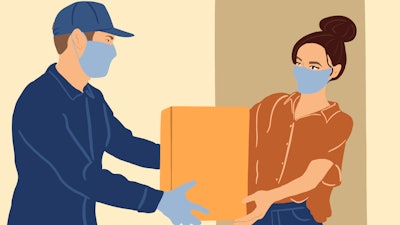
As with so many industries around the world, the Coronavirus disease (COVID-19) presented the grocery sector with a host of supply chain problems in the wake of pandemic-driven disruptions and rapidly changing consumer habits. From maintenance and temperature consistency issues to sustainability concerns, the shift to grocery delivery – both at home and curbside – shined a spotlight on the flaws of the cold chain fulfillment system and gave rise to a list of demands that needed to be met in order for it to run smoothly, even while under intense pressure.
Grocery sales are projected to only increase. According to a recent report, online grocery revenue is expected to account for 20% of total grocery sales by 2026. Updated technology that addresses these key areas of concern is needed – and quickly – as the demand for this service continues to rise.
Compressor-based systems traditionally used in transporting and delivering cold chain products take up significant truck space and are prone to maintenance and leaking problems that slow down transport and can delay schedules. Solutions like solid-state cooling technology can offer an alternative that is not only more mechanically reliable, but also more sustainable than hydrofluorocarbons (commonly used in compressors) as the technology is able to maintain consistent temperatures. This chip technology offers energy and cost-efficient ways to generate a cooling effect, putting up a promising solution to solving the last-mile delivery issue in the cold chain.
Historically, cold chain grocery delivery has been riddled with maintenance issues commonly related to the use of compressor-based systems, which refrigerate goods as they move from point to point. Leaks, which take place when the fluids used to cool the compartments of the trucks seep out, are a silent but disastrous concern that lead to failures in the cooling systems of trucks and can compromise loads. Drivers or fulfillment teams typically have no way of detecting a leak until it is too late. While consistently monitoring the temperature of the compartments can sometimes avoid these disasters, this strategy is far from perfect and doesn’t avoid lost time spent waiting for repairs and the delay of fulfillment of orders. Other leaks, such as air, also present issues, introducing unstable temperatures into the truck. This can compromise the cargo, leading to dissatisfaction from customers.
Switching to a solid-state technology system eliminates leak-prone compressors, both increasing space in the trucks and helping to reduce system upkeep. Solid-state cooling technology can also be integrated into extremely compact refrigeration solutions that are easily monitored through wireless technology, which is able to alert drivers to issues before they result in a loss.
The above issues get at the heart of the problem -- keeping the refrigerated and frozen goods at a desired temperature for food safety and freshness. This is key to complete a successful trip. Delivery of items that need multiple temperatures in one load, as well as those that use passive cooling, can create over or under temperature environments without accurate cold chain custody. Problems caused by the aforementioned leaks may not be detected by sensors until the temperature has dropped beyond return for safe delivery. If the food has not maintained a specific temperature, the best case outcome is spoilage and reduced freshness, but in many cases, the food can become unsafe for consumption. However, solid-state cooling technology meets this challenge once again by providing consistent temperatures with intelligent active sensors and control that can flag malfunctions and track cold chain custody in real time, preventing irreversible damage.
Finally, sustainability is increasingly becoming top-of-mind as many customers begin to devote loyalty and therefore dollars to companies who put forth more sustainable efforts. Refrigeration solutions are particularly susceptible to this scrutiny, as the vapor compression systems inside refrigerators release gases that produce a very high greenhouse effect. Traditional refrigerants like R134a and R404 are highly potent greenhouse gases (GHGs) and contribute to global warming, and have been called out by the United Nations as a rising concern. “Natural refrigerants” such as isobutene and acetone have lower Global Warming Potential (GwP) but come with a host of maintenance and safety issues. Solid-state cooling technology uses just CO2 and water, with a GwP of just 1. With more and more consumers asking retailers how they are making their operations more sustainable amidst this growing global warming crisis, being able to show that every area of operations is as sustainable as possible is incredibly important.
Luckily, solid-state cooling technology introduces a solution that not only decreases the amount of harmful byproduct produced by a company, but additionally can reduce the need for more supplies in the cooling process. In this way, chips can reinvent and refine the cold chain delivery system with a decreased use of refrigerants, eliminating the need for additional cooling materials (dry ice, gel packs, ice blocks, etc.). They are also cost-effective, as their small size, portability and flexibility of use makes them reusable across solutions. Solid-state cooling technology can also help eliminate the need for multi-temperature warehouses, reach-ins and tri-temperature delivery vehicles, as they can be integrated into smaller, self-contained systems that hold individual loads, including loads that require freezing. This reduces the number of resources needed for cooling and provides a solution that consumes less time, worker attention and maintenance.
The industry of cold chain delivery has always had its share of issues, including keeping the refrigeration systems maintained, ensuring consistent temperatures for a variety of chilled and frozen goods and ensuring that the solutions utilized do not introduce more harmful byproducts into the already-damaged climate. However, when replaced with solutions like solid-state cooling technology, many of these problems are reduced or even eliminated, making it an effective tool for the logistics and grocery industry to approach the last-mile challenge of cold chain grocery delivery.