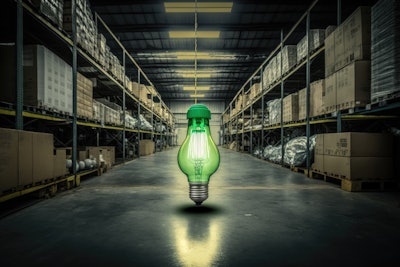
Warehouses have a significant role to play in the green transition of today. Enhancing the sustainability of warehouses, particularly by improving their energy footprint, offers environmental, economic and social benefits.
Warehouses are traditionally energy-intensive by consuming large amounts of electricity for lighting, heating, cooling and operating machinery. So, it's no shock that reducing this energy consumption can mitigate climate change. Antonio Mendonca, director of Engineering at Concentric, says that as more companies think about how they can make a real, long-term impact through sustainability programs that are beneficial to the environment, they will need to first think about how they’re defining sustainability.
"Corporate sustainability has become an expectation, not just a nice to have. Yet despite the outpouring of programs and money dedicated to fueling entire divisions dedicated to sustainability improvements, while well intended, the impact in large has not produced anything truly sustainable. I challenge more leaders to consider this: if the environmental metrics your company is seeking aren’t sustainable financially or operationally, then what is the point?", asks Mendonca.
The rewards of planning and executing a sustainable plan in the warehousing sector come in many forms including lowering carbon footprint, lowering environmental impacts, better and ultimately safer working conditions for employees, an overall improvement of productivity and reduced costs.
Mendonca explains the start to reaping these benefits comes in 3 steps:
Step 1: Evaluate the power use in your facility. Start by taking a look at where your current power is coming from. An audit of how your system is powering everything from production equipment to HVAC systems to lighting and beyond will give you a base to best understand your starting point.
Step 2: Optimize your current power system. Look closer at your utility data - how is power being used right now and what happens during peak and off-peak periods? What changes can you make based on evaluating the design of your current system - what’s working and what isn’t? Do you have automation in place? When can you dial back your AC or heating, and are you doing that? What is driving your energy consumption and what changes can be made accordingly? These questions will inform a strategy and the necessary change to drive the greatest impact.
Step 3: Take a deeper dive. A comprehensive study will help you take a close look at your material handling operations and find key areas of improvement. Take a look at your whole operation - not just your power - and consider the criteria below as you assess the best course of action:
- What are your maintenance practices? Are they proactive or reactive?
- What are your key business processes through time studies?
- What are your leaders’ goals? Both on the warehouse floor goals and leadership goals. Do interviews and make sure they’re aligned.
- Do a deep power assessment including a peak power evaluation. How do you operate today and how do you want to operate tomorrow?
- Material handling equipment is the #1 power consumer at your warehouse. How many assets are you using? Can some be eliminated? What is your charging strategy and how does battery technology affect your productivity?
- Are you recycling everywhere you can? When it comes to power, are you recycling 100% of all the batteries utilized in every system?
- Is there technology available to make your facility safer? Good automation can lower risk for your workers and reduce hazardous situations from occurring in the first place.
Improving the energy footprint of warehouses is an obvious move in a better direction. As the demand for sustainable practices grows, warehouses that invest in energy-efficient solutions and strategy will be better positioned to thrive.