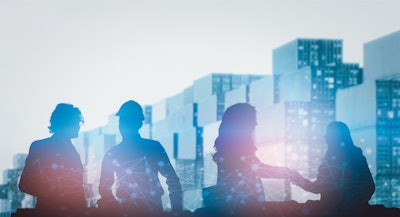
Nearly two years after the COVID crisis shut down economies and sent global supply chains into a frenzy, another glaring risk to global supply chains emerged: geopolitical insecurity gained the spotlight when Russia invaded Ukraine.
Geopolitical interruption is not a new risk to supply chains. Starting around the 1990s, U.S.-led globalization ushered in a new era of commerce. Our political, economic and social goals were furthered by fragmenting supply chains across vast distances, capitalizing on access to raw materials, energy and inexpensive labor. Most developed economies followed suit, establishing new industrial booms across eastern Europe, South Asia and the Indo-Pacific regions. This, of course, presents tremendous opportunity but also risk.
Today’s hyper-globalization of supply chains coupled with unprecedented volatility has highlighted a new critical area for scrutiny by strategic business leaders: how to use scenario planning to build supply chain resilience.
The impacts of the Russia-Ukraine War on supply chains are far-reaching and will continue to be felt longer than we can speculate. Initially, though, we have seen two major results:
- First, one of the shocks to the global supply chain was the immediate loss of access to agricultural commodities and its effect on commodity markets. Ukraine is one of the world’s six “breadbaskets,” or primary regions where our food is produced. Ukraine produced a significant market share of wheat (10%), barley (13%), corn (15%) and sunflower oil (50%) before the war. The impact of the loss of those crops sent commodities prices skyrocketing which impacted the production and availability of food globally and is continuing to contribute to inflation of food prices at a retail level. Ukraine was also a leading producer of potash, a key ingredient in fertilizer, further destabilizing global agriculture prices and output.
- Second, global enterprises are facing an existential question of whether globalization is the right decision for their critical supply needs. As we moved production beyond our shores, governments and economies became more interdependent. One assumption that was relatively safe until recently was that political and economic stability would continue. In reality, most geopolitical conflict was held to localized scope and geopolitical risk was largely driven by vendor opacity and the risk of finding forced labor being used unknowingly. That assumption of relative peace and stability is no longer a given in some, if not most, regions of the world.
There has also been a flurry of activity reconsidering supply and production networks. Much of this activity is deliberate, driven by corporate governance and risk analysis in light of events in Europe and East Asia. Last year, more than 1,000 companies curtailed operations in Russia. To avoid the extreme cost and impact of such unplanned exits, boards must include geopolitics in their risk analysis; reshoring, nearshoring and now friendshoring, a growing trade practice where supply chain networks are focused on countries regarded as political and economic allies, are prevalent in corporate lexicon.
Reshoring has grown in popularity recently where economically feasible. However, building and staffing new capital investments in the United States isn’t always possible. Federal and state policies often incentivize certain industries to do so, as evidenced recently by work such as the CHIPS Act. Nearshoring moves production closer to home operations, usually into countries with a lower cost of production but with a shared border. This ensures ease of monitoring operations, as well as a faster speed to market by reducing lead times. Friendshoring, on the other hand, moves production and sourcing resources from countries whose values align with our own. In friendshoring, we may lessen the risk of a sudden, abrupt shock to the system like that faced by the 1,000+ companies who found themselves quickly exiting Russia.
The growing role and responsibility of supply chain planning
Supply chain practitioners have never been in a more valuable position to play a critical role in these enterprise decisions. Fortunately, as boards look at events in Europe and Asia and consider how best to plan or act, supply chain organizations have spent the last three years already building and exercising the capability to plan flexibly and responsively to rapidly changing conditions.
Best practices and key planning considerations include:
- Network analysis: It’s important to understand the physical footprint and flow of goods from Tier 1 and 2 suppliers into manufacturing locations, through distribution hubs and into your internal network. This may have been conducted as part of a previous risk analysis, in conjunction with a supply chain planning resiliency project or, for some, as part of an ESG assessment. Many reputable supply chain consulting firms offer network studies, and they can be completed relatively inexpensively as a baseline.
- Advanced scenario planning: Once the baseline network is known, capacity, cost, throughput, lead time and other metrics may be included to develop a digital twin of the physical supply chain. This forms the basis for advanced scenario planning, a critical capability for modern supply chains. Major analyst firms and research organizations have published research on the topic, from supply chain risk response and mitigation to using scenario planning to build supply chain resilience. The most difficult part of developing such responsiveness in a supply chain is not at the strategic or academic level; rather, it’s in driving the execution of the plan through a multi-tiered organization that may contain multiple business functions, geographies and even operating companies. Here, data plays a critical role.
- Interconnecting systems and data: To enable the type of visibility across an enterprise to predict, model or suggest alternatives across such a multivariate problem, massive amounts of accurate, complete and timely data are necessary. Vendors today sell software like supply chain “control towers” which can unify multiple corporate systems, enabling the ability to monitor risks and help model responses. Many leading supply chain organizations are in the process of replacing multiple, disconnected systems with a more modern architecture that unifies data across functions and even enables rapid “what-if” scenario planning.
Supply chain digital transformations enable organizations to better predict and respond to supply chain disruptions. Whether those disruptions are geopolitical in nature or based on more mundane and frequent disruptions, having a playbook in hand that can optimally redeploy resources to reduce negative outcomes is paramount.
Risk analysis of geopolitical considerations can be done without expensive digital transformations, as can procurement analysis to prohibit over-reliance on a single supplier in a riskier region. And while geopolitical risk is not a new phenomenon, it’s impact on a faster, more interconnected world of supply chain is. To get started, corporate leaders must consider first how exposed they are and second how quickly they can respond in a worst-case scenario. Working with a consultancy experienced in multinational supply chain planning can also provide an immediate augment of internal capability and experience.