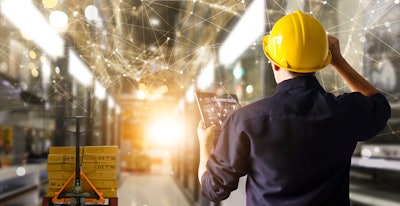
Our 2022 Top Supply Projects award’s mission is to celebrate projects the most transformative and successful cases from the past year. And, this is certainly true for the project featured in this interview.
The editors of Supply and Demand Chain Executive sit down with inVia Robotics executives to discuss how the company was able to install robotics into a 3PL's operations that drove efficiency and streamlined operations. The project was selected as one of SDCE's Top Supply Chain Projects of 2022.
Supply and Demand Chain Executive: Pease describe the project.
inVia Robotics: A 3PL customer of ours was using completely manual processes, and the warehouse team was picking at an average rate of 30 UPH. They chose inVia to implement a comprehensive warehouse execution system (WES) that could create greater efficiencies in its distribution center. This project entailed using artificial intelligence (AI) to better organize storage and movement of inventory, providing tools that would help employees be more productive and using robots to automate picking and replenishment tasks to save on labor costs. Using inVia’s robotics-as-a-service (RaaS) model, this 3PL was able to adopt all these optimizations at its own pace without disrupting any of the existing operations.
Supply and Demand Chain Executive: What was the inspiration for this project?
inVia Robotics: Our customer was looking to increase productivity rates and decrease labor needs given the tight warehouse labor market. Ultimately, their goal was to make their operations more efficient so they could provide better service to their own customers by automating fulfillment tasks they were able to decrease cycle times and get orders out the door faster.
Supply and Demand Chain Executive: How did it make a difference for the company?
inVia Robotics: This 3PL was able to increase productivity rates 1,000% higher than what they were achieving before implementing the inVia Robotics automation system. Before, they were picking at an average rate of 30 UPH per picker. Now they’re picking at an average rate of 334 UPH per picker. This increased overall operational efficiency as well as reduced labor needs by 60%, which was the difference for them to be able to keep delivering on customer promises while struggling to find reliable labor. Using the machine precision of robots to pick and put away items also increased accuracy rates to 99.9%.
Supply and Demand Chain Executive: How does this project provide innovation during the supply chain crisis and disruptions seen this past year?
inVia Robotics: Implementing the inVia system boosted both efficiency and accuracy rates by eliminating uncertainty at every step in the client’s workflow. Not only did this system reduce labor needs by 60%, it also improved the work environment for their team members by leveraging robots to do the dull, monotonous work of traveling through warehouse aisles.
Supply and Demand Chain Executive: What makes this project different than others in the industry?
inVia Robotics: inVia’s system is unique in that it eliminates costly travel time for warehouse workers without requiring an expensive, disruptive implementation. inVia Picker robots are autonomous mobile robots (AMRs) that retrieve and put away goods in the warehouse completely autonomously. People don’t have to travel with them, so hourly wages aren’t going toward warehouse walking. They’re going toward high efficiency picking. inVia Picker robots bring goods to people, and people sort and pack out orders.
The robots are also mobile, operating as a fleet, which means they can be dropped into an existing facility and be operational in a matter of days. Traditional automation systems that deliver the high throughput of an inVia system require new infrastructure build outs that are costly, time-consuming, and disruptive.
Supply and Demand Chain Executive: How did/does this project fit into the overall operations of the company?
inVia Robotics: By utilizing AI to better organize storage and movement of inventory, providing tools that would help employees be more productive and using robots to automate picking and replenishment tasks to save on labor costs, the 3PL was able to better meet their customer SLAs. No major infrastructure changes were needed within their facility and operations were streamlined to improve efficiency and accuracy. All these improvements allow them to consistently deliver on customer expectations, which leads to greater retention. They’re already making plans to expand their business based on their ability to now accommodate more throughput and offer more value-added services.
Supply and Demand Chain Executive: What do you think the future holds for this project?
inVia Robotics: This project has already expanded from initially implementing inVia Logic WES software to increase productivity of existing labor. After seeing the ROI from their initial investment, they quickly elected to add automation to their operations to realize further gains. Having seen the robots pay off as well, they are in the process of moving to a larger facility where they can take advantage of additional business opportunities. inVia’s robotics-as-a-service (RaaS) model makes it easy for them to add system capabilities as they expand their business. It eliminates the risk of customers having to make big CapEx outlays with economic uncertainties. They can invest as their revenue is growing.
This content was created in partnership with inVia Robotics.