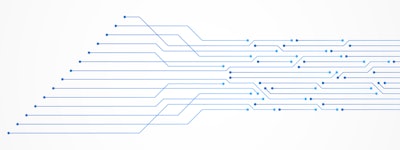
Demanding industries like trucking and manufacturing have long relied on internal combustion engine (ICE) forklifts, even in indoor settings. That’s changing, especially as both governments and companies establish goals for reducing emissions. Electric motive power is increasingly popular among high-intensity operations, and electric options for forklifts are no longer limited to lead-acid batteries. The opportunity to electrify is more real than ever, but what should you know about electrification of indoor forklift applications?
1. Are indoor operations really making a shift to electric?
According to data from the Industrial Truck Association, retail bookings for electric counterbalanced (class 1) cushion tire forklifts are increasing compared to bookings for ICE counterbalanced trucks with cushion tires primarily intended for indoor applications (class 4). In 2018, just 31.5% of cushion tire bookings were electric. In 2023, that number increased to 45.5%, showing a growing demand for electric equipment. Experts expect this trend to accelerate further in coming years as states continue to implement more stringent air-quality regulations.
2. Can electric power options really offer comparable performance to ICE?
The legacy electric motive power source, lead-acid batteries, possesses certain characteristics that hinder its ability to deliver performance on par with ICE, especially for power-hungry indoor applications:
- Lead-acid batteries are generally too large and heavy to be adequately scaled up to satisfy the energy draw of higher capacity lift trucks.
- Power output diminishes as a lead-acid battery’s charge depletes.
- Charging a lead-acid battery can be space-intensive and time-consuming for operations that require more than one battery per truck, requiring about 20 minutes for the operator to switch out the battery, followed by approximately 16 hours of charging and cool-down time.
By contrast, newer electric options like lithium-ion batteries provide consistent power until depletion, putting them more in line with ICE performance. Hydrogen fuel cells also have a similar operating profile as ICE from a time and convenience standpoint, often taking only three to five minutes to refuel. Lithium-ion and thin plate pure lead (TPPL) batteries offer faster charging times than traditional lead-acid and are designed for opportunity charging.
3. What are the benefits of switching from ICE to electric?
All electric options can help your company meet regulatory standards and reach emission reduction goals. Lithium-ion and TPPL produce zero local emissions, while lead acid does emit hydrogen when charging. However, none of these sources emit carbon dioxide. Deploying a truck fleet that doesn’t emit smells or greenhouse gases can also help enhance working conditions for your operators, who benefit from improved air quality and reduced noise levels of electric relative to ICE, especially in indoor settings. While all lift trucks require maintenance, the requirements associated with particular power sources vary. Electric drivetrains have fewer components and less complexity than ICE, and lithium-ion in particular requires zero battery maintenance or equalization. The reduced maintenance requirements and workload associated with electric trucks can be an important aid for businesses.
Switching to an advanced source like lithium-ion can also help to minimize downtime for both operators and equipment. Lead acid batteries require eight hours of charging time, eight hours of cooling time and an additional 20 minutes of changeout time – a process that must be repeated every four to eight hours in applications with multiple batteries per truck. Lithium-ion batteries charge more than three times as quickly, in as little as one to two hours, with the ability to top up and charge when an opportunity is available during lunch or another break in the action. No cooling time is needed, so once the battery is charged, the equipment is good to go.
An additional benefit of electric lift trucks is access to systems that are not available on ICE trucks, like operator assistance solutions. These help to support operator awareness and adherence to safety best practices by alerting the operator and automatically adjusting forklift performance like speed or lift based on truck stability, facility rules and proximity to obstacles, people and other trucks.
4. What are the concerns?
Electrification can present advantages for many facilities, but every operation is different. Several factors influence appropriate motive power choice, including operating time, temperature, space availability, cost tolerance, local utility grid dependability and relevant emissions requirements. For example, operations located in areas with weak electrical grids become more susceptible to interruptions as charging requirements become more intense. Likewise, going electric may require your facility to dedicate extra space for battery storage or to upgrade its electrical and other infrastructure to support the necessary chargers or dispensers. These are all considerations that are reviewed as part of the electrification process.
5. Compared to ICE, is going electric going to break my bank?
Generally, electric power options have a higher acquisition cost, but have a lower cost of operation and generate a strong return on investment.
Electric power options range in cost from one type to another and will also vary depending on the particulars of your location and operation. Taking advantage of available grant and incentive programs can help offset the costs of electrification. Programs and opportunities will vary by state, but resources are available to help make the conversion to electric more financially appealing.
Rightsizing lithium-ion batteries and chargers to your infrastructure and operational needs can also help contain costs, as overestimating the size of the battery and charging speed needed to accomplish your goals can lead to unnecessary overspending. Estimating and comparing not just the initial acquisition expense, but the total cost of operation over the life of the truck, including factors like energy spend, maintenance, space and labor costs, can help you to arrive at the most cost-effective power solution for your unique operation.