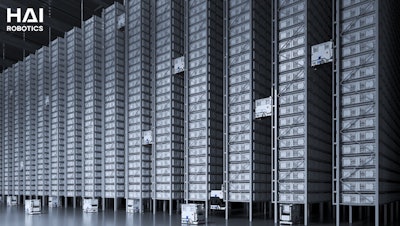
Hai Robotics released HaiPick Climb, a robotic solution that simplifies goods-to-person automation, enabling warehouses and distribution centers to retrofit existing facilities more easily.
“We know that many warehouses want to automate but are put off by the complexity and cost,” says Richie Chen, founder and CEO of Hai Robotics. “That’s why we created HaiPick Climb — to deliver powerful automation without the need for major facility modifications. Our system is built on simplicity, requiring only standard racking and minimal floor preparation while providing top-tier performance.”
Key takeaways:
- Built around the HaiClimber robot, an intelligent, compact climbing robot, HaiPick Climb is designed to boost efficiency, increase storage density, and scale operations — all with minimal infrastructure requirements.
- HaiPick Climb operates by attaching climbing channels to one side of nearly any industry-standard racking. Compact robots travel up and down these channels, retrieving totes from both sides of narrow aisles. Since the system mounts from just one side, it requires less infrastructure and is more tolerant of floor irregularities than typical AS/RS, reducing facility preparation and cutting implementation costs.
- Totes of goods are automatically delivered to one or more ergonomic workstations.
- HaiClimbers freely navigate under racking, allowing for the most direct and optimized path for each tote delivery and avoiding robot congestion that can occur in aisle "highways." Robots have direct access to every tote at all times, eliminating the wasted response time associated with searching or digging.
- Traveling an extreme speed of 4 meters per second (13 feet per second) and climbing at 1 meter per second (3 feet per second), the HaiPick Climb system can process 4,000 totes per hour within a 10,764-square-foot space. Totes are delivered to workstations in as little as 2 minutes after order receipt — 34% faster than traditional AS/RS — allowing for extended order cutoff times for same-day fulfillment.