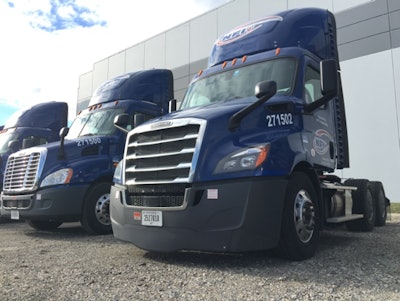
All those trucks you see on the road? They’re carrying almost 71 percent of the freight tonnage moved in the United States. According to the American Trucking Associations (ATA), that’s 10.5 billion tons of freight annually, requiring more than 3.6 million heavy-duty Class 8 trucks and over 3.5 million truck drivers. And, the ATA reports, it also takes 39 billion gallons of diesel fuel to move all of that freight.
Yes, freight makes the economy go, but that 39 billion gallons of diesel also helps contribute to greenhouse gas emissions globally—7 percent, more than the airline industry and the Internet combined, says Business for Social Responsibility (BSR), a global nonprofit organization that works with a network of more than 250 member companies and other partners to build sustainability.
So, with an expanded focus on sustainability, transportation companies and 3PLs are searching for ways to be more environmentally-friendly without losing profitability. It’s not easy.
“There is no single solution that will accomplish transformation without disrupting the business,” says Bill Forster, executive vice president of the food and beverage consulting practice at Maine Pointe, a global implementation-focused consulting firm. “A balanced approach works best.”
Forster suggests such things as retrofitting existing units, replacing retiring units, maintenance routines, utilization and driver behaviors as parts of an overall strategy to build and maintain a sustainable fleet.
“Retrofits of power units and trailers provide a tangible benefit and may be a good entry point of a multi-prong program,” he says. “Replacing retired or less-efficient power units may cost more upfront, but will provide fuel savings throughout the life of the unit,” he explains, adding that, “fuel can count for more than one-third of the total cost of ownership.” Forster says that, “Smart routing to maximize utilization, along with no-idle policies, contribute to a sustainability culture among fleet operators. A safe, sustainable and, at the same time, profitable fleet across every transportation mode used is part of the Total Value Optimization (TVO) approach.”
The fuel experts at 3PL NFI Industries also are controlling fuel costs while boosting sustainability, says Bill Bliem, senior vice president, fleet services, who adds that sustainability is a prime concern for customers. “NFI utilizes various fleet technologies to boost sustainability, including weight reduction, idle improvement, aerodynamic packages, wide-based tires, automated manual transmissions, down speeding, speed governors and electric APUs, to name a few.
“Most customers from both distribution and transportation channels express continued interest in sustainability and NFI’s green initiatives,” he says. “Social responsibility is a core value here, and we continuously implement innovative ways to support customers with sustainable operations.”
It’s Not Easy
As in so many things related to supply chain, change management is at the forefront, notes Maine Pointe’s Forster. “Get to the ‘why’ as soon as possible to align people,” he advises. “Once aligned, everything is possible. Taking a pragmatic approach, and getting resources engaged at all levels of the organization, is essential. Transforming an existing fleet does not happen overnight. Make the case for change, set reasonable expectations and schedules, and then relentlessly execute against the plan—that’s a winning way forward.”
Forster adds that C-Suite involvement and communications, especially from the CEO, is critical to a successful outcome and cost reduction while improving service.
Change, though, doesn’t come without risk, says NFI Industries’ Bliem. “When adapting new technologies, there are the infrastructure and maintenance uncertainties. We look for static partners in both arenas to ensure our risks are mitigated,” he says.
Organizations such as BSR also are involved. Its Future of Fuels group has created the Sustainable Fuel Buyers’ Principles, which provide a framework to catalyze lasting change in the road freight fuel system. Members include such heavyweights as AB InBev, Amazon, Heineken, HP, McDonald’s, Walmart, PepsiCo and UPS.
The Sustainable Fuel Buyers’ Principles include:
- Support low-carbon, sustainable fuel choices. The rise of multiple fuels means a poly-fuel future, but each fleet has unique needs. It is important for suppliers to continually produce more sustainable, low-carbon fuels, vehicle technologies, and infrastructure, preferable in consultation with the buyers who will invest in them.
- Demonstrate competitiveness. Buyers must be able to assess technologies based on financials that accurately capture the total cost of ownership and fully understand the comprehensive costs and benefits of different types of fuels to support the case for new investments.
- Advance investment, pilots and standardization. Buyers are open to mutually beneficial, strategic opportunities that help facilitate investments, pilots and standardization across the value chain. Both bilateral and collaborative efforts will help to overcome these barriers.
- Measurably improve well-to-wheels climate impacts. To justify investments that support progress toward climate goals, buyers must be able to fully understand emissions that contribute to climate change across the full fuel lifecycle and measure improvements with standardized methodologies and metrics.
- Address other relevant sustainability impacts and benefits. All fuels produce other social and environmental impacts throughout their lifecycles. Buyers seek suppliers that demonstrate they address the most material impacts of their products through highest regulatory norms, market standards and certifications, and adoption of global social and environmental standards.
It’s Not Cheap
Building and maintaining a sustainable fleet means more cost, at least initially, acknowledges Forster. “Green power units can cost $20,000 more than traditional gas and diesel counterparts, he says. “In addition, there are potential infrastructure costs associated with electric and alternative fuels. Maintenance, at least in the short run, may be higher due to the availability of training and tools required top perform maintenance and repair operations.
In addition, he says advanced electronics and sensors in new equipment can shut the unit down, and keep it down, until the problem is addressed.
“This leads to additional costs for out-of-hours repairs, expedited shipping and dispatch, and incremental lodging costs,” adds Forster.
To combat this, Maine Pointe recommends approaching sustainability and operational excellence together, helping clients “break through functional and supply chain silos and transform the buy-make-move-fulfill supply chain to deliver the greatest value to customers and investors at the lowest cost to business,” Forster says.
Measuring the Impact
Not surprisingly, metrics are also important. You can’t tell if you’re improving—or falling behind—without them. NFI uses the EPA’s SmartWay emissions metrics as a KPI. Bliem says his company has reduced emissions 80.65 percent since 2011, with an eventual goal of near zero. SmartWay metrics cover various emissions of carbon dioxide, oxides of nitrogen and particulate matter.
Forster advises establishing clear-cut program goals, including a dashboard that reflects progress against those goals and communicating the results throughout the organization.
“Total miles driven, fuel cost per mile driven and CO2 emissions per mile are some customary metrics,” he says. “However, each organization will have its own unique value drivers that are important to stakeholders, customers and associates of the firm. Furthermore, your suppliers’ suppliers [and their suppliers] and your customer can and will add value to the process.”
All that is great, but the CFO is more likely to ask, “OK, but what’s in it for us? What’s the ROI?”
Maine Pointe, says Forster, has worked with several industries that had “hard-dollar savings by combining two methodologies. First, operational excellence, and second, measuring the exact improvements of less empty miles, fewer company-owned vehicles, more public transportation offerings, reduced fleet CO2 (truck, rail barge, air). Our TVO approach typically delivers between 4:1 to 8:1 ROI.”
Lowering the environmental footprint through fuel economy improvement, alternative fuels and great facilities is an everyday function for NFI, Bliem concludes, adding, “Our future fleet is zero emissions; we firmly believe that we will be running trucks on battery electric and hydrogen electric within the next three to four years.”
Barry Hochfelder is a freelance journalist who has covered a variety of industries in his career, including supply chain. He also served as the former editor of Supply and Demand Chain Executive. Hochfelder is based in Arlington Heights, Illinois.