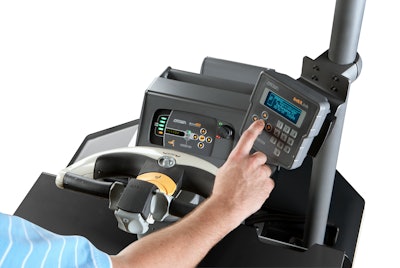
Lift trucks are the workhorses of the warehouse, and like most tools across the supply chain, are increasingly becoming smart—proving an essential source of supply chain data. Lift truck telematics are replacing outdated fleet management systems and, in some cases, manual processes to offer important data to managers related to operator behavior, maintenance, repair information and more.
The data can be used to identify the best—and worst—operators, as well as measure impact, monitor and manage energy use, and alert both operators and maintenance of possible repairs.
“There's a lot of opportunity for customers to add telematics to their vehicles. Your larger, bigger, fleet users have adopted it pretty much across the board, but there's a lot of opportunity for your smaller customers to have one or two vehicles,” says Jim Gaskell, director of global technology business development for Crown Equipment. “Fleets of all sizes can benefit from the data that's being collected to improve their efficiency. My vision or belief is that someday everyone will have (telematics on their lift trucks) just like how today everybody has a cell phone.”
Safety First
When it comes to fork lifts, safety is always top of mind, but regulations put in place to achieve a safer warehouse are not always easy to comply with. A telematics system can help operators check off a few of those safety boxes—quite literally.
Gaskell says one of the primary reasons warehouses adopt telematics is to help operators comply with those OSHA-mandated checklists. Telematics have the ability to not only record that checklist electronically, but also control or shut down the truck if the operator notes the truck is unsafe to operate.
“One of the biggest problems (with the checklist) requirement is the completion of a paper checklist,” he adds. “Paper really only creates a record, and a lot of the times, an operator might write the wrong machine number on the piece of paper, and then after they've collected a week's worth of data, they take that paper off the truck, they put it in the file cabinet and then they find out they have a piece of paper that doesn't belong to any truck.”
With telematics, the system always knows what truck belongs with what check list.
Additionally, telematics can respond to any kind of failure on the checklist, which says there is a reason the truck is unsafe to operate. The system will automatically lock out the truck until supervision comes and fixes the problem or re-enables the truck.
Operator and Fleet Efficiency
Beyond the safety benefits, forklift data can help management track operator skill level. Telematics systems can actually control the forklift based on an operator’s skill level, so that when they sign on to the equipment, their skill level is noted in the system and slows the truck down based on that level.
The system also can provide performance indicators back to management, as well as the operator, such as how often they're driving the truck, lifting the truck, standing idle on the truck, or not on the truck at all. These data points are especially crucial in optimizing your fleet.
“In a lot of cases, customers think they're using their trucks all the time because they see them in operation, but in reality, they use them a much smaller percentage of time,” Gaskell says. “People buy the number of forklifts that they need based on the peak volumes in the warehouse. When they're trying to move goods, there's certain peak times of the day, but at other times of the day, they're not using the lifts all the time and maybe not at all.”
Additionally, an anonymous sign-on is easily detected on the data-driven forklift, holding operators who use emergency codes to a move a truck without signing in accountable.
Improving operator efficiency via data doesn’t come without its challenges. Gaskell notes that management often doesn’t know how to talk to their operators about the data be collecting about their performance, adding, “if you don’t know how to speak to your operator, then your level of service is going to be limited.”
Management needs to be aware of certain operator behavioral patterns, how to address them, and how to coach operators to avoid them. “If you don’t know how to ask the right question to address a problem, you will not have success,” Gaskell says. “In fact, you can even have the operator talk you out of how effective the system is. That’s the primary challenge, because people don’t understand how to manage the people side of things after they collect the data.
“You can look at the data, but you need to know what to do with it, how to address it. The best way to do that is to look at best practices.”
Brace for Impact
Many telematics units are mounted separately on the truck and some eventually will be built right in—but what Gaskell says is even more important than the placement is how the system is integrated into the truck.
“What I call an integrated system is one that uses the truck sensors to also enable the telematics,” he adds.
If a lift truck is driving across an expansion joint that really shakes the truck, a telematics system that is not integrated into the truck’s sensors will log the movement as an impact. An integrated system will recognize that the truck didn't change momentum, and know that the movement should be filtered as a bump in the floor instead of an impact to the truck.
“Systems that aren't integrated, which means they're not connected to the camera system or into the truck's heart, so to speak, wouldn't be able to identify that. They wouldn't know that that truck didn't change momentum, and they would register that as an impact,” Gaskell says. “When you think of a bolt-on system, it's not as important as the modules on the outside. It's how integrated it is to the truck system.”
Maintenance
Like the check engine light in your car, telematics can alert both operators and maintenance personnel that something is wrong. Maintenance can seek out the vehicle and look up the code to decide if the repair needs to be addressed immediately. Or, via the terminal, maintenance can ask the operator to bring the truck in for service. That in itself, Gaskell says “could prevent complete engine failure, complete motor damage, batter damage, anything.”
The maintenance light also gives the service provider an indication as to what part they might need for that vehicle, so if they're traveling over the site, they'll know what to bring.
“The future of this is that all this data is analyzed in the cloud, and you can actually start to determine priority of codes and parts that are driven behind them,” Gaskell says. “The efficiency will continue to grow as that engine continues to get smarter.”