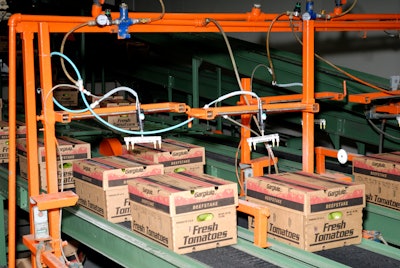
The Coronavirus disease (COVID-19) pandemic dramatically impacted all industries. The food industry is no exception. Just one year before the pandemic, hopeful projections predicted that one-fifth of U.S. households would be shopping for groceries online within five years.
In the last nine months of 2020, some online grocery retailers saw order volumes surge 500%, according to CNBC. Digitalcommerce360.com reports that in the United States, “68% of consumers ordered groceries online for home delivery between March and late August 2020.” McKinsey & Company projects that 45% of consumers intend to continue ordering online post-pandemic.
This dramatic growth of online grocery shopping combined with a short-term increase in people stocking up on food has increased pressure on the industry to keep pace with demand, minimize waste and uphold the highest quality and safety standards. Fortunately, there are tools and high-impact activities within end-of-line packaging and transport preparation that can help food suppliers and distributors meet these challenges.
The key to maintaining and ensuring food safety is through the strategic application of technology and advanced materials across complex global supply chains.
Raw and bulk ingredients
The transportation of raw and bulk ingredients is the first leg in the food supply chain journey. Whether for in-store, food processing plants or animal feed, some ingredients require special care during transporting and handling. For example, polybags, which are widely used in animal feed, tend to slip on each other when stacked. One innovative solution to avoid spillage and loss is using water-based adhesives that hold filled and stacked polybags in place during transit. These adhesives are cold applied and do not leave behind a sticky residue or cause tearing during unstacking like hot melt adhesives.
Sometimes a combination of solutions is required to achieve optimal results. For example, cold-based adhesives are widely used in conjunction with stretch film. Ultimately, many factors contribute to food safety and are largely dependent on the type of food produced, as well as the distribution channels. Consider the vast differences in packaging needs related to transportation of perishable vs. non-perishable goods. While food contamination and damage can occur at any level, optimized packaging solutions help food products arrive at their destinations the way they were intended -- safe and secure.
Consumer food products
Once the raw ingredients have traveled safely to the store shelves or food processor, things get more complicated. For instance, consider two high-volume consumer goods -- macaroni and cheese and dairy products -- and their distinct transportation safety demands driven by differing shelf-life requirements and manufacturing environments.
Handling the millions of mac and cheese boxes rolling off production lines requires the work of more automated load containment systems. Rotary ring stretch wrapping technology is a common solution in these high-throughput environments to help ensure that the product is tightly wrapped and arrives to its destination safely and uncontaminated.
Dairy must also keep up with equally high demands as millions of gallons of milk are sold daily in the United States alone. The difference is these products have much tighter timeframes in terms of processing, packaging and shipping to preserve shelf life. Speed and reliability are a top concern in this environment. Any machine downtime in the palletizing zone can cause a myriad of problems upstream and greatly affect product shelf life. Having a strapping or stretch that can withstand the cold and challenging conditions of a dairy processing plant is critical to maintain shelf life.
Produce
Produce takes a different journey, and growers are responsible for ensuring this key ingredient makes it through the supply chain. Corrugated boxes typically used for packaging produce are often stored outside in the fields where produce is picked. If these boxes get wet due to exposure outdoors or otherwise, moisture can spread to the produce and leave them vulnerable to mold or bacteria growth.
Stretch hood technology is ideal in this situation. Using a stretch film with multi-layer technology effectively manages sunlight to reduce condensation and creates an impermeable barrier to liquids, while still providing barcode readability.
While film works great for keeping the product packaging dry before use once packed, additional considerations my need to be considered. Sealing with strech film can cause moisture to build up on the pallet, which can cause produce to rot or spoil early. To create necessary airflow, many growers will apply edge protection to the stacked pallet and secure the load with plastic strapping. This enables the produce to stay well secured and ventilated during transport.
Optimization for automation and shelf life
Additional opportunities exist to optimize shelf life and mitigate the management of demand spikes. Automated storage and retrieval systems (AS/RS) are available to prioritize product picking by expiration date. Finding a solution suited for cold storage that automatically tracks and stores items based on shelf life and expiration is necessary to ensure food products are stored and transported safely.
Beyond COVID-19
Even as demand begins to normalize following the COVID-19 spike, transit packaging solutions can help to improve operations and increase profit for food producers and manufacturers by helping to reduce spoilage, breakage and potential for mold growth, thereby increasing shelf life.
Ensuring safety and minimizing food loss work in tandem. A 2020 report by the U.S. Department of Agriculture estimates that the total value of wasted food -- in-transit, in-store and in-home -- is more than $160 billion annually. It comprises 133 billion pounds (31%) of the 430 billion pounds of food produced in the United States each year.
The report highlights the needed role that technology and material innovations during distribution can play to reduce total food waste.
Innovation and optimization of end-of-line packaging and logistics operations provides a critical opportunity to benefit the whole supply chain. Transit packaging specialists are well-versed in the technology and strategies to help customers effectively pack, bundle, unitize, warehouse and transport products.