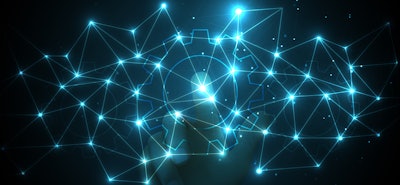
In the world of supply chain depot management, the integration of automation and artificial intelligence (AI) has heralded a new era of efficiency. From streamlined operations to enhanced safety measures, automation is optimizing depot processes and generating faster, more consistent output. Aside from businesses and consumers benefitting from this technology, who else benefits? The answer is employees throughout the supply chain, including workers at warehouses, fulfillment centers and other supply chain depots.
The evolution of the workforce is nothing new, and professionals throughout modern history have needed constantly to evolve with new technology. For example, the advent of refrigeration has made ice delivery a largely obsolete profession, and since digital movie projection became the norm, most major theater chains no longer employ film projectionists. In a similar vein, many workers throughout the supply chain have expressed concerns that automation and artificial intelligence may threaten their livelihoods. In my experience, however, advances in automation contribute to a culture in which workers are happier and safer — and have considerable opportunities to enhance their own professional development.
From a business perspective, the productivity benefits are undeniable. Automated systems can sort pallets more than four times faster than human operators, aided by sophisticated AI-driven cameras that snap hundreds of pictures every second, instantly identifying pallets in need of cleaning, repair or recycling. And a larger, more steady supply of pallets is good for consumers, because it keeps the supply chain moving as robustly and efficiently as possible.
But furthermore, workers are seeing the benefits, for the following business-critical reasons:
1. Fewer injuries. According to the National Safety Council, warehousing and transportation is second only to the construction industry in the number of preventable fatal injuries in an average year. When moving pallets, products and other assets throughout the supply chain, the potential for injuries is a constant concern. But studies of OSHA data have shown that the introduction of robotic systems can not only reduce accidents, but also preventable problems such as repetitive stress injuries.
2. More room for professional growth. Many workers that once considered themselves manual laborers are now skilled technicians. Instead of touching the pallets themselves, they are now taking accountability for the AI-enabled systems that move the pallets — troubleshooting, making repairs, switching out parts and performing cleaning and preventative maintenance tasks.
3. More satisfied workers. In a more automated environment, workers feel an increased sense of overall well-being. They know that they are safer and are less likely to experience both the boredom and the potential injuries that arise from doing repetitive manual tasks. The environment is cleaner and more organized, with less waste generated. And employees feel a sense of excitement about working with the latest, cutting-edge technology that is pushing the industry forward. The employees who are motivated about moving upward within the company are the same ones who step up and volunteer to learn about the new technology and safety procedures.
As advancements in automation and artificial intelligence continue to proliferate throughout the industry, their adoption at an increasing number of depots and other supply chain centers is inevitable. It’s true that some facilities will require fewer workers overall and supply chain professionals will need to adapt with the changing times. Those who participate in this evolution will be more contented in their jobs — and less likely to encounter a preventable accident in the workplace.