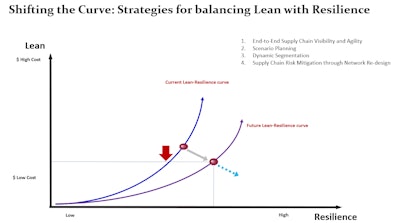
For decades, the lean strategy, which was largely shaped around the 40-year-old Toyota production system and principles of eliminating waste, cost savings and operational excellence, has played a critical role in improving supply chain efficiencies. By making traditional supply chains as lean as possible, companies could supply goods quickly and cost-effectively, while reducing inventory levels, improving operational effectiveness, reducing their cost of goods sold and increasing asset utilization. The lean strategy was originally based on assumptions around low demand fluctuations and no supply disruptions to ensure a smooth production and just-in-time deliveries
However, neither of these assumptions hold true in today’s volatile, uncertain, complex and ambiguous (VUCA) environment where there’s unexpected demand and supply swings. Many organizations have recently discovered that their supply chains were too lean and fragile and not robust and resilient enough to react to the extreme demand and supply variations caused by Brexit, tariffs, North American Free Trade and the most recent Coronavirus disease (COVID-19) pandemic. Just being lean alone is no longer an option and recent events, including the COVID-19 pandemic, have exposed serious flaws of entirely lean networks as regards to impact, severity and duration of the disruption. On the other hand, with shrinking margins and cutthroat competition where profitability is key, being resilient by adding buffer inventory, building excess capacity, or increasing labor to solve problems is not sustainable either.
With a second wave of Coronavirus on the horizon, supply chain business leaders need to rethink the cost of risk and invest in operations that make the supply chains lean, resilient, agile and responsive at the same time. This means being able to meet customer demand with a supply chain that is intelligent enough to proactively identify problems, robust and resilient enough when faced with disruptions, agile enough to respond quickly to marketplace changes, and efficient enough to improve planner productivity and reduce costs.
Organizations that will emerge the strongest in the wake of the COVID-19 will be the ones that have successfully balanced lean and resiliency in their supply chains. It is not a matter of choosing between lean or resilience, but rather shifting the curve, increasing resiliency and becoming lean at the same time.
Here are a few strategies that can help supply chain leaders shift the Lean vs. Resilience curve and find that happy medium:
1. End-to-end supply chain visibility and agility
It’s not smooth sailing, but a “cold restart” is necessary as companies try to coordinate activities at the same time across different regions.
End-to-end visibility will be essential in order to anticipate disruption in the flow of raw materials upstream as well as finished goods downstream to fulfill customer demands. When you can visualize the entire flow of goods across suppliers, factories, distribution centers, distributors, retailers and customers, you can measure the impact of supply, demand and disruptions in real time, and come up with proactive risk mitigation plans that are simultaneously both lean and resilient. For example, once disruptions are predicted, artificial intelligence (AI)-supported “control tower” technologies have the power to recalibrate plans in real time using what-if scenarios to mitigate risk and maximize financial outcomes. Backed by AI and machine learning, these overarching control tower solutions enable companies to make trade-offs, balance various outcomes and respond with extreme speed and agility without human intervention.
In the event of a missed part delivery, digital control towers can weigh such options as expediting a replacement from the original location or shipping from an alternate location. They can evaluate the speed of different carriers and routes to minimize any negative impact caused by the disruption, thereby enabling the most cost-efficient outcome which will help the organization to quickly and proactively recover from the potential disruption.
2. Scenario planning
No one knows for sure whether it is going be a U-, V- or W-shaped economic recovery. However, organizations that proactively come up with robust contingency plans based on different economic recovery outlooks by understanding cash flow, profit and loss, and balance sheet impact, will be able to ride the waves of uncertainty instead of being overpowered by them.
Proactive scenario planning will help the organization comprehend the demand upside that can be covered with the current supply picture and percentage of demand that will be unmet in the event of a supply disruption. The keys to planning and executing smooth operations are understanding how these different demand realization and supply risk scenarios impact your business and coming up with business plans that are more balanced from a resilience and efficiency perspective.
There are predictive technologies available today designed to synthesize vast amounts of current and historical data to facilitate forecasting and event-driven scenario planning. Using AI and automation, supply chain planners can simulate scenarios and prescribe rather than just predict with the requisite speed and accuracy needed to navigate these turbulent times. Once the implications from cash flow, profit and loss, and balance sheet impacts are understood, the organization can assess the costs and benefits associated with proactively adding capabilities to increase supply chain resilience.
3. Dynamic segmentation
Supply chains in the past have used a lean only “one size fits all” approach centered on operational excellence, with the goals of increasing efficiency, reducing waste, and reducing or eliminating non-value-adding activities. As enterprises continue to navigate a period of unprecedented disruption, further consideration must be given to segment strategies that are aimed at risk mitigation for different segments, increasing resilience and determining how to operationalize these plans.
In the wake of the current COVID-19 crisis and demand-constrained environment, nimble organizations must build a plan to prioritize and protect their most valuable segments and customers based on margin, revenue, strategic importance and contractual obligations. Segmentation can help planners understand products with high-margin and high-opportunity for prioritization in case of labor constraints or material shortages caused by the pandemic. As market dynamics continue to change faster than most organizations’ ability to adjust, understanding changing customer demands and crafting attractive value propositions to serve them is becoming increasingly difficult. Machine learning (ML)-based dynamic segmentation, in which many factors can be analyzed simultaneously, can enable companies to dynamically segment their supply chain strategies and operations to balance cost-to-serve with the value to the business for each segment. Moreover, all supply chain processes and parameters are then dynamically aligned (including demand planning, inventory planning, master planning, allocation planning, order promising and sales and operations planning) by marrying the cost to serve for each segment with its customer value proposition.
Dynamic segmentation that balances lean and resilience is the best way for companies to address their customers’ needs while meeting financial mandates. Using strategies like production postponement and risk pooling is a great example of lean and resilient practices balancing and complimenting each other. Balancing these strategies shifts inventories upstream of the supply chain which leads to reduction in finished goods inventory while simultaneously increasing resilience as inventory can then be proactively allocated to downstream locations which are seeing disruptions.
4. Supply chain risk mitigation through network redesign
In light of recent geopolitical events such as Brexit, tariff, North American Free Trade and the COVID-19 pandemic, organizations are increasingly looking to restructure their lean supply chain networks that were built for minimizing cost through outsourcing. As disruptions intensified early on during the pandemic, many businesses realized that they relied heavily on suppliers that were single-sourced and based halfway around the world. A Bank of America survey showed just how wide the remapping of supply chains may be. Analysts who cover 3,000 firms reported that companies in 10 out of 12 global industries (including semiconductors, automotive and medical equipment) have shifted, or plan to shift, at least part of their supply chains from current locations.
Developing a supply chain risk mitigation strategy includes business continuity plans (a set of contingencies to minimize potential harm to businesses during unexpected events) and understanding risk consequences by balancing the lean principles of efficiency while balancing cost with the resilient principles of impact on performance, time to recover and service levels trade-offs. The risk mitigation strategy should also include network re-design, creating sourcing and network design strategies to support your organization’s risk tolerance.
The goal here is to diversify manufacturing and suppliers across various regions instead of just use off-shoring, near shoring or on-shoring. Reconfiguring global and regional supply chain flows through a multi-sourcing and multi-shoring approach based on needs, cost, service and risk scenario analysis trade-offs, will help ensure the supply chains resiliency in the event of a disruption in a particular region. This will also help the supply chain recover quickly, and encourage a V-shaped recovery instead of a U-shaped one.
The “New Normal” of the post-COVID-19 world presents a unique challenge. As the speed, frequency, magnitude and intensity of disruptions including geopolitical events, climate-related disasters and public health crises continues to increase, organizations emerging the strongest will be the ones that can that see the current emergency as an opportunity and adopt both lean and resilience strategies into their operations. Technology has come a long way and it is now possible stay a step ahead of supply chain disruptions by improving the ability to rapidly ingest and analyze internal and external sources of big data, leverage machine learning and artificial intelligence for predictive and prescriptive analytics, deploy early-warning technologies, model risk scenarios and develop pre-programmed responses. Such organizations will be able to shift the lean vs. resilience curve, have a potent defense by being ahead of the competition by being prepared earlier, dip less in the event of a disruption, be agile and responsive and move faster to come out ahead of the curve.