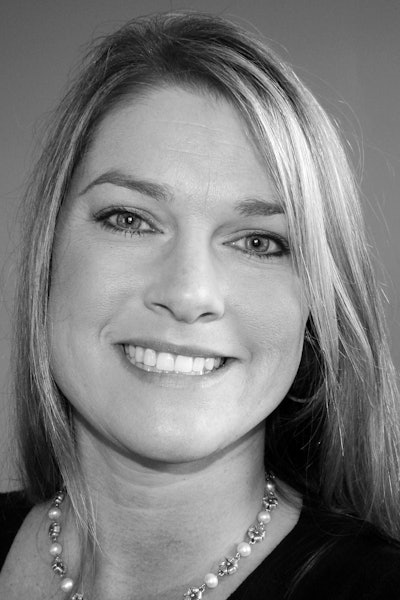
Cost management is still a priority in 2015 in automotive sector companies. Beside the fluctuating economic outlook, this also concerns advances in integrated indicator systems (balanced scorecards) and cost control, which allow for total costs to be captured. The underlying assumptions, however, often prove incorrect for business operations. The functionality of turbo transparency for connecting strategic and operational planning provides a remedy.
Automobile manufacturers base their value chain decisions on parameters such as supplier location, material flow planning and warehousing, also called total landed costs. The key performance indicators (KPIs) for logistics derive from these factors: inventory, cost, space and staff.
Many carmakers create an overall cost perspective based on total landed costs that provides comprehensive information on the outcome of entrepreneurial activities. Not only is the purchase price (A price) relevant, but manufacturers also consider a B price with logistics elements, as well as a C price with risk costs that may occur. This model could illustrate how a delivery location in China could ruin the originally much lower A price due to higher B and C costs.
Through this holistic approach to costs, companies are making great progress in the strategic decision phase. With an overall view of the entire delivery, warehousing and manufacturing process, investment decisions are made on a more accurate basis. They can, for example, more easily and reliably decide which storage facilities or factory floors to develop, and which suppliers they want to select for which sites.
Though this is an intelligent approach to cost management, everything falls apart if you cannot readjust continuously in the daily value stream. Fluctuating market demands and long supply chains prove to be susceptible to glitches and different views, and information at different times cause many assumptions to be unsustainable. Contrary to the original plan, a market may develop unexpectedly. Or other concepts could prevail in production, at least temporarily, which cause higher logistics costs. One does not adhere to assumptions made at the beginning planning phase without considering the need to revise according to changing market conditions.
Supply chain decisions at the strategic level may prove to be unsustainable at the operational level.
Silo Mentality and Lack of Integration
As a result, strategic targets (supplier selection, storage facilities) in operational business (market changes, strike, insufficient storage facilities) can boomerang.
Within the logistics organization, it turns out that the organization may still be vertically operating in silos: order dispatchers’, material dispatchers’ and transport dispatchers’ work may be function-oriented, but not integrated. Information systems operate separately and overnight processes can result in delayed information status, which increase daily changes in the control process.
For these reasons, logistics is lacking the essential real-time visibility across divisions; there is no informational and organizational medium that can successfully intervene in the control process. As a result, the overall cost view is overlooked in the individual silo decisions.
What Was Planned Up Front Must Be Readjusted Daily in Operations
Many strategic assumptions are static and don’t consider foreseeable changes. At the same time, many of the strategic assumptions interact in operations dynamically and often provide a surprising result. Subsequently, competition begins in the in-house control process about which department can best optimize in their area and can put their own indicators into perspective. The unconnected optimization of one silo (usually) has a negative impact on other silos, which then have to again be readjusted.
Slowly, but inevitably, supply chain management begins to rethink. The realization takes hold that the processes that influence each other in daily operations need to be much more interconnected. Order planning and processing, as well as physical material and production logistics in supply chain management are much less connected than required. More integration, especially in the operational processes, is urgently required. Only in this way can meaningful and direct adjustments be made.
The comprehensive integration (end-to-end) of the horizontal organization (order management, production control, scheduling, transportation planning) is moving into focus as a result. At present, tactical transportation planning is usually not connected efficiently with material planning and the material demand process. In order slotting, it is often not resolved how real vehicle orders from customers (build to order) may be guaranteed on time, even though material was already ordered from long supply chains long before scheduling.
Commit to What You Can Deliver
Capable to promise (CTP) means promise only what you can deliver. Incoming orders should be scheduled following this motto when the capacity and availability of materials is a given. There they should remain! Only then can demand fluctuations towards suppliers be avoided and greater stability achieved.
Due to the mentioned short-term changes (quantity and order configuration), the normal control process still requires daily readjustments.
Turbo transparency produces relief. This method takes all available information and creates planning silos in real time, linking organizational decision-making processes through a total cost analysis. Because the information is collected in real time, a source of truth is created and brings together knowledge from the silos.
What does turbo transparency mean from an information technology point of view? It combines information about orders and material, which are very complex—such as in the automotive industry—and connects the demand situation with the inventory situation and the transport situation. It also integrates the aforementioned levels over the entire value horizon (time flow: view per time slice and cumulative view across time slices).
Turbo transparency reveals interrelated knowledge about change dependency. For example, if a truck is late, it identifies and takes into consideration which inventories and orders are affected; which order changes; and which materials, inventories and transports are affected. It can provide simulation knowledge focused on the future in order to migrate from a reactive to a proactive role in the control process; it can validate scenarios to test the effectiveness of special measures like the impact of extra shipments.
Only through turbo transparency as part of the CTP principle are automakers and original equipment manufacturers (OEMs) able to intelligently connect material and order planning with material control. They can quickly provide recalculations and a very high degree of process transparency, contrary to the still widely used method of testing in nightly batch operation. The bottlenecks identified in this way are not visible until the following day. In a real-time turbo transparency process, critical components are being constantly monitored. Since this method also quickly explodes the variance of the components or the supply chain commodities (a very high complexity and diversity of data is produced), a classification into A, B and C parts is often made.
If a currently planned production suddenly demands changed requirements, turbo transparency can then offer a way to readjust their impact, even during the day. One can now decide whether to perform this change or opt to leave production as is (with fewer follow-up costs). Last-minute changes are scrutinized and omitted much more with this approach than before—not least because the decisions’ impact on other parts and processes will be transparent.
Order scheduling in assembly plants is strongly associated with material dispatchers, which call off material for plants. If there are any changes in the order mix, the dispatcher recognizes material that must be ordered on short notice. With turbo transparency, the dispatcher and the order scheduler have the same decision-making information. They may decide whether a particular adjustment or even another scenario makes the most sense.
Spontaneous actions in order to maintain supply guarantee can reduce the bullwhip effect.
Controlled intervention is possible for customers thanks to turbo transparency. The analysis, calculations and simulation capabilities, delivered in real-time, enable them to recognize the consequences of potential interventions. On this basis, customers adjust and intervene only if it makes sense with regard to the overall cost.
Lean Principles All the Way to the Supplier
There is greater stability in operations if the functionality to visualize transparency in real time, the turbo transparency, is implemented and only meaningful change decisions are made. Warehouse space, inventory and special transports can be better regulated. This stability can be used to further transcend the classic lean management principles to reach beyond the company and into the supply chain.
Company logistics can realize goals that were previously beyond reach. With little locally maintained stock, it controls material and orders material for plants close to actual need. Ultimately material, planned by demand, can be brought into the plant on the basis of reliable order planning. Ideally, an in-sequence process follows. The lean method can be used despite the complexity in the automotive industry. Experiences with the use of the solution show that large savings are possible.
Technological Prerequisites for Turbo Transparency
This approach is not feasible in enterprise resource planning (ERP) systems with conventional relational databases. Simple reporting and data mining are not adequate. A change in thinking and a new technology that is based on two basic pillars is necessary:
- A data model that maps automotive value chain processes, similar to the structure in ERP systems.
- Relations of different sources that must be linked transactionally.
The model of choice for this is in-memory technology. It quickly calculates changes and their impact in real time several times a day.
Stable planning means fewer readjustments!
Shay Sidner is the director of operations for flexis North America, a company that focuses on sales and operations planning, as well as advanced planning and scheduling. Sidner has more than 10 years of experience with supply chain optimization in manufacturing industries. For more information, contact Sidner at [email protected].