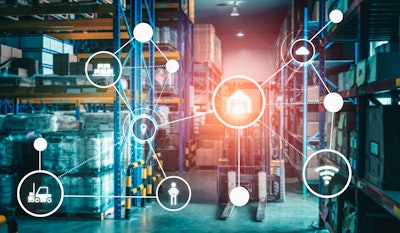
As e-commerce continues to soar, customer expectations are rising in lockstep, fueling a surge in demand for speed, efficiency and reliability. In this ultra-competitive landscape where speed and reliability are the hallmarks of a superior customer experience, shipping times have emerged as a key driver in customer loyalty and satisfaction. With approximately 75% of customers reporting, they would likely not purchase from retailers with delivery times longer than two days, businesses are under intense pressure to deliver.
The frenetic pace of eCommerce is par for the course, though fluctuations in volume and demand are regular occurrences. While it's always exceptionally busy, certain periods of the year bring even more intense activity. However, with the right plans and tools in place, these periods of heightened demand can be navigated with ease, barely registering as a blip on the radar of the retail and supply chain industries.
Take the holiday shopping season, for example. Those whirlwind months are looming large, poised to drive already-skyrocketing demands to unprecedented heights. October is when 50% of consumers say they’ll begin holiday shopping, if not sooner. To avoid getting caught off guard by the inevitable traffic spike, the retail and supply chain sectors plan around the clock for holiday sales. And this strategy doesn’t end with the conclusion of December.
Throughout the year, various shopping peaks — such as back-to-school season and the post-New Year fitness equipment frenzy — require proactive preparations to ensure a seamless and efficient customer experience. These fluctuating demands, on top of eCommerce’s high-volume norms, necessitate effective warehouse management, which facilitates the easy navigation of ebbs and flows to support a consistently high level of service.
Warehouse Management Systems (WMS) are equipped with capabilities to shed light on complex operations and streamline processes to offer potential solutions to these challenges. The specific benefits offered by WMS are diverse and effective, designed to help businesses of all types and sizes meet the evolving needs of their customers.
Optimizing the Power of Warehouse Management Systems
To maximize efficiency and productivity in warehouse management, it's crucial to optimize various aspects of the order fulfillment process. Warehouse management teams can significantly improve their overall performance, prepare for peak seasons, and help raise customer satisfaction by implementing strategies like these:
1. Warehouse Layout
A well-thought-out warehouse layout is fundamental to maximizing efficiency. By re-evaluating layout, third-party logistics companies can significantly reduce travel time within the warehouse, which directly impacts productivity. Here are some tips:
- Receiving area: Quickly identify where inventory should go to keep the area clear and get items into circulation faster.
- Forward picking: Store high-demand, fast-moving items in easily accessible areas to lower time and cost per order.
- Returns area: Set up distinct transition and evaluation locations to streamline the returns process.
2. Order Batching – Using Intelligent Automation
Order batching involves releasing groups of similar orders into the warehouse at specified times. This method can coincide with pickup schedules, ensuring Service Level Agreements (SLAs) are met without delay. Grouping orders with similar steps expedites the picking process and maintains high levels of efficiency – something a WMS can enable.
3. Barcode Technology
Implementing barcode technology can dramatically speed up warehouse transactions. Barcodes replace the need for manual data entry, allowing for faster processing and greater accuracy. This technology provides real-time data capture, enabling managers to oversee activities more effectively and maintain stringent quality-control measures.
4. Fine-tuned Picking Process
Optimizing the picking process involves grouping orders that involve similar steps to streamline operations. Using barcodes can further reduce walking time and increase picking efficiency. This boosts productivity and ensures higher accuracy in order fulfillment.
5. Optimized Packing
An efficient packing process provides several benefits, including quality control, content tracking, and audit trails. Formalizing a quality-control process with barcode scanning saves time and reduces errors. Content tracking identifies what products are in each package, and an audit trail offers visibility into every order packed.
6. Inventory Management
Real-time inventory accuracy and tracking are crucial for maintaining smooth operations. The utilization of WMS ensures e-commerce storefronts display correct inventory levels. Preventing backorders and costly interruptions is essential as 67% of survey respondents polled by Stitch Labs indicated that being out of stock after an order is placed or overselling are the top inventory mistakes that lead to lost customers. Tracking every inventory transaction with barcode technology helps to maintain accurate levels and ensures continuous order flow.
7. Efficient Returns
Handling returns efficiently is vital, especially during peak seasons. Setting up a clear returns process and training team members on it can eliminate confusion and reduce the need for verbal instructions. Use transition locations to move returned inventory to stock locations or other designated areas, ensuring a smooth process.
Leverage WMS to Stay Ahead of Curves Throughout the Year
E-commerce knows no busy season – the demand is in full throttle all year long. However, certain times do add pressure, and businesses rely on warehouses to maintain a seamless and uninterrupted flow of operations, without exception. The time is always right for supply chain management teams to ensure warehouse operations and software are up to par. Implementing a Warehouse Management System can significantly increase visibility, efficiency, and shipping speed — key factors in meeting evolving customer expectations. Those who make the shift can expect positive results quickly, as it’s not uncommon for users to report a 400% or more increase in processing daily orders after moving to a WMS.
Proactively optimizing warehouse operations with a WMS gives teams a leg up on the competition and ensures businesses are well-prepared all year long. Taking steps now to enhance warehouse efficiency rather than waiting until later in the year will make a big difference when it matters most.