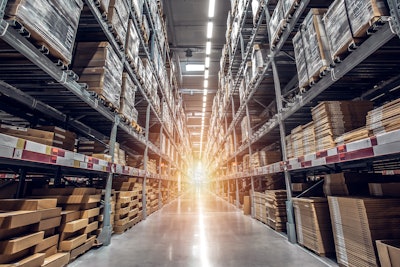
Warehouses are critical to thriving modern economies and supply chains. They can also be dangerous places to work. The fast-paced work environment, use of heavy-duty industrial equipment, and constant movement of large inventory contribute to a heightened risk of workplace accidents and injuries.
It’s a problem that’s becoming more difficult for employers to solve.
According to an analysis by the Department of Labor Office of the Inspector General, the number of reported injuries and illnesses in warehouses doubled between 2016 and 2021, a trend that has continued unabated ever since. Solving this problem is both a moral imperative and a practical requirement. Attracting and retaining top talent is an industry-wide challenge, making enhanced workplace safety a competitive advantage in the labor market.
Here are four of the best practices for improving workplace safety in warehouses heading into 2025 and beyond.
#1 Provide the Right Equipment
The right equipment can distinguish a safe workplace from a danger zone. While this can mean investing in expensive machinery to automate hazardous tasks and reduce worker strain, providing the right resources can also mean investing in often-overlooked equipment that makes an outsized difference in employee safety.
For example, casters play a central - if often unobserved - role in warehouse safety. The wrong caster wheels contribute to many of the most common warehouse injuries, including overexertion, muscle strain, and repetitive stress injuries. The right caster wheel style and material will minimize the push force needed to move objects, making workers less likely to be injured when pushing or propelling material across warehouse spaces.
Warehouse work may require taxing manual labor, but the right equipment makes the job easier and reduces the risk of immediate or long-term injury.
#2 Incorporate Automation When Possible
Many businesses are working tirelessly to streamline their operations and guard against supply chain disruptions by modernizing their warehouse operations.
Increasingly, this means adopting automation technologies. These solutions promise to solve everything from labor shortages to workplace safety. Unfortunately, as one McKinsey and Company report notes, “A warehouse automation revolution is underway, but too many projects are not delivering the results.”
Instead of considering automation as a holistic prerogative, prioritize solutions that increase efficiency and safety. For instance, implementing automated line delivery carts for material transport across warehouses enhances worker efficiency by allowing them to focus on higher-value tasks and avoid potentially injurious manual labor.
Similarly, upgrading from manual to motorized delivery carts minimizes the physical strain on workers, reducing their exposure to potentially harmful pushing and pulling activities. When possible, incorporating automation, with an emphasis on safety, can help people be more productive and workplaces be safer.
#3 Prioritize Noise Reduction
Warehouses are full of hazards. Some, like heavy machinery or falling objects, are obvious. Others are smaller and more difficult to identify but just as damaging.
For example, the Centers for Disease Control and Prevention (CDC) reports that 40 percent of all transportation and warehousing workers are exposed to hazardous noise. As a result, 12 percent of noise-exposed warehouse workers have a “material hearing impairment.” In this case, providing hearing protection can help mitigate the effects of loud noises.
However, even seemingly small things, like caster wheel sounds, can cause serious injury over time. By accounting for the small things, companies demonstrate care for their warehouse teams by making them safer (and consequently more productive) workplaces.
To ensure you’re capturing all of the ways to make the biggest impact, it’s also recommended to work with an expert whose specialty lies in providing strategies to reduce noise inherent in your overall facility processes. Taking this approach also allows warehouse managers to remain compliant with standards set by the Occupational Safety and Health Administration (OSHA), which requires employers to implement hearing conservation programs when noise exposure exceeds 85 decibels on average over eight working hours.
#4 Teach Safety Best Practices
Don’t assume that warehouse safety is intuitive. Teach and train every employee - from new hires to established veterans - warehouse safety best practices.
This timely and comprehensive training should cover the proper use of equipment, safety protocols, and procedures. It will comprise:
● Regular training sessions for all employees
● Comprehensive coverage of proper use of carts, maintenance schedules, and safe material handling techniques
● Hands-on practice with equipment
● Documentation of training completion for each employee.
Ultimately, workplace safety requires actions from the people who navigate these complicated spaces every day, and safety-first warehouses will teach their employees to identify potential hazards and implement best practices into their daily operations.
Safety First Makes People Better and Organizations Stronger
If warehouses are going to be as productive, resilient, and agile as possible, workplace safety has to be the cornerstone of the organization. Put differently, warehouse safety isn’t just about compliance or risk management. It’s about building a workplace where employees can thrive, which produces lasting business.
As warehouse business leaders approach the end of the year and a busy holiday season, reassessing the best practices to keep their team safe in 2025 and beyond is best achieved by focusing on optimizing equipment, strategic automation, and reducing hazards. These simple steps can make any warehouse safer while advancing a strategic imperative that drives operational excellence and sustainable growth. It’s possible and worth pursuing now.