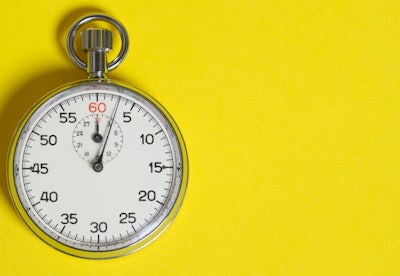
Supply chain teams at global companies have never been complacent about the robustness of their supply chains. Scenario planning for anticipated events and mechanisms built on historical learning that are activated to minimize disruptions even during unforeseen events have long been best practices. Due to this, examples abound of multinational firms that maintained service levels after a few initial hiccups during the pandemic or bounced back to BAU in record time after a natural disaster.
However, what were earlier rare and exceptional occurrences have become the norm. Before the pandemic, the McKinsey Global Institute found that, on average, companies experience a disruption of one to two months in duration every 3.7 years. While companies have been proactive in improving their responses since, the disruptions themselves are clearly on the rise. Climate change, political upheaval, international trade rivalries and conflicts define the current global landscape of polycrisis and the financial impact on businesses is significant.
In the consumer goods sector, for instance, McKinsey found that the financial fallout of these disruptions over a decade can equal 30% of one year’s EBITDA. And it is not companies alone. A single, sudden policy shift can create supply chain pressures that affect an entire country or region given the complex web of interdependencies.
Furthermore, ramping up the already considerable pressure on vulnerable supply chains has heightened consumer expectations created by e-commerce. Irrespective of the sector, the only answer for global supply chain teams to ensure their companies thrive in this challenging environment is to double down on their rapid response capabilities. The tools and mechanisms that exist have to be vastly improved and made highly accessible and flexible so frontline teams can use them on the go, to rebound faster from disruptions, maintain service levels and fulfill sky-high customer expectations.
A Consolidated Approach Unifying Data, Analytics and Teams
How can supply chain teams achieve this? The first step is to eliminate silos. As mentioned earlier, there are already a number of mechanisms in place to hone emergency response continuously and minimize disruption when it happens. The task now is to yoke these numerous tools into a consolidated and ongoing effort for rapid emergency response. It has to integrate and tap into the company’s historical and current internal data, such as past disruption responses and outstanding orders in an impacted area, and external data, such as weather forecasts, transportation providers’ updates and relevant news coverage. Next, it has to apply the gamut of analytical techniques from basic descriptive measures to advanced predictive and prescriptive methodologies, such as machine learning, to facilitate both prompt and adequate response in the face of disruption and continuous refinement of these tactics.
For instance, if a hurricane is predicted to hit a specific area, the dynamic response planner can analyze similar past events and live external data to anticipate disruptions, such as road closures or warehouse damage. Frontline employees, who earlier had to toggle between information sources and collaborate across teams to gauge the impact, will have a comprehensive, granular analysis at their fingertips and can focus on expediting preemptive measures, such as rerouting shipments, increasing labor capacity or stockpiling inventory at unaffected locations. The learning from the successful mitigation exercise will be quickly and comprehensively captured in a single place, preparing the company to face a similar emergency that follows soon in another location.
In retail, this can mean ensuring that stores in the affected area have sufficient stock of essential goods to meet customer demand before the storm hits, which can mean paying transporters more and ensuring faster compliance for intra-state or country border clearances. Since teams are on a single platform leveraging consolidated information and advanced techniques, they can act faster on all these fronts.
Training, Adoption and User Friendliness Drive Supply Chain Agility
For a company to genuinely acquire resilience in the face of polycrisis, it has to ensure the adoption of its unified and advanced response approach among frontline teams, such as operations and logistics. They should be highly familiarized with using the consolidated rapid response planner. Consistent education and training must tackle any hesitation to work with cutting-edge, evolving algorithms for inventory management, risk identification, demand sensing, cost analysis and so on. Supply chain and analytics leaders can build the trust of their frontline teams in the comprehensive dynamic response planner by regularly seeking feedback for improvement and demonstrating how the planner can deliver better responses for exceptional events that occurred or future what-if scenarios compared to the existing scattered mechanisms.
Crucially, the consolidated planner should be friendly to use and understand and accept user inputs easily to generate probable outcomes on the fly, so a frontline employee is not hampered from leveraging their own learnings and live observations while responding agilely on the field. For example, due to conflict in a region, a company may be well into the process of onboarding new suppliers and transport partners in another geography. While the formal process may not be complete, a frontline employee who is tackling a crisis elsewhere and aware of the new partnerships should have the agency to add these to their scenario planning to determine the best possible response to minimize disruption.
A Window of Opportunity
Multinationals and their supply chain teams should see the current daunting landscape as an opportunity to build true resilience. The way to do this is to invest in a comprehensive dynamic response approach that will bring everyone on the same page in terms of how they understand and view the multiple factors influencing crisis response, ensuring no piece of data or information is lost as it flows across regions, functional teams and individual decision-makers on the field. Familiarizing teams with advanced techniques and empowering them to incorporate their learning and experience into the algorithms will also significantly enhance the accuracy of the rapid response to disruptions.
A unified dynamic response planner addresses two of the top four factors EY identified in 2023 that modern supply chain leaders are seeking to address: end-to-end visibility and improved resilience. Falling behind on rapid response will not only hit the bottom line but also create reputational loss, as consumers expect more, faster.