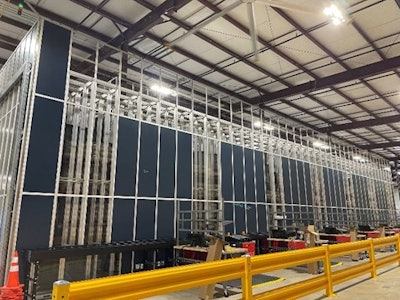
Automating supply chain processes is a popular trend right now. It can enhance productivity in your facility and help your business achieve better results than ever before. Companies are looking to automation as the answer to improved warehouse and distribution operations for speed, reliability and flexibility.
According to McKinsey, the overall automation market is rapidly growing. Their expert sources anticipate that shipments, powered by robotics, will increase by up to 50% each year through 2030. They also expect warehouse automation to grow by more than 10% per year. Further, automation promises to help organizations tackle pressing supply chain problems: addressing labor challenges, improving fulfillment quality and safety, maximizing space utilization, and increasing throughput.
While these are all significant benefits to the bottom line, when evaluating the use of an automated warehousing system for your business it is important to note that it is not a universal solution. Like any significant investment or change, implementing an automated system requires patience and planning. Warehouse managers and business owners should evaluate their current processes and future goals to find the best-fit solutions for their unique workflows.
Several factors contribute to the successful integration of an automated system into your warehouse facility. To maximize your investment, consider these five best practices.
1. Evaluate Current Processes First
Before installing an automated system, it's important to evaluate current processes. Failing to do so could result in inefficient workflows that waste time and money. If you want your automated solutions to provide real value to your company, start by focusing on areas for improvement in your existing operations.
Identify the weakest parts of your current workflow and determine whether there are ways to improve before investing in automation. Optimizing current practices makes it easier to implement effective solutions and get the most out of your automated equipment once it’s in your facility.
2. Prepare Your Facility
For instance, the surface area where the automated solution will be housed has to be completely cleared out of current inventory, pallets, shelves and other storage equipment so that it can be thoroughly cleaned. The floor must be extremely flat to ensure the system grid is flat to the floor, so retrieval bins won’t get stuck. Consider hiring a remediation specialist to prepare the floor and help ensure no one enters the premises while the flattening process is underway. This is a crucial step in the implementation process and cannot be overlooked.
Also, it might sound funny, but look up! Identify any ceiling fans, skylights or other obstructions high up that need to be moved or covered to protect from leaks.
Do not forget to consult with a trusted electrician. Your current facility might not have an ample amount of power intake required to operate an extremely large automated system and all its components. An electrician will assess the situation and make recommendations on what changes your power source will need to operate efficiently.
3. Get Comfortable with Surprises
As no one automated system is alike, no implementation service is perfect. Expect the unexpected and work the solution. For example, the floor flatness may fail and more remediation work has to be done…it can happen and indeed it happened to us. Change requests are also common with the size and scale of these projects so plan for a contingency spending cushion in your budget.
You may also face unforeseen fire suppression requirements...including the need for a fire pump or a VESDA alarm system installed for very early smoke detection. This is a very important step to take because if there’s any smoke in the air, the VESDA triggers an alarm, the automation robots huddle together, and the system stops.
Facility managers and owners spend a lot of time and effort making sure automation system implementations get done in their timeframe, but things can and will happen.
4. Ensure Your WMS Communicates Well
A successful automation system requires a cohesive relationship with a warehouse management system (WMS). Without good communication between the two, downtime issues will ensue resulting in lost time and profitability. Be sure to take the time to conduct your due diligence with the automation system provider and the WMS technicians to ensure your systems understand each other.
5. Empower Your People
Change isn’t always easy to accept, but gaining employee support makes integrating automation into your warehouse much easier. You will always need human beings on staff. That’s why it’s important to work closely with your entire warehouse team to make sure everyone is on the same page as you adopt new technology and practices.
Take time to listen to employee feedback about your automation strategy and use that insight to your advantage. Prioritizing your staff throughout and after the implementation process is the key to making the most of your automation while retaining passionate and enthusiastic employees.
In a landscape where the demand for automation is increasing, adopting these best practices is not only advantageous but essential for long-term success. By embracing automation, distributors can navigate the challenges of today's supply chain landscape and emerge as leaders in their industry.