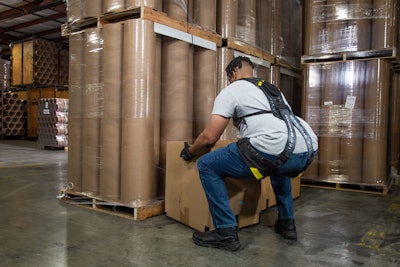
Wearing an exoskeleton used to just be a bucket list item. Now, supply chain executives are finding exoskeletons on the agenda in the present. Exoskeletons (also called exosuits, or exos, for short) are among the rapidly emerging technologies poised to impact worker safety, productivity, and retention.
The rise of exo technology coincides with a perfect storm in supply chain and logistics: an aging workforce, increasing labor costs, worker shortage, and higher demands on the remaining workforce.
High labor costs are partially due to work-related injuries, which take a toll on employees and employers. Back pain is the leading cause of disability globally. And overexertion at work is one of the leading causes of back pain and other musculoskeletal disorders (MSDs), costing U.S. businesses $12.8B annually.
Interestingly, higher worker demands are partially due to advances in automation. Supply chain automation was hoped to improve worker safety, which it can in terms of traumatic injuries. However, a recent Amazon report revealed that warehouse automation actually increased worker MSDs by 77% due to higher throughput and pace of work.
Companies must determine how to leverage multiple emerging technologies to do more with less, while keeping their workforce safe, healthy, and happy.
Exos may be part of the solution. Exos are wearable assist devices that reduce strain on targeted parts of the body (e.g., back, shoulders, hands) and make physically demanding jobs safer and less tiring. But they do not look like the bulky exos you may have seen in the movies—many real-life exos do not even contain motors or rigid frames.
In the last few years, modern exos have started to break through and be adopted due to lighter, softer, more practical and comfortable designs, along with increasing industry data on their safety, operational, and financial impacts. As a supply chain leader, here are three things you should know:
Reduce Costs Due to Work-Related Musculoskeletal Injuries
Occupational exos may seem new, but they have been studied in academic labs for over 15 years and in industry for at least seven. In the past three years, more exos have been successfully implemented allowing for a heightened understanding of their short-term and long-term impacts on worker well-being and MSD risks.
For instance, following the multi-year use of shoulder exos, Toyota and Boeing found injuries and associated workers’ compensation costs had dropped to zero in several roles. Ford Motor Company’s 18-month study found exo-user medical visits were 52% lower than the non-exo wearing control group. Similarly, a university study led by Vanderbilt and Auburn evaluated back exos by adapting an established ergonomic assessment tool and concluded that exos may reduce low back disorder risk by 20-60% for material handling jobs. Insurance company SAIF also found exos reduced worker back discomfort by 73%, while reducing lifting and overall work effort by 29-32%.
Thus, for companies aiming to reduce MSDs or struggling with high injury costs, exos provide a promising opportunity to enhance worker safety and well-being.
Exos Can Provide ROI from Improved Productivity and Retention
One reason exos have begun piquing the interest of supply chain executives is because of recent findings that exos may also increase endurance, cognitive performance, or productivity—as a result of workers being less tired and sore.
A Vanderbilt University study found that exos increased lifting endurance by 28-75%, while simultaneously reducing low back disorder risk. A Clemson University study found back exos improved lifting capacity by 6-7%, reduced peak back muscle activity by 9-13%, and made participants feel safer. An Iowa State University study found exos reduced back muscle fatigue, improved how people process information, reduced mental workload, and increased task accuracy (meaning exo-wearers made fewer mistakes).
These performance effects can have measurable impacts in the workplace, from safety to quality to productivity. While there is still limited ROI data in the public domain, supply chain companies, including DHL, XPO, DB Schenker, and Kenco, have openly discussed exo use and their evaluation of financial and operational impacts.
Recently, one multinational grocery chain used surveys and operational data to evaluate warehouse worker well-being, productivity, and ROI impacts of exos. Warehouse case pickers wearing exos reported 39% less fatigue and 31% less back discomfort. Furthermore, exos increased worker productivity by an average of 8% (measured by cases picked per hour). Based on the exo and implementation costs, and average warehouse worker wages, this productivity improvement was projected to pay back the device and implementation costs in less than 5 months and for this exo solution to have an ROI of 13X over 5 years.
Additional cost savings may also be seen from reduced medical costs and lost workdays due to lower injury risk, as well as improved employee retention and recruiting, further increasing the potential ROI from exos. Worker shortages are already creating difficulties in the supply chain, with 57% of supply chain executives reporting that hiring and retaining qualified workers is their greatest challenge. Many workers have shared that they feel employers who provide exos are showing they care about workers. These perceptions, coupled with exos making physical work less exhausting, could lead to improved recruitment and retention and alleviate some labor shortage challenges.
Projecting the Business Impact has Become Easier
There are now ROI calculators (exo-specific and generic) available that enable companies to estimate exo impacts based on their operational data, injury rates and workers’ compensation costs to weigh the costs vs. benefits. Just be sure that any calculator you use includes both the technology and implementation costs. Sometimes people get fixated on the technology (exo product) but overlook the need for thoughtful implementation (exo fitting, training, storage, cleaning, maintenance and oversight) and change management. These cost time and money but are crucial to ensure worker comfort, buy-in, sustained use and maximum benefits.
There are a few common ways for exos to achieve positive ROI. If your company’s injury rate is high and the exo solution is not too expensive, then the ergonomic risk reduction benefits alone may provide a reasonable payback period. Alternatively, if injury costs are lower, your company may see ROI primarily driven by improved productivity or retention.
But there are also numerous ways to fail, from poor implementation to deploying an exo whose cost outweighs its benefits for a given job. Working with implementation experts to identify good exos and use cases—that complement your existing ergonomic programs and controls—and properly fit and train workers can help you evaluate if and how exos can serve your business.
Surprisingly, exos do not necessarily require a large upfront capital expenditure. While a few robotic exos cost between $10,000 to $30,000, most exos in the workplace today use passive (elastic) mechanisms and are much lower cost, even as low as about $1,000 per worker (plus implementation costs). Some manufacturers even offer exo-as-a-service (lease) models to reduce upfront costs.
In summary, exos are now beginning to make a tangible impact on the supply chain and should be on the radar of safety and business leaders alike. It is becoming clear that exos—when well-implemented—have the potential to significantly enhance worker well-being, reduce injury costs, boost operational performance, provide an ROI and offer a competitive advantage in a tight labor market.