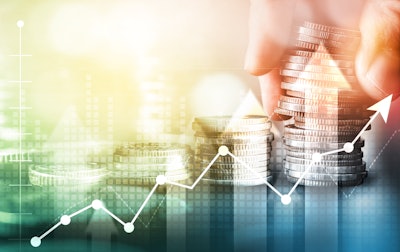
By Sept. 30, inflation in the United States over the previous 12 months was running at 8.2%.
This isn’t an all-time high, but it is the highest inflation has been running at since the early 1980s.
What lies behind this sudden uptick in inflation?
We can boil it down to two factors: the lingering disruption caused by the COVID-19 pandemic, and Russia’s invasion of Ukraine.
The Russian invasion of Ukraine in February and the sanctions it has led to drove global energy prices through the roof, with Europe exposed in particular as we head into winter. The decoupling of Russia from many countries’ energy supply has driven up prices as they have sought other sources of gas, which has in turn driven up global prices further.
This exacerbated the challenging situation the world has faced as it emerges from the COVID-19 pandemic. Huge fiscal support packages from governments around the world kept people in jobs (or helped them if they became unemployed) but also injected an enormous amount of money into key global economies.
At first, this wave of new cash sought out products in limited supply, driving up prices. More recently, countries’ differing stages of emergence from the pandemic meant supply chains that had been optimized for just-in-time manufacturing and delivery struggled to cope with port delays, shortages in vehicles and having key components cut off thanks to local or national lockdowns.
This has been a particular issue in China, with its global manufacturing hubs and attendant port infrastructure still facing regional lockdowns under a "zero COVID" strategy.
All of this has made 2022 a challenging year for supply chain professionals, with inflation exacerbating many of these logistical problems by driving up the cost of labor and fuel, creating a malign feedback loop.
There’s no way of knowing for sure how long this bout of inflation will last, and coping with it will require creativity and innovation – for many, it is the first serious inflation of our working lives.
The U.S. Federal Reserve has been attempting to meet the challenge with five rate hikes so far in 2022 (as of mid October), with more likely to be on the way. Capital is set to get more expensive, then, right as the global economic picture darkens – economists are almost unanimous in predicting a recession for the United States and other key economies in 2023[2].
So, with inflation changing your cost base seemingly day-to-day and the world seemingly growing messier with every passing day – what can you do to bake stability into your supply chain?
Here are some suggestions:
- Pursue visibility across your entire supply chain
Modern supply chains are incredibly complex and can stretch across the globe and span a network of a huge variety of suppliers.
Tracking every element of it can sound like a tall order, but it’s hard to know where you’re going if you don’t know where you are.
Building a full picture of your supply chain can offer you real-time insights into what’s going on across all the businesses you are directly or indirectly transacting with, making it harder for procedures or practices that are risky or unsound to slip through the cracks.
Uncovering these risks is the first step toward managing them, and therefore the first step toward sleeping soundly at night.
- Manage your inventory effectively
Once you have built a picture of your supply chain, armed with this knowledge you can now start to manage it effectively and more confidently.
At its core, good inventory management is when companies can figure out what stock to order, how much of it to order and when.
There’s a lot more to it than that, of course, especially during inflationary periods.
This makes it all the more important to leverage modern inventory management platforms to keep lead-times to a minimum, plan for and amass contingency stocks in response to events, and make sure inventory is distributed and the most efficient way you can.
If inflation is a disruption that makes us more vulnerable to disruptions, good inventory management is the starting point for building the kind of resilience you need to manage them.
- Harness the power of data and analytics
It seems pretty likely that both abrupt shifts in supply and demand and ongoing price increases are here to stay for the foreseeable future. Embedding data capture and sharing throughout your supply chain along with analytical platforms to interpret it means you’ll be able to identify the early indications and adapt your operations accordingly.
Also, with better visibility on where items actually are – rather than where you hope they are – you’ll be able to better control and forecast inventory requirements. Analytics will convert data into actionable reports, dashboards and visualizations that can act as the basis for solid decision-making.
All of these factors are what is needed to manage an environment of dynamically changing energy prices and where transportation costs and delivery times are similarly unpredictable.
- Embrace the potential of early payment solutions
Embracing data-enriched supply chain management and the technology that underpins it in turn creates opportunities for innovation in your financial operations.
For example, offering early payment programs will allow your suppliers to overcome gaps in their cash flows, make decisions based on predictable settlement dates, have cash on hand should the unexpected occur, and ultimately invest in and grow their businesses.
This would deliver obvious benefits in undergirding a successful working relationship going forwards, but more practically it means that a broader range of size of counterparty can now enter your supply chain, given that smaller businesses are often less able to able to soak up variances in cash flows than their larger peers – for obvious reasons.
But why stop there?
Dynamic discounting programs can act as incentives for early payment, rewarding stakeholders for paying early. These tools are growing increasingly popular with larger corporates seeking to support suppliers without impacting their own cash flows.
Also, with environmental, social, governance (ESG) considerations growing in importance for stakeholders throughout the global economy, dynamic discounting offers a compelling model for baking incentives into your supply chain that can reward positive progress on crucial issues like carbon dioxide emissions.
- Optimize your working capital
Simply put, optimizing your working capital is when you examine your organization’s receivables, payables and inventory to discover where your cash is tied up.
You can then optimize this working capital by managing the balance between your assets and liabilities to their maximum possible efficiency. Once your cash is freed up, build a strategy for putting that capital to work for you – whether it’s in investment in infrastructure, research and development, or laying the foundation for the next generation of growth.
Of course, this is a somewhat more complex procedure than just snapping your fingers and making it happen, but deployed right and measured using the correct metrics, working capital optimization might just be the secret to riding out this challenging period.