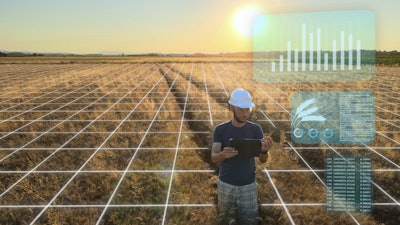
From enhancing visibility, building resiliency and mitigating risk to leveraging smart technologies and automated software, a digital supply chain means different things to different companies.
Yet, digitization itself presents the same benefits across the board in moving temperature-controlled foods in a safe and efficient manner.
Marina Mayer, Editor-in-Chief of Food Logistics and Supply & Demand Chain Executive, talks exclusively with James Newman, head of product and portfolio marketing at Augury, advises supply chain leaders to discover the largest blockers in the business and begin the digitalization process there.
CLICK HERE to read the article in full.
Food Logistics: What is a digital supply chain? What does it mean for you/the cold food chain?
James Newman: Digital supply chains are very complex. They’re designed to offer a complete view of everything that needs to happen to create food - from raw material traceability and management (including land usage, animal usage, etc.) to packaged goods production facilities to B2C traceability of consumption, inventory and stocking management. Organizations must consider all these factors to get every piece of a (sometimes) international supply chain right and enable traceability and sustainability tracking - all while ensuring that logistics, demand planning and forecasting, etc. are integrated, interconnected and driving toward common goals.
For the cold food chain in particular, this becomes even more interesting when we consider things like energy costs for refrigeration, transportation costs (including refrigeration) and production costs for creating and storing refrigerated foods.
Food Logistics: Describe some technologies and solutions defining the future of digital supply chains.
Newman: There are a host of technologies and solutions that are revolutionizing digital supply chains. For example, exotic technologies like wearable tech for cows that control methane emissions in the agricultural space, drone mapping for land usage, AI-driven solutions for processing facilities and QR- or NFC-enabled technologies that track finished foods between the processing facility and the retail store (and everywhere between).
If we take a deep dive into just one area, the space inside the processing plant walls, there are a number of places technology can bring breakthrough benefits. AI-driven machine health platforms enable maintenance and reliability teams to better manage the uptime of the assets, which turn raw materials into finished food products, while reducing waste due to unplanned downtime and lowering energy consumption through optimized asset performance. The ability to leverage AI-driven process health solutions optimizes production lines to maximize quality and throughput while reducing energy and waste. Both technologies directly drive bottom line results, which contributes to success up and down the larger supply chain. Machine health and process health can reduce raw material waste and energy costs and increase production capacity and quality, which leads to more products available on the shelves at retail stores.
Lastly, by leveraging connected worker solutions, which bring maintenance, production planning, and operations teams together into a more tightly integrated production team, technology solutions can empower new decision making models and recruit new talent. They can become an integral part of how teams work; one example would include making maintenance work order creation dynamically automated via machine health alerts, coupled with worker training certification, digital process management and production scheduling to understand the when, where, how and minimal disruption required to operations to complete a repair.
In reality, there are almost too many operational opportunities and technologies ready to tackle every one of them.
Food Logistics: Where to start? How do companies start the journey toward a more digital supply chain? Outline some good first steps.
Newman: It all starts with one thing: what are the largest blockers the business is facing? Often, digital projects start as “proof an idea” rather than “can we solve a problem for the business.” As a result, numerous research studies and analyst groups agree that 75-85% of all digital projects get stuck in pilot mode, and they are never able to scale across an enterprise. In many cases, that is a direct result of not being able to translate the pilot results into an achievable business outcome at scale.
If the issue is to solve raw material availability due to waste, look at where that is happening in the supply chain, what you are doing today and what success looks like for the entire business if you eradicate this issue. Then, focus on a technology selection process that can address and realize the actual core business need. Many times, this means foregoing the idea of generic platforms that could potentially solve numerous challenges someday and instead focusing on purpose-built solutions that can immediately tackle the problem they were designed to solve and have already cracked the scalability issue.
Many organizations and consultants talk about starting small with digital projects, but in reality this has led to many bad practices. The best companies don’t start small. They start smart with a real focus on what the global outcomes to be realized are and then choose digital solutions that meet those requirements.
This methodology doesn’t care where in the supply chain you start, whether it’s in raw material handling, finished product loss and waste improvement, or raw materials to finished product processing. But it does require the business to take a hard look at what is really driving the need for change and be willing to tackle that problem head on, very specifically.
CLICK HERE to read the "Breaking Down the Digital Supply Chain" article in full.
Food Logistics: What sectors (i.e., agriculture, frozen foods, etc.) are more impacted/affected by digitalization than others and why?
Newman: There is almost no sector that isn’t having a digital revolution, although it’s very unequal across the supply chain. Large agricultural companies are leveraging digital solutions almost everywhere while smaller organizations may be struggling to afford digital solutions during times of uneven pricing, especially as transportation costs drive profits down for smaller producers. In the manufacturing space, digital solutions are driving significant reductions in raw material loss, improved quality and throughput and reducing the need (where capacity constraint still exists) to build new factories as existing ones are able to increase throughput through better operations. At the same time, sustainability requirements will rise over the next several years, so across the supply chain, particularly as requirements extend to Scope 3 (the entire supply chain), the need to not just “make each part” digital but to integrate across the supply chain for better traceability will be the new frontier.
A couple of examples: Farmers are often using very sophisticated digital solutions to improve crop efficiency while reducing the need for labor that is in short supply. GPS-enabled machines can have pre-configured planting or harvesting routines built in that enable autonomous machines to do work far more efficiently and at lower costs than traditional methods.
In food processing plants, the reduction of unplanned downtime has triggered savings of millions of dollars in increased capacity while improving production forecasting, triggering impacts across the supply chain for better raw materials demand forecasting and better supply chain delivery to locations that have demand.
Food Logistics: From food production to the retail and/or foodservice outlet, how does a digital supply chain transform the way food is moved from Point A to Point B? This could also entail fleet, warehousing etc.
Newman: Let’s take an example of one product and how it impacts the entire supply chain. An ice cream producer has variable demand across seasons, so their digital supply chain needs to be able to forecast demand from the consumer side to understand requirements for how much ice cream is needed and when (for simplicity, let’s use a single flavor). Demand is not just “seasonal” but regional, based on pending promotional campaigns by particular outlets, etc. Obviously, the digital supply chain must then be able to transmit this information to the manufacturing plants that will produce the finished products. However, in many cases, this isn’t a single location, it can be many. So, the digital supply chain also has to understand production efficiency and capacity at each location so that each individual site can be given the order within the context of the entire demand. Obviously, this should then cascade to raw material providers (milk, sugar, etc.) with an understanding of their capacities, costs and constraints as well. In between all of these points lie logistics, including warehousing, transportation and fleet management, dispatching and order management, etc. It’s a very complex process.
However, what happens to an intricate web if one of the plants has an unexpected shutdown or produces less optimally than required? Raw material requirements may increase, as products that don’t meet quality standards must be discarded as waste. Production quotas are impacted, meaning that logistics planning and supply chain management must be recalibrated to the lower output available. And, of course, retail outlets must be managed to adjust delivery based on available product, which means there will be less supply than demand, which could result in brand loyalty challenges.
The digital supply chain, especially with solutions like machine health and process health, can manage this from start to finish but, even more importantly, it can avoid these operational challenges entirely. Digital factories can better prevent failures, optimize production and can actually accelerate each part of the chain. As production improves, each part of the chain is optimized based on true capacity, without disruption.
Food Logistics: Describe some other trends and challenges with regards to digital supply chains.
Newman: There is an increasing need to connect each part of the supply chain together. Often, parts of the supply chain (scheduling, production planning, delivery and logistics, fleet management) have digital solutions within a single set of walls but a true digital supply chain must connect each of those components together, while also extending to include systems outside of the company, including suppliers and end retailers. This is not the same as the “vertical” supply chain of the past, although it has elements, of course. Instead, this is the idea that digital solutions are not just “managing the top” of the supply chain but are integrated into each operations layer to ensure that problems are recognized and treated or adjusted long before a disruption occurs. This means going deeper than just logistics or inventory management, but instead getting to the root of “if this happens here, this is what we do about it, where we go next, and how we react” at a very granular level, at each stage of the supply chain. This means that more people have to be involved in creating and understanding the entirety of the supply chain. Manufacturing, operations, logistics, supplier management, fleet management, farmers and agricultural suppliers, retailers and every other stakeholder must be an integral part of the connected process to ensure that each step is not just “known” but digitally connected.
Food Logistics: What are some things not addressed above that may be pertinent to our readers?
Newman: One could look at this topic and think “it’s impossible.” And to some extent, holistically, that’s true. There is no such thing as a “complete” supply chain solution. However, it’s important to remember what we said about where to start: understanding the biggest challenges and tackling them first and directly. There are solutions that can help do that, but it requires the managerial courage to not do what’s easy or simple but to achieve what has real value. Digital solutions providers with purpose-built solutions, including AI-enabled solutions, solve challenges and help realize real value, but they aren’t enough. Digital and business transformation require real cultural transformation, and that will create a supply chain that drives value beyond just managing logistics and suppliers.
CLICK HERE to read the article in full.