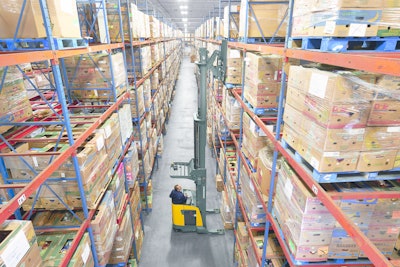
Today’s lift trucks are more versatile than ever. They offer more comfort features, they’re more energy efficient, have greater reach capabilities, more safety features, integrate with warehouse management software, and more. That’s the good news.
The not-so-good news is that all these problem-solving capabilities sometimes make it difficult for a warehouse manager to know what particular lift truck best suits his or her needs. Investing in a lift truck now requires research and evaluation, if not a pilot test.
It’s not your grandfather’s warehouse any more. Welcome to the Brave New World of lift trucks.
Every year, manufacturers introduce more lift trucks to the market. These vendors usually claim a litany of cost-saving capabilities and energy efficiencies, oftentimes citing third-party test results to verify their claims.
At the very least, a materials handling manager is required to 1) research what’s available, 2) determine the organization’s objectives, 3) follow up with manufacturers to find out how their products will meet their needs, and 4) arrange to see lift trucks in action.
Cesar Jimenez, national product planning manager at Toyota Material Handling, U.S.A., Inc., says users must consider site specific needs; will the forklift have to be equipped with accessories such as work lights, strobe lights and/or alarms? The type of rack storage utilized at the location also must be considered: selective, drive-in, push-back, or flow rack.
Thanks to evolving software, today’s lift trucks can integrate with racking systems, voice picking systems, floor sweepers, battery charging systems and more. Hence, the lift truck is best viewed as part of an integrated warehouse management system.
Cloud computing comes
Last year, Crown Equipment introduced InfoLink, a cloud-based, forklift fleet and operator management system that delivers data to help warehouse managers maximize productivity.
InfoLink delivers actionable data through content-rich, interactive dashboards. The wireless system provides fleet-wide visibility into an array of operator and fleet information, such as battery usage, impact history, truck utilization, OSHA compliance, service needs and more through a user-friendly interface.
InfoLink provides multiple paths to forklift fleet optimization depending upon an organization’s priorities and budget. The standard plan provides basic fleet and operator management features, including operator authorization for equipment use, impact detection and alerts, along with real-time equipment status. Another plan offers the ability to track operator productivity, manage planned and unplanned maintenance, and optimize energy resources including battery changes and fuel usage, in addition to the basic features.
Scott Carver, product manager for business and information systems at Raymond Corp., observed that materials handling is becoming more of a service than a product for logistics managers, thanks to more robust software.
“People have a strong interest in the information that the trucks can provide,” he said. He noted that 77 percent of warehouse cost is in labor while only 11 percent is in the price of the truck. Hence, information systems that make labor more economical bring new benefits.
“You can get a full picture of what these guys are doing every single second,” Carver said. In addition, the software can interface with warehouse management software.
Consider the warehouse environment
Food and beverage distributors oftentimes review lift truck needs when moving to a new warehouse or revamping an existing one. They find it makes sense to decide what lift trucks to use when designing or redesigning a facility since truck capabilities can impact the amount of space required.
Fabiano Brothers, a beverage distributor, reconsidered its lift trucks when relocating to a 300,000-square-foot distribution center in Bay City, Mich.
After consulting with Andersen Material Handling, a Raymond Sales and Service Center in Wixom, Mich., Fabiano Brothers used Raymond Model 4700 sit-down counterbalanced lift trucks with cascade single/double pallet handlers. The double cascade attachments allow operators to unload more pallets from a truck at once. Thanks to alternating current (AC)-powered motors (which have gained favor among manufacturers in recent years), the trucks deliver increased uptime, longer battery run times, decreased maintenance costs and, most importantly, moved product faster. Ergonomic features include an adjustable seat and steering wheel and easy-to-reach controls.
Fabiano Brothers also used Raymond Model 8400 end-rider pallet trucks that have a narrower, longer fork than the traditional fork. The forks carry four retail delivery carts at one time. The forks allow order picking and loading functions faster than before.
Energy considerations
As with all types of vehicles, much of the innovation in lift trucks has focused on more efficient use of energy. The growth of electric lift trucks in recent years has resulted in a stronger focus on battery management.
Battery management systems can now give operators access to information on every battery on every truck. These systems can minimize energy use, avoid overheating, overdischarge and other harmful conditions; give fuel gauge readings to help ensure timely charging; and collect and analyze data for recordkeeping and fleet management.
The food industry has been more aggressive moving to electric vehicles due to food safety concerns, notes Wayne Wilde Sr., field technical sales officer at UniCarriers Americas Corp. Electric trucks are also more energy efficient and likewise more sustainable. But the move doesn’t come without costs. Space and equipment is needed for battery charging, including eye washing stations.
The answer to this has been “opportunity” charging, which allows a battery to charge while it’s on the truck, which will save labor for battery handling and reduce the number of batteries needed per truck.
“That has become a more attractive way of handling batteries,” Wilde said.
The Industrial Truck Association (ITA), in its 2013 business trends survey, noted that manufacturers expect to see “opportunity” charging gain ground in the next three years. This allows a battery to charge while it’s on the truck, which can save charge time. The ITA also sees growth in “fast” charging, which is faster than opportunity charging, but requires the battery to be charged outside the truck.
More economical and energy efficient batteries are also coming into play. ITA expects lithium ion batteries to post the most growth potential in the next three years, thanks to low maintenance. However, ITA noted that the lead acid battery remains the most economical solution while also serving an important role as the truck counterweight.
One of the most promising battery innovations is hydrogen fuel cell technology, which eliminates batteries altogether and produces only water and heat as byproducts of combustion. Fuel cell energy is also less susceptible to environmental events that disrupt power.
ITA, cognizant of the benefits of fuel cell technology, cited the following concerns affecting the pace of growth: cost, delivery, distribution and customer acceptance.
Nevertheless, Latham, N.Y.-based Plug Power, one of the nation’s leading manufacturers of fuel cell powered lift trucks, recently closed deals with Sysco, Coca Cola, Wegmans, Kroger, Walmart, and Central Grocers during the last quarter. The company has reportedly sold about 5,000 lift trucks in the last five years.
Other types of energy are also evolving. ITA forecasts the most growth in the next three years for liquid propane gas, followed closely by diesel fuel.
Vehicle features evolve
In the meantime, lift trucks continue to evolve in other ways.
As rack storage systems have continued to grow taller, lift truck manufacturers have recognized that optical visual aids are important, according to the ITA’s 2013 business trends survey. Manufacturers view optical safety aids important as both a safety feature and an efficiency enhancement.
Looking further into the future, manufacturers envision greater use of automatic guided vehicles (AGVs), depending on the application. Crown Equipment, in a recent white paper on automatic forklifts, noted that vehicles that can accommodate both automatic and manual operation to provide the flexibility needed in warehouse environment. One application that has emerged is high-volume picking where the operator is able to remotely advance the forklift, eliminating the need to climb on and off the vehicle multiple times in an aisle.
Lift trucks also continue to improve in the areas of reach, speed and weight capacity.
Mitsubishi Caterpillar Forklift America Inc., the provider of Jungheinrich lift trucks, recently introduced the Jungheinrich ETR 340 – 335d series of pantograph reach trucks. The 3,500- to 4,500-lb. capacity trucks offer faster lift speeds combined with high capacity retention, allowing loads to be staged at higher-rack levels for greater warehouse efficiency and productivity.
The ETR series provides load handling at heights up to 450 inches, thanks to a suspended articulating drive axle that balances load weight for improved stability during cornering and when working at high heights.
Hyster notes that its W45ZH walkie improves productivity by allowing operators to simultaneously transport and lift pallets. Trucks automatically lift the pallet to the maximum fork height without having to hold the lift button during transport. Another feature is Hyster’s “Intelligent Slow Down,” which recognizes when the operator turns the truck during cornering and automatically decreases speed. This allows the unit to be placed in “turtle” function in all handle run zones, minimizing the truck profile and improving maneuverability.
Distribution facilities have more lift truck choices than ever, thanks to enhanced capabilities. Determining the right product requires a manager to examine the organization’s needs thoroughly and match these requirements with the many available options in today’s marketplace.
PICTURES and CAPTIONS:
FIRST 4: MANDATORY
1)
UniCarriers
UNICARRIERS_RPX
CAPTION:
UniCarriers Americas Platinum RPX Series Walkie & Walkie/Rider Pallet Truck is among the battery operated options available.
2
Raymond Corp.
6031
CAPTION:
Trucks such as the 6031 from Raymond Corp. deliver increased uptime, longer battery run times and decreased maintenance costs.
3)
Mitsubishi
ETR 345 (3)
CAPTION:
The new Jungheinrich ETR 340 - 335d series of pantograph reach trucks allow loads to be staged at higher-rack levels for greater warehouse efficiency and productivity.
4)
Toyota
Image 0214-10
CAPTION:
The Toyota 8-Series Electric Stand-Up Rider maneuvers easily around a warehouse.
LAST 4: NON-MANDATORY:
5)
Crown
SX3000-611
CAPTION:
The Crown SX 3000 Series allows operators to easily maneuver in small spaces, such as those commonly found in grocery and retail warehouses and distribution centers.
6)
Hyster_W45ZHD_Walkie2
CAPTION:
The W45Z walkie is available with Hyster’s patented Intelligent Lift which allows operators to simultaneously transport and lift pallets.
7)
Yale
Yale-M025-Application2
CAPTION:
The Yale MO25 multi-level order selector increases accessible pick positions through its lifting platform.
8)
Power Plug
Brochureinsidebtmpic
CAPTION:
The GenDrive from Power Plug uses hydrogen fuel cell technology.