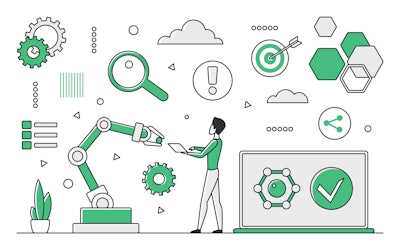
The U.S. Food and Drug Administration (FDA) recently unveiled new guidance to encourage the adoption of continuous manufacturing, particularly among pharmaceuticals that have been slower than food and beverage companies to adopt the practice. According to the FDA, continuous manufacturing (CM) has the potential to improve product quality and reliability, lower manufacturing costs, reduce waste, and increase manufacturing flexibility and agility in response to product demand. Ultimately, it’s a key step to reduce food and drug shortages and drive efficiency.
But as more and more manufacturers embrace continuous operations, incorporating this approach throughout their entire supply chain, including packaging, labeling and distribution, is key to realizing its true benefits.
Continuous Manufacturing in Label Printing
When it comes to label printing, CM technology keeps printing presses running 24 hours per day, which helps reduce non-productive time, optimize press uptime and get products on shelves faster.
For example, automatic splicers technology allows the presses to run non-stop at optimum speed and reduce waste. The automatic splicers make it possible to change rolls without stopping production, and automatic turrets allow the inspection and boxing of products while the press continues to run. Without this technology, many additional presses would be needed to cover the lost capacity of the downtime for changing rolls. This lost production time could equal hundreds of hours per day depending on facility size.
Enterprise Resource Planning with Inventory Management
Choosing the right Enterprise Resource Planning (ERP) system is crucial for a successful continuous manufacturing strategy – for both manufacturers and their supply chain vendors. It allows for real-time data that drives proactive decision-making, production efficiencies and schedule attainment. Real-time information flow provides an advantage in pivoting and adjusting operational plans quickly to meet ever-changing customer needs.
In the labeling process, supervisors can see when the press is not running to speed from the ERP dashboard, which allows them to respond to the issue and help the operator return the press to its proper run speed. Prior to real-time data, companies would have to review reports from the previous day and then solve issues retroactively. It was more reactive than proactive and many times the jobs were already off-press. Ultimately, real-time data allows workers to correct issues as they come up and get ahead of future issues.
Increasing efficiencies through a cloud-based ERP strategy helps to maximize inventory levels to deliver exactly what customers need when they need it. A comprehensive, data-driven inventory strategy with both raw materials and finished goods ensures product availability and minimizes production disruptions.
Realizing the Benefits of Continuous Manufacturing Requires Skilled Workers
The printing industry, like most industries in manufacturing today, has an aging workforce with fewer people looking to get hired. Automation via continuous manufacturing can reduce the amount of manual labor and manual intervention in processes, helping companies do more work with less labor. Integrated systems coupled with a continuous manufacturing approach can complete quality inspections, and box and palletize products to get them ready for shipment. Today, these processes may require two to three people to complete, but technology could reduce that to one.
With advancements in technology comes a greater need for a skilled workforce and company training programs, however. The Manufacturing Institute reported that manufacturing companies are finding a greater need for individuals with data analysis, critical thinking and interpersonal skills to help leverage the data that technological advances have produced. Manufacturers will need to enhance or initiate new upskilling opportunities for existing employees, and the qualifications for new employees will need to become increasingly more sophisticated.
While continuous manufacturing helps address several challenges faced by manufacturers today, companies must ensure their entire vendor ecosystem is adapting to this approach to realize its true benefits and train their workforce to adapt to the automation continuous manufacturing requires.