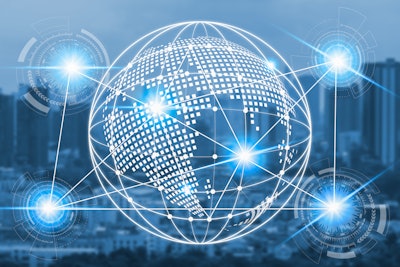
The events of the last few years might have elevated the term “supply chain” to the public zeitgeist but, for businesses, logistics disruptions have always been a fact of life.
Disruptions come in all shapes and sizes. Small logistics network disruptions, like shipment delays of raw materials, parts, or finished goods due to weather conditions or minor equipment breakdowns in manufacturing or distribution centers can lead to temporary inventory shortages, increased transportation costs, and delays in fulfillment. Large-scale disruptions, such as the closure of the Port of Baltimore due to the collapse of the Key Bridge in March 2024 or the low water levels in the Panama Canal that have persisted since 2018, have much more widespread effects. Without proper planning in place, the resulting backlogs, production disruptions and product shortages can have far-reaching consequences including lost sales, damaged client and customer relationships and financial losses for companies up and down the supply chain.
It is crucial for businesses to have contingency plans in place to mitigate the impact of logistics network disruptions. And, in the wake of the pandemic, a lot of businesses seemed intent on doing just that. But as the pain of the COVID supply chain crisis has diminished, so too has the urgency to prepare for what comes next. After spending so much on offshoring, “near-shoring” is a costly and time-consuming endeavor. And, although some businesses have taken a serious and deliberate approach to change, most have gone back to the practice of managing to current period financials.
Change is painful, and many are unwilling to take drastic steps toward mitigating future disruptions if it means missing a reporting milestone. Nevertheless, there are some practical steps all businesses can take to mitigate and manage network disruptions. Many of these come down to using the tools we have available to anticipate and plan for certain disruptions and having choices available to help avoid their worst effects.
1. Consider Your Geographic Footprint
This goes for both your inventory and your people. One of the most common causes of logistics disruptions is weather. For example, Hurricane Beryl, which hit the gulf coast of Texas in early July 2024, impacted everything from maritime shipping, air cargo and rail to trucking and last mile delivery. And, even if there was a way to get shipments in or out, in some cases there was no one to load and unload trucks because people couldn’t get to and from work. For a business with all their inventory housed in the affected area and no Plan B, this was a logistics disaster.
Just because your business operates in a region where major weather events are possible or even commonplace, does not necessarily mean your Plan B has to be as drastic as having multiple warehouses and distribution centers spread throughout the country. Although it wasn’t the case a few decades ago, we can now forecast major weather events with a fair degree of accuracy several days out. That means you can get ahead of anticipated disruptions by loading trucks with enough inventory to cover a few days or a week’s worth of orders and sending them to safe locations to bridge the gap while you weather the storm.
2. Adjust Your Just-in-Time Approach
Be wary of adherence to just-in-time (JIT) inventory management that cuts excess but places production lines and other downstream processes in peril. JIT inventory management leaves little room for error or unexpected disruptions. Any logistics hiccups can quickly lead to production halts, stockouts and complete shutdowns.
Nobody wants to go back to the way we did things before JIT but, in some cases, we’ve leaned too far into it. Inventory is a buffer. Maintaining safety stock levels for critical items and diversifying suppliers to reduce dependency on a single source are ways to avoid being pinched in the event of a disruption. Businesses should also conduct regular risk assessments to identify potential vulnerabilities and develop contingency plans to ensure operational continuity.
3. Don’t Rely Exclusively on Industry-Dependent Carriers
Limit your exposure to carriers who are too dependent on a single customer or industry sector for business and revenue. When the industry or sector experiences a downturn or disruption, it can have a cascading effect on the carrier’s operations. A downturn in a given segment can mean reduced shipping volumes and that the carrier’s trucks aren’t around when you need them.
Build out your roster of carriers so you can pivot when necessary. Diversifying your carrier relationships across multiple industries and sectors—not to mention multiple geographies—gives you greater redundancy and flexibility to sustain smooth operations during a disruption. Working with a 3PL that has depth and reach in their vetted carrier base can help you broaden your capacity and capture capability across shipping modes, particularly for small or medium-sized shippers or those who might not have a lot of density in a certain mode.
4. Don’t Become Mode-Dependent
Often, disruption hits different modes in different ways and to different extents. When one mode gets strained by a disruption, the effects might take time to reach other modes. This creates short-term opportunities for relief.
That said, it’s important to understand the costs and transit time impacts from mode to mode. Modes generally have different speeds of movement, and you must understand what that means for your customers in terms of lead times and promised dates. Moving from one mode to another might mean a hit to your short-term margins, but strategically switching modes can help mitigate the impact of a disruption and get the job done.
5. Don’t Wait for a Crisis to Try New Methods and New Providers
Trying new methods and new providers in the midst of a disruption is pretty much always a bad idea.
Establish your roster of carriers and interact with them in standardized methods. Assess that network of carriers and look for potential flaws in your logistics network. If you find a potential weakness, experiment with solutions when things are running smoothly. For example, if you decide the answer to a potential geographic disruption is to establish a forward stocking location 500 miles away, send a truck one day during normal operations and evaluate the results. Necessity might be the mother of invention, but a crisis is not the right time to try something new, unless there’s no other choice.
Being prepared for logistics network disruptions doesn’t have to mean spending vast amounts of money rethinking your entire logistics network. In today’s world of technology and communication, there are fewer true surprises than ever before. The advanced notice might only be measured in hours, days or weeks, but that is not nothing. Even the pandemic had warning signs months ahead of time that, had we heeded them, might have softened the blow to our logistics networks.
It all comes down to optionality—see to it that you have choices available to you, so that when you see the signs of impending crisis, you can leverage it to help you ameliorate the worst of the effects and continue to function. Make a plan and stick to it.