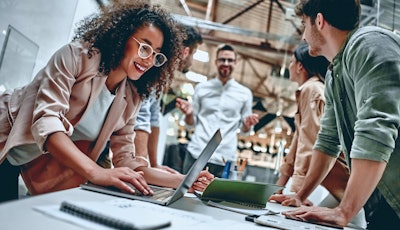
The world is about to be reminded again how dependent it is on efficient supply chains. The challenge of distributing COVID-19 vaccines to billions of people worldwide is one of the most significant logistical challenges in history – requiring unprecedented speed, precision and coverage.
Managing phenomenal demand in supply chains is a tough ask, as empty supermarket shelves demonstrated in the first weeks of the pandemic. But, we must be able to vaccinate as many people as possible, as quickly as possible – there’s no room for inefficiency.
However, as supply chain professionals know, even the best-run organizations – from medical equipment companies to online retailers – have struggled to overcome friction in their supply chain, which can prevent products and supplies from reaching end users. This isn’t just an issue facing vaccine deployment. Between increasing customer expectations for shorter fulfillment timeframes, lower tolerance for late or incomplete deliveries and growing costs and volatility, supply chain managers feel the pressure to exponentially increase on-time delivery rates that can be as low as 43%. Something needs to change, but how exactly can we create the resilience in our supply chains to deal with massive and often unpredictable disruption?
Finding friction
On-time orders have long been a key departmental metric, but the stakes are now much higher – being late with personal protective equipment (PPE) or the inability to coordinate vaccine delivery is not an option. Supply chain managers must be able to drill down on specific variants in a process and understand which broken links are most critical and causing friction. A single blocked invoice or credit check could prevent a hospital from receiving a respirator, and unfortunately, that may be hidden deep in the system with no way of notifying an employee to investigate and solve the issue.
The ability to analyze
Notably, healthcare supply chains are experiencing multiple challenges, while being beholden to a historic timeline. The challenges are undoubtedly dramatic, and also provide insight into issues other sectors are facing and how to overcome them. The ability to analyze what is happening across fragmented enterprise systems and see the reality deep inside individual processes offers breakthroughs that can be applied across just about any industry. Moreover, because the process analysis is connected to the business objective, users can be assured that they’re taking the most efficient and effective approach to achieve their desired business outcomes.
This can be done by leveraging the latest technology and working backward from the desired end goal – in this case, on-time delivery – and assessing how this can be accomplished or what will prevent it from happening. Artificial intelligence (AI)-powered technology can analyze the entire supply chain and flag potential problems before they appear. It can even automatically put contingencies in place to ensure a delivery target is fulfilled.
Until now, the obstacle has been that all enterprises run their core processes and operations through a mix of hundreds, and sometimes thousands, of individual systems. The complexity of this fragmented environment often limits organizations’ ability to execute (or execution capacity), which hampers business performance. A combination of process mining techniques, powerful AI and machine learning algorithms can analyze the processes running on these systems and identify execution gaps in real-time. This is done by drawing data from underlying systems to identify and measure the barriers that stop companies from reaching their full execution capacity. Systems can then be put in place to automate specific actions and navigate roadblocks – systematically removing any constraints.
Widening the net
These lessons apply across the board. In retail, seasonality has always created intense periods of demand. In the current environment, flagship days such as Black Friday present opportunities for retailers to make up for the loss in sales caused by the pandemic. Amazon Prime Day 2020 generated almost $10 billion in global sales — a 43% increase year-on-year. But, take away Amazon's near-impeccable reliability and that growth is not so certain. After all, in 2019, 84% of consumers said that they won’t return to a brand after just one poor delivery experience.
As retailers offer unprecedented deals, quick delivery and easy returns to remain competitive in the online world, customer expectations have simultaneously increased. In fact, 60% of consumers have higher expectations of their digital experience now than before COVID-19. To remain competitive, retailers must meet and exceed expectations by delivering products on time and providing excellent customer service. However, many are still struggling with the large-scale disruption caused by the pandemic and may not be prepared for the additional pressure created by a surge in online shopping on their fragmented supply chain.
For almost every business, the pandemic has exposed the fragility of their supply chains, with slight shifts in consumer behavior leading to widespread supply shortages.
Organizations have always experienced these issues though to a lesser extent and typically not all at once. The drive for maximum efficiency meant that many organizations hard-coded rigid processes into their systems and sacrificed full visibility in lieu of delivering faster. Unfortunately, that strategy has left many organizations without the agility required to adapt when even minor disruptions occur. With so many supply chains spanning countries and even continents, the pandemic's global nature affected vast numbers of businesses. By creating the ability to analyze and react to processes in real-time, organizations dependent on supply chains deliver the resilience that is so often discussed.
The importance of total visibility
In the big picture, making a company’s supply chain more resilient is another phrase for making a company more trustworthy, thus breeding greater customer satisfaction and saving businesses money. In such turbulent times, using the available technology to look at gaps in supply chains is essential for businesses to succeed and keep customers happy.
It's called the importance of total visibility -- being able to react quickly to live updates. This means businesses can find alternative vendors with faster delivery times or change their orders at the earliest possible stage to adjust to demand. Resilience is more than a buzzword. It means the capability to always have a Plan B ready if any of your suppliers cannot deliver on the orders.
Click here to hear more about visibility in the supply chain: