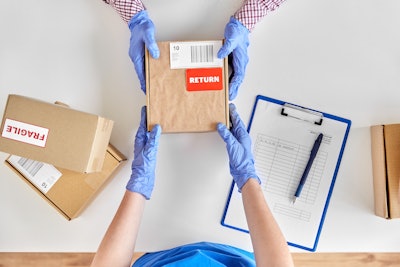
The e-commerce boom, fueled by unprecedented convenience and no questions asked returns policies, has created an expensive problem for retailers, costing them about $218 billion annually as 20% of their inventory is now tied up in the returns process. Retailers must now reevaluate every aspect of their reverse logistics process, including disposal options, return procedures and re-sale strategies.
Retail has a convoluted returns problem. The word return alone carries its own stigma – used, broken, discarded – with a consistent narrative of statistics that equally share impact in dollars and the environment - 25% of returns, 5 billion pounds of goods, arrive back to retailers “unsuitable” for restocking with insane amounts of packaging and emissions waste to coincide as well.
So, how did we get here and what can be done to fix it?
The good, the bad, the future and the truth
· Incentivize in-store returns. This is the biggest misconception in all of retail with the notion that it brings valuable foot traffic -- this is false. The only case when foot traffic from a return is beneficial is when it occurs at replenish retail locations, like grocery stores.
The argument still stands for the in-store return to reduce shipping costs or even put returned items on the store shelf. But again, we find ourselves in the hazy convoluted space where perception isn’t reality. These items bought online and returned to store (BORIS) do not wind up back on a shelf and if they do, it’s on the discount rack and items that are brought to the back wind up being liquidated because of how long it takes to get back to a warehouse.
Partnering with a big box store to bring a returns center to their brick-and-mortar store is 95% more cost effective than a shipping label, removes fraud and even pre-sorts on pallets for liquidation. There are some outliers like manufacturing refurb contracts, but this is also why consolidation points do not accept third-party seller goods and try before you buy because that product needs to be reinjected.
· Charging for returns. Some retailers have said enough is enough and are changing their returns policies. Some are no longer paying for return shipping costs, limited return policy days, deduct fees for returns made by mail and more. But these charges are not there to cover the retailer’s costs as much as they are in place to deter the consumer from returning items in the first place.
· Tiering for returns. Other retailers are looking at returns from a loyalty perspective, the more loyal the consumer, the more lenient the policy.
Companies are beginning to segment returns into tiers and rewarding their best consumers. For example, the best customers (based on how much they spend with the retailer annually and how often they return) get perks like free shipping and unlimited returns.
· New technologies. Faster recovery enablement (reselling items quickly) is essential, as retailers can lose 10% per week of the value on items as seasons, trends, product lines and technologies change. Speed of recovery in these time sensitive situations is imperative to saving retailers tens of hundreds of millions of dollars.
· Emerging solutions and technologies. Data-driven solutions that make decisions based on each individual customer’s shopping habits are emerging. Companies are applying their technology to the retail world and are successfully curbing excess and fraudulent returns.
Returns are a part of shopping culture and play a major impact on purchasing decisions. It’s improbable that we are ever going to eliminate them. But we can take a different approach to how we manage them by transforming the problem into a solution that recaptures customers/dollars, data-driven decisions, waste reduction and supply chain efficiencies.