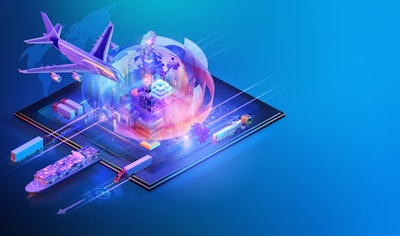
The global supply chain has focused on force optimization and the lowest costs for the last twenty years. That all changed when global regions and crucial suppliers shut down due to COVID-19. The global supply chain tried to adapt quickly and refocus on regional supply chains. Despite this adaptation, the world still faces myriad supply chain difficulties two years after the pandemic began. By nature, supply chains are comprised of many moving parts, which multiplies the chance for disruption. From more pervasive issues, like labor shortages and unrest, to singular events – like the United Kingdom’s biggest container port being hit by eight days of strikes– global supply chains are experiencing wide-ranging effects.
The new, post-COVID supply chain is still in the process of being built. While improvements have occurred, there’s still a certain level of fragility that makes predicting disruptions more difficult than in the past. The companies that are finding success in this uncertain world are the ones that have focused on resiliency in all lines of business. Every manufacturer and its supply chains are different but being agile with processing materials and creating greater visibility is key across all sectors.
New supply chain technologies
Technologies are playing a crucial role in helping supply chains undergo this evolution. The suppliers that are still working with previous methods aren’t as successful. It’s now about moving from being ‘connected’ to having ‘intelligent’ technology that’s automated, autonomous, and has end-to-end orchestration.
Businesses are using AI and machine learning to connect to machines and manufacturing lines to help make the supply chain more predictive. An upstream supplier readiness solution that’s semi-automated helps to better assess risks. Adaptive machine learning can optimize performance-related parameters, such as lead times and minimum order quantities, on a real-time basis. Data analytics tools are also being used to see where the disruptions can come from layers of the supply chain.
This proactive big-picture view —to figure out where problems are before they exist— is crucial. For example, businesses can prioritize based on revenue versus spend by looking at which parts of the supply chain impact revenue the most. By mapping out a process that gives a clear understanding of the current state of the supply chain, businesses can get ahead of potential issues and minimize disruption.
The uptick in nearshoring operations
For many decades, companies were moving their supply chain operations to Asia to cut costs but have since realized that nearshoring can help to transform their supply chains positively. According to Kearney's 2021 Reshoring Index, 79% of U.S. executives who have manufacturing operations in China have either already moved part of their operations to the United States or plan to do so in the next three years. This is true across a wide variety of industries, including automotive, semiconductor and industrial. Reshoring materials helps to shorten the supply chain, which then translates to fewer supply chain disruptions.
It would be remiss not to acknowledge that nearshoring operations have also led to new challenges, with labor shortages being one example of this. Now, U.S. companies are having to navigate how to build up talent to assist with labor operations rather than sourcing from abroad. Matching the strength of other markets means building and rebuilding essential skillsets. As part of nearshoring, U.S. companies must also invest in upskilling their workforce, as well as recruiting and retaining next-gen talent, for a more digital world.
Competing for talent
All suppliers—from manufacturing to distribution plants—are having trouble finding and keeping talent in traditionally blue-collar jobs. PwC's 2022 supply chain survey found that 58% of companies are seeing higher-than-normal turnover among supply chain employees, and only 23% fully agree that they have the necessary digital skills to meet future goals.
The era of working from home has certainly played a contributing factor to the labor shortage; however, factories and distribution centers often require a physical presence. For nearshoring to work, companies need employees with the skills and expertise to accelerate that innovation at home. Businesses can start by mapping their existing employees’ competencies and then make a plan to build out their workforce from there. For example, our main priority is focused on our employees' needs and giving those in the factories and distribution centers access to digital training tools to build their skills. In doing this, we’re helping to optimize operations while adhering to the needs of our employees. We’re living in a new world which has caused us to reevaluate the needs of our employees. The key for businesses is to get creative in how to attract new employees and working with them to create an environment that best aligns with their position to help them retain the talent and keep their digital skills current.
The evolution of the supply chain
There is no shortage of questions or factors to consider when it comes to improving the supply chain for the future. Businesses are starting to multisource, looking at all the nodes of the supply chain and tiers of people who form this resource. Vulnerabilities are being better identified and collaborations are happening to make managing supply chains more successful. Companies are asking questions like, "how can products be redesigned to better align with the way the supply chain currently works?" or "Are there ways to better work together strategically or operationally with vendors?"
As the supply chain continues to evolve in the face of new challenges, companies can stay ahead of the curve by doing regular roadmap alignments and implementing technologies that allow them to anticipate change. Ultimately, the companies that are proactive, collaborative and agile will have business continuity and success.