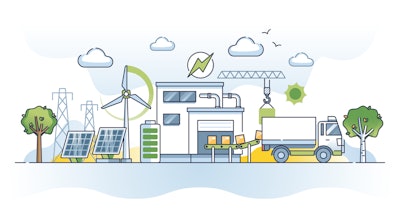
Americans have grown accustomed to buying anything online and having it arrive within days or sometimes hours. Despite the attention paid to transportation modes, the key to speedy delivery lies in the warehouse.
Same-day and next-day delivery requirements of e-commerce are driving a shift to smaller warehouses and fulfillment centers that hold inventory closer to the consumer. Coinciding with the transformation of the retail supply chain, climate change across the globe has reached a point where there is a growing effort to study and reduce the carbon footprint of logistics activities in these facilities.
Here are seven trends warehouses have embraced to reduce their environmental impact and enhance operational efficiency, helping contribute to a more sustainable future.
- Energy efficiency: Warehouse owners have installed LED lighting systems, motion sensors to control lighting, and efficient HVAC systems. Evaporative coolers, also known as swamp coolers, have become a viable alternative to refrigerant-based air conditioning, especially in dry, hot conditions. These coolers work by pulling in outside air and passing it through cool water. Some warehouses are also integrating renewable energy sources like solar panels and wind turbines to generate clean energy on-site.
- Green Building Materials: Facilities are being constructed or retrofitted using sustainable building materials. This includes using recycled or locally sourced materials, paints with low volatile organic compounds and environmentally friendly insulation. Green roofs and walls are also gaining popularity, as they reduce stormwater runoff, improve insulation and provide additional green space.
- Water Conservation: Warehouses are implementing water-saving measures, such as low-flow plumbing fixtures, rainwater harvesting systems, and efficient irrigation techniques. These initiatives help reduce water consumption and reduce the strain on local water resources.
- Sustainable transportation: Facilities are focused on efficient transportation practices to reduce emissions and environmental impact. Cross-docking is an example of a logistics process that optimizes inbound transportation and inventory management. In a cross-docking facility, inbound shipments, usually less-than-truckload, are received, sorted, and transferred to outbound trucks, which are fully loaded. In other words, products come in one door and out the other, without being stored in between. Cross-docking can be used for a variety of different product types, including perishable goods, high-turnover items and time-sensitive shipments. Successful cross-docking operations reduce the number of trucks traveling to a central warehouse and improve the flow of products through the distribution process.
- Packaging and waste management: Reducing waste is a key initiative within e-commerce supply chains, with much of the focus on packaging. Effective waste management practices include recycling programs for paper, plastic, and other materials, as well as composting organic waste. Logistics providers also are keen to reduce the use of Gaylord shipping boxes or reuse more of them. These bulk bins are ideal for commercial use, but they are not easy to manually unload. Workers often have to cut crescent-shaped holes into the bins to remove items from the bottom, which renders them too damaged to reuse.
- Automation and artificial intelligence: Automation equipment and software, such as robotics and artificial intelligence, are being employed to improve workflows and operations inside warehouses. Sorting systems improve the flow of products while also automating repetitive and potentially injurious manual sorting tasks. One indirect benefit of robotic picking is that it preserves Gaylord boxes. Automated storage and retrieval systems allow for more efficient use of floor space, increased order-picking accuracy, and fewer labor constraints due to labor shortages. AI takes robotics and automation to the next level. Machine learning algorithms enable robots to acquire knowledge, improve performance through experiences and adapt to changing environments. AI-driven perception systems enable robots to interpret visual and sensory data, enabling object recognition, navigation and pick-and-place.
- Monitoring and analysis: As warehouses become more automated, they are using data and analysis tools to track and optimize energy consumption, water usage and waste generation. Data analysis also helps predict equipment maintenance needs and prevent failures. By analyzing patterns, detecting anomalies and forecasting potential issues, organizations can proactively schedule maintenance tasks and minimize downtime.
Fully embracing these trends requires employee engagement and education in sustainability initiatives. Training programs and awareness campaigns are essential to encourage employees to adopt eco-friendly practices and promote a culture of sustainability.
Customers also are looking for logistics partners with strong environmental credentials. By adopting sustainable practices and reducing carbon footprints, warehouses can achieve third-party validations, such as the Carbon Neutral certification from Natural Capital Partners. Green certifications provide a clear and recognizable way to distinguish environmentally responsible companies in the marketplace.