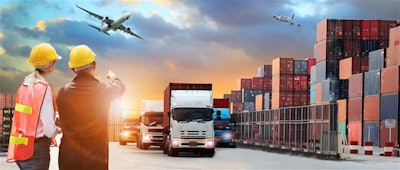
Whether supply chain leaders are trying to figure out the optimal supplier network, where to locate inventory, or how customer demand patterns will be affected by a new product launch, they need more than a simple review of historical data. Factoring in the varying key performance indicators (KPIs), plans, and data inputs requires a structured approach to asking “What if…?”
To build the capability to model and analyze varying outcomes, organizations can turn to scenario planning. Scenario planning and analysis is a process of examining and evaluating possible events or scenarios that could take place in the future and predicting the various feasible results or possible outcomes. Today’s modeling and scenario analysis combines artificial intelligence, analytics, and data visualization, while leveraging cognitive computing capabilities to process data into outputs.
In addition to reviewing the role that scenario planning plays in supply chain, this article includes cross-industry data to show the tangible benefits this practice can help organizations achieve.
How supply chain organizations use scenario modeling and analysis
Done well, scenario modeling and analysis help supply chain planners test assumptions, identify risks, and evaluate options in the context of factors such as cost drivers, supplier relationships, marketplace disruptions, and operational constraints. Simply put, testing out different scenarios helps supply chain planners make more informed decisions. While some organizations have used scenario planning, modeling, and analysis for decades, the supply chain disruptions of 2020 and beyond have made it more important than ever to imagine and plan for different possible futures.
To integrate scenario modeling and analysis into supply chain planning, supply chain functions should:
- Leverage the organization’s available analytics expertise to establish and advise on supply chain planning simulations.
- Select a scalable simulation tool that fits the supply chain’s needs.
- Establish a step-by-step data selection and simulation model for standardized use.
- Exercise informed judgement and common sense when critical uncertainties are at play.
- Track indicators that a specific scenario is likely to occur.
- Apply consistent standards for factoring scenario outputs into decision making.
The ultimate goals of these efforts are to simulate the impact of decisions before they are instituted, predict operational challenges (e.g., capacity limitations), model new strategies to pre-emptively address impacts, and evaluate options with no available historical data. Technology is not doing all of the work—humans continue to play an important role by judging scenario analysis in its full context.
Scenario planning and analysis drive better supply chain outcomes
APQC research finds that most organizations are trying to integrate scenario modeling and analysis into planning activities to some extent, but relatively few (12 percent) have achieved this to a very great extent (Figure 1). More than 40 percent of surveyed organizations only have these capabilities to a small extent—or not at all.
Scenario planning capabilities make a big difference in the performance of key supply chain processes. For example, when customers routinely expect lightning-fast ordering and shipping, organizations with shorter customer order cycle times will be at a competitive advantage relative to those that are slower. APQC finds that organizations that can model and analyze scenarios to a significant or very great extent have faster customer order cycle times than organizations that model and analyze scenarios to little or no extent (five days versus 11 days).
Scenario modeling and analysis also help organizations to achieve higher finished goods inventory turns relative to those that use scenario modeling to little or no extent (9.6 versus 8.2 turns). While 2020 taught organizations the danger of having too lean an inventory, having too much inventory sitting on the shelves carries its own risks. Organizations that use scenario modeling and analysis to a greater extent not only move more inventory, but also get paid faster for it through quicker cash-to-cash cycle times (49 days versus 60 for those that barely use scenario modeling and analysis).
Scenario modeling and analysis drive deeper insight into the business
While no one can perfectly predict the future, organizations derive many benefits from the planning, preparation, and relationship building that takes place when scenario modeling and analysis are done well. For example, one of the benefits of simulating multiple scenarios and optimizing models is that doing so allows supply chain leaders to evaluate tradeoffs among factors such as costs, fulfillment performance, and service. Organizations that simulate and optimize models to evaluate these tradeoffs to a significant or very great extent outperform those that don’t, with:
- Faster customer order cycle times (11 days versus 6),
- Higher finished goods inventory turns (9.6 versus 7.7), and
- Shorter cash-to-cash cycle times (53.5 days versus 63 days).
Effective scenario modeling and analysis also require an organization to understand its suppliers, the conditions under which the organization might need alternate suppliers, and who those alternate suppliers might be. It’s also important to understand how fast alternate suppliers can get up to speed, and what their capacity is. This does not mean that an organization needs to have an alternate for every supplier. With limited time and resources, leading organizations focus on finding alternate suppliers for the materials that are attributed to the greatest amount of sales contribution, as well as those that are most likely to cause bottlenecks (whether because they are patented or available from limited sources). By identifying the highest risk materials, procurement teams can focus the bulk of their resources on developing robust business continuity plans for these suppliers.
Moving forward
In a business environment marked by frequent disruptions, organizations that have the plans, knowledge, and processes to shift to alternative plans faster than others stand to gain significant competitive advantage. Organizations that develop the ability to model and analyze different scenarios—and test out those scenarios via “war games”—are more likely to have these plans in place before disruption hits the business, which means they will lose little or no time while others are scrambling to recover. Regardless of what the future brings, these organizations will keep serving customers faster, bringing in cash more quickly, and building relationships that pay off in a big way when disruptions occur.