and IT integration. Joining forces with a 3PL partner is particularly desirable for CPG firms with multiple plants producing different products. With 3PL support, the manufacturer can ship the products from each plant to the 3PL provider, and orders can be fulfilled from there, according to PMMI’s Packaging and Automation in the Warehouses of the Future report.
However, sometimes broader support is needed. When that happens, it’s time to hire a 4PL service provider which can manage the supply chain end-to-end via a network of 3PL operations. As a result, 3PL and 4PL distribution comprises up to 50% of D2C shipping by CPG firms, and the PMMI report predicts the use of these logistics partners will increase.
In fact, the 4PL segment already dominates, accounting for more than 62% of the global logistics market in 2022, according to statistics gathered by Facts and Factors. A projected 3.92% compound annual growth rate through 2028 ensures the 4PL segment will continue to dominate.
A strength of both 3PL and 4PL service providers is the increasingly data-driven nature of the operations. This addresses the growing demand from CPG companies for package traceability and assurance of on-time fulfillment. An array of emerging tools is evolving to support traceability and reduce theft, fraud and delivery errors. This includes sophisticated software platforms and smart labels with printable electronics, which replace manual barcode scanning with an automated process.
Benefits derived from a relationship with a 4PL service provider include faster fulfillment, operational efficiencies, cost savings, and expedited deliveries. In addition, the report notes that 4PL service providers can help reduce overhead, labor, and inventory costs, eliminate wasteful procedures, simplify the supply chain, and enhance purchase leverage through an extended supplier base.