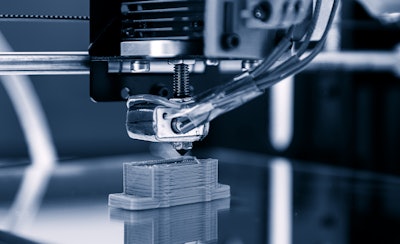
Sound familiar? Well, it should. Such hyperbole has been used ad nauseam in the past. Yet, this time around, things are different. The combination of two new technologies, additive manufacturing and generative design, promise to fundamentally redefine how products are engineered. Given today’s tightening constraints on development, that’s not only a good thing, it’s a great thing.
The purpose of this article is to offer the first glimpse into the implications of these two technologies on mechanical design. To begin, we have to start with how manufacturing is fundamentally changing and its implications on design.
The Radical Impact of Additive Manufacturing
What Exactly is Additive Manufacturing?
Additive manufacturing is a process by which material is added or joined to make a component. It stands in contrast with subtractive manufacturing, where tools are used to remove material from stock material, which includes all machining processes like milling, turning, laser-cutting and the like.
The Constraints of Subtractive Manufacturing
Before we can talk about the implications of additive manufacturing, we need to talk about the constraints of subtractive manufacturing. There are certain geometric challenges to using these production approaches. For example, if you use mill machining to make a part, you cannot have overhangs. That essentially means the tool couldn’t reach the material you need to cut. It’s inaccessible. Another impossible milling example is designing a space in a component completely surrounded by material. The tool couldn’t get to the middle of a part without plunging into the sides, thereby violating the design. The same holds true of latticed geometry and myriad other designs. Some simply can’t be made with subtractive manufacturing.
The Implications of Subtractive Manufacturing
All these constraints, of course, dramatically affect how an engineer designs. Throughout the process, they must develop geometry that can be produced. In some cases, this inhibits their ability to come up with designs that could address product requirements in a unique or innovative way. In many respects, their hands are tied. They only have a few options to develop a new design.
The Freedom of Additive Manufacturing
Making components with additive manufacturing, in contrast, has far fewer constraints. Designs can be made with undercuts. They can be made with voids in their center. They can be made with latticed geometry. Why? Because the material is added or joined layer by layer. This approach means that, with supporting structures that are removed after completion, there are far fewer constraints in the production process.
The Implications of Additive Manufacturing
Fewer constraints, naturally, means there are less roadblocks for engineers. They can design all these new geometries that can support innovative new ways to fulfill requirements. Their hands are untied.
On its own, additive manufacturing stands to deliver sweeping changes to how engineers design, making their lives easier than before. However, there’s more in store for the transformation of design.
The Profound Automation of Generative Design
What is Generative Design?
Generative design is the capability of some computer aided design software applications to automatically and autonomously produce a number of alternative designs once given a set of engineering constraints. There’s a lot in that definition, so let’s dig a little deeper.
The use of the terms automatically and autonomously here are no accident. Once you define some specifications such as loads, constraints and materials, the software produces new designs by itself. It sounds a bit like artificial intelligence (AI), and frankly, it’s starting to approach it. But the idea is that an engineer provides the inputs and walks away. When they return, the software has a number of design alternatives for them to review.
Why is Generative Design Different?
Answering this question needs a little context. Traditional modeling capabilities in CAD software are exceedingly familiar to the steps used in subtractive manufacturing. You can extend a cross section to cut material away. You can round edges. You can add holes. These geometric operations inherently mirror traditional production procedures.
Generative design, however, differs in this regard dramatically. In fact, there are no overt geometry operations. Instead, these modeling capabilities have been developed to mimic growth patterns from nature. For example, some copy the processes used to grow bones or other cell structures in the body. Others imitate the way bacteria colonies grow multiple paths to food sources. Yet others copy how trees build their structure over time. The results are organic shapes that look far more like nature than anything produced in a factory.
What are the Advantages of Generative Design?
There are a few different ways that generative design is advantageous over traditional modeling approaches.
From a time perspective, generative design offers a significant benefit. Engineers don’t have to manually develop new designs. This technology produces the design alternatives automatically and autonomously for the engineer. This allows engineers to walk away from the software to focus on other tasks. In this way, engineers can recoup their time and even multi-task. In some ways, every engineer has the possibility to be a manager over a group of software agents, all leveraging generative design capabilities to complete various designs.
There are, however, significant advantages from a design perspective as well. The algorithms that mimic natural processes tend to produce more optimized designs, yielding higher strength with lower weights. Today, engineers are facing more difficult requirements for the products they design. Generative design technologies can help fulfill them.
Combining the Technologies
Each of these technologies independently provide advantages. Yet, when they are combined, engineers truly see significant benefits. Additive manufacturing offers the largest advantage when it is used to produce lighter yet stronger components. Generative design can deliver those designs. Furthermore, generative design produces organic shapes that are extremely difficult to produce using subtractive manufacturing. However, additive manufacturing can produce those parts with relative ease.
In the end, the combination of these two technologies hold the potential to transform engineering. Engineers are freed from the constraints of subtractive manufacturing with additive manufacturing. They are liberated to do more with less when they oversee a number of software applications, each applying generative design techniques to automatically and autonomously produce innovative designs.
Over the years, many technologies have claimed to transform design. This time, however, they might be right.
Get ready for a seismic shift in mechanical design.