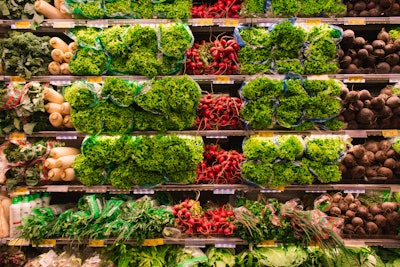
The safe handling of food is a top priority in the third-party logistics (3PL) sector of the cold chain, as consumer health is directly affected by the products that are transported. However, as with any sector, when it comes to the trade of goods and food, recalls still sometimes happen despite the countless safety measures in place. Since 3PLs are responsible for moving this product, food recalls directly impact their businesses, despite often having little to do with the recall itself.
“3PLs are rarely the ones to initiate recalls; typically they receive a notification from a supplier that a product has been recalled (or from their customer, who has received a recall notice from a supplier), and they need to act on that information,” says Jennifer McEntire, senior vice president of food safety and technology at United Fresh Produce Association.
However, once a recall is enacted, it is time for the 3PL to spring into action to ensure the safety of consumers.
“3PLs need to review the recall notices that they have received, and isolate the affected product,” she adds. “This includes product that is still being warehoused, that is in transit and that has already been delivered to customers. Depending on the operation, this may require pulling information from a few different systems. Like other parts of the food industry, recalls are generally executed by a team. For product that has already been distributed, they need to notify their customers of the recall, so that the customer can take appropriate action (assuming the customer is not yet aware). 3PLs should recognize that in the eyes of FDA, they are a registered facility (if they ‘hold’ food). When it comes to a recall, it doesn’t matter to FDA who owns the product—it’s the one that physically handled the product that plays a role in the recall, and a recall plan is required as part of the Preventive Controls Rule for any products with a hazard that needs to be controlled.”
Plan ahead
Because of the importance of situations like these, 3PLs need to have clear plans in place to effectively handle the recall in a timely and efficient manner.
“First thing first, a detailed documented and proven process that is centered around clean data needs to be in place,” says Matt Goker, chief executive officer of Quloi. “3PLs start with flagging the group of products with quality issues. Subject merchandise then is moved to a resolution area where a detailed analysis can be made. Quarantining the recall merchandise is critical since this process drives the decision to repackage, relabel or destroy in accordance with the manufacturers policies. During the entire process, high quality, transparent and two-way information is the make-it-or-break-it phenomenon for a successful result.”
While it is up to the 3PL company to ensure these recalls are handled properly, there are others in the industry that vet procedures to determine their accuracy. For instance, the International Organization for Standardization (IOS) is a non-governmental organization that certifies various companies based on the procedures in place prior to an event.
“ISO-9001-certified companies typically have processes and procedures in place that can be examined before any recall happens,” says Chonchol Gupta, chief executive officer of Rebirth Analytics. “It is also important for companies to practice with mock recalls, so that they can ensure the capabilities of 3PL providers, should a real event materialize. Companies should also be focused on preventing problems before product reaches the 3PL, which requires them to have a better understanding of their suppliers – Tier 1 and beyond.”
Look into the future
In addition to certifications and practice, technology, data and analytics take recall procedures to a more advanced and efficient level. Modern management systems, communication and visibility allow 3PLs to act fast and accurately.
“A food recall requires 3PLs to have robust warehouse management systems and good traceability data,so that good product is not impacted by or ‘flagged’ as bad product,” says Steve Kluting, national director product recall at Gallagher. “They also need proper/effective recall protocols, which should be documented and tested. They also need solid communications capabilities – upstream and downstream – so that the food supply chain that runs through them is not disrupted.”
Technology in the cold chain helps to almost predict the future and allows companies to plan ahead.
“We believe companies continue to explore and invest in system capabilities,” says Johnathan Foster, consultant at Proxima Group. “This includes exploring automation capability to minimize any impacts that staffing might have in their service offerings. Like most other industries, the cold chain industry is working on their future planning strategies. They do not know the type or extent of the next recall, but continue to work on their preparedness for the next eventual issue. In a sense, word-class supply chains and cold chain networks build their plans off of past learnings and occurrences, work the adaptive plans and then subsequently measure the success of the plan being put into action.”
As supply chains grow longer and more complex, the need for these technologies grows along with it. Recalls for temperature-sensitive products in the 3PL space that are most common are usually due to product damages or expiration dates. The longer the supply chain, the more common these events become. Using analytics to provide deep insight into the entire supply chain from start to finish is key, and predictive technologies can help 3PLs pull product faster and avoid disruption all together as problems are spotted and mitigated before a real issue occurs, according to Gupta.
Where there is weak data is where 3PLs will see the most problems, adds Goker
Keeping track of product is an important aspect of recall management.Rebirth Analytics
“In general, when a product recall is required, a sizeable 3PL’s most likely response is a function of its most likely weakest area—data management,” he says. “Since the quality of data depends on entering it properly, preventing a disruption is a matter of having a detailed documented and proven process in place that covers the recall scenario from A to Z. In the pandemic era, things became more challenging for several reasons. Overall supply chain is disrupted, contaminated and compromised. Cold chain recalls get their fair share. It is also worth mentioning that there is an inherent drive of increased recall needs due to contextual quality management issues. We are living times where coordination is difficult at all levels, production is not spared.”
Technologies such as sensors and various solutions also drive efficiency in recall procedure.
“Automated solutions, including barcoding, RFID and integration with manufacturers business and ERP systems for product flow and traceability should be in place,” says Stephen Dombroski, director of consumer markets at QAD. “Today’s advanced technologies such as smart tags and smart labels can automatically trace the movement of product. This information can be used by the 3PL provider internally, but also communicated back to the manufacturer to ensure that their products are being handled properly and on to the retailer.”
Click here to hear more about tracing technologies in the supply chain:
A pandemic’s effect
As the supply chain gets lengthier, the more room there is for error. However, since the start of COVID-19, some data shows that there was a decrease in the number of recalls in the food industry, despite one widespread onion recall in the United Stated during the month of August.
“In my view/experience, there are likely fewer food recalls occurring in the 3PL (cold chain) sector right now; that would mirror the trend occurring generally in the food supply system during 2020 and the pandemic,” adds Kluting. “I’ve seen reports indicating significant decreases (more than 75%) in USDA recall events in Q1 2020, and decreases (approaching 10%) in FDA recall events during the same period. I don’t have reports on Q2 or July/Aug, but I would anticipate that the number of USDA/FDA recall events would be even fewer during those periods, in some part due to decreased regulatory inspections, including product sampling, environmental swabbing and enforcement, as well as plant shutdowns due to COVID-19 outbreaks.”
The beginning months of the COVID-19 pandemic caused the most problems for the cold chain where recall procedures were likely distressed, but as companies settle into the New Normal standard of work during a seemingly ever-lasting pandemic, processes have become more stable.
“The only way that the pandemic may be affecting recalls is if supply chains have been modified,” says McEntire. “This was an issue early in the pandemic when foodservice sales came to a halt and there was a surge in retail purchases. There may still be some new supplier-buyer relationships, but this should be settling down now. A strong traceability system should also be able to accommodate these changes.”
When restaurants first shut down in March and April and food consumption in the United States dramatically altered, many distributors saw a surge of orders canceled and excess amount of food waste, compounding recall standards even further.
“Some 3PLs faced immediate order cancelations (largely from foodservice/restaurant sector), leaving excess food stranded and not easy to move, leading to storage shortages, which is particularly expensive on cold chain,” continues Kluting. “Global supply chains were disrupted by COVID-19 outbreaks, including facility shutdowns (impacting production schedules, volumes and certainty); global lockdown of populations and activities creating less demand by restaurant/foodservice customers and increasing demand by grocery/retailers, and the resulting packaging-size issues (moving from foodservice packaged items to consumer packaged goods); and a less-than-fully-mobile movement of goods through ports and across borders.”
However, order cancelations and restaurant closures are not the only influences from COVID-19 on recalls in the cold chain. In the last few months since the start of the pandemic, staffing greatly altered, as many companies decreased the number of staff on site or had to hire new personnel. This could upend solid recall procedures that were previously in place. Some, like David Rossi, believe technology mitigates this.
“Like any staffing-related service, the aspect of staffing any warehouse or facility has become an issue,” says David Rossi, consultant at Proxima. “In the event of a recall, warehouses and 3PLs that have established recall or block chain systems in place will feel little-to-no-excessive pressure because of the pandemic beyond some minimal staffing constraints. However, if the warehouse and/or 3PL is reliant upon manual processes and system interfaces, they will feel velocity, staffing, and response pressure that is amplified in a pandemic environment.”
Additionally, demands, sourcing and routes all dramatically changed on a dime.
“The pandemic has caused disruptions to all pieces of the food supply chain,” says Dombrowski. “Due to increased product demands, many manufacturers have had to change product sourcing routes and distribution flows that are used to get product to customers. Some warehousing stages might be skipped, including 3PL storage to reduce shipping times. With changes in product sourcing, traceability becomes increasingly difficult, which has forced 3PL providers to become more diligent and has at times slowed the movement of product. A major impact of COVID-19 has been in the procedures of the operations of the facilities. Thorough reviews of product flow and personal physical touches are being reviewed and processes changed. Social distancing and PPE procedures have been added to the normal work environment. Washouts of product movement areas and cleaning of trucks now occur to eliminate contamination from human interaction and potential contaminated food. Track, trace and recall procedures are being reviewed, and in many cases, rewritten to ensure that the process of a recall is not interrupted or impeded by the pandemic.”Proxima Group
Despite the issues COVID-19 caused, exposed broken links in the supply chain supports a stronger future.
“The pandemic has made companies more aware of the risks hidden within their supply chains,” says Gupta. “Companies are realizing that they lack visibility into the multiple tiers of their suppliers (i.e. the suppliers who provide goods and services to the company’s trusted suppliers). No matter how trusted a particular supplier is, if the company lacks visibility into the supply chain of that 1st Tier supplier, they can become blindsided by disruption and recalls that they haven’t anticipated. The haphazard nature of how companies around the world are reopening (or how they reopen, only to be shut down again) has increased problems for companies that lack visibility into the multiple tiers of their supply chains. This undoubtedly complicates the job of 3PLs, which are forced to respond to changes and recalls brought on by supply-side pandemic related issues.”
The future of the supply chain looks bright, as more technology enters the scene and 3PLs become more comfortable using it on top of the discovery of weak links that are fixable. The more weak areas are exposed, the more they can be fixed for a stronger cold chain.