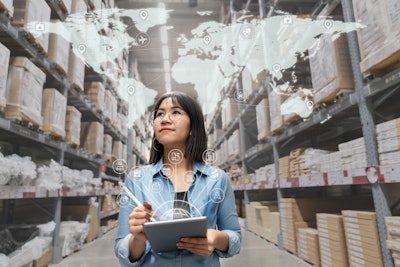
From life-saving equipment to the technologies used to improve daily life, semiconductors are the backbone of progress in today's world. Unfortunately, the global supply chain has experienced massive chip shortages due in part to the pandemic, labor shortages, company acquisitions, and the war between Russia and Ukraine. Given that this shortage is expected to continue until 2024, organizations are wise to put new consideration into their strategy for maintaining a robust inventory and must adopt nuanced ways to mitigate supply chain risk.
According to a 2020 study conducted by BluJay Solutions, 75 percent of leaders across the supply chain credit the pandemic for the changes to their supply chain process. McKinsey surveyed senior supply-chain executives from across industries and geographies and found that 93%of respondents intend to make significant changes to boost the flexibility, agility, and resilience of their supply chains. Furthermore, in the wake of the COVID-19 pandemic, the estimated value for out-of-stock items in 2020 totaled $1.14 trillion - a notable contrast to the $626 billion of overstock items, meaning out-of-stock items were double the value. In fact, 34% of businesses have delayed shipment or delivery due to selling a product that wasn’t in stock; likely contributing to the 63% supply chain accuracy that serves as the current industry standard.
Increasing the complexity of securing inventory; the inflation rate has risen as high as 8.5% so far in 2022, its highest level in over 40 years. With the Federal Reserve trying to regain control of current and future inflation trends, the greater the chances are of a policy decision that could push the economy into a recession. The only real solution for manufacturers who wish to minimize these additional losses is to maximize efficiency whenever possible. One way to tackle this issue is to leverage Big Data, and another is to move away from the traditional just-in-time inventory approach.
The role of big data in the supply chain
The Supply Chain Big Data Analytics Market is expected to grow by $4.88 billion by 2025, unsurprising when one considers that especially in times of significant supply chain constraint, only through the thorough analysis of comprehensive, accurate market data can an OEM make a decision to place orders for necessary electronic components, determine if alternate components are necessary, or even transition their product toward obsolescence in favor of a product with greater profitability.
The ability to acquire such data, however, not to mention analyze it, is beyond the scope of many manufacturers’ abilities. In some cases, the data on hand is limited by what one individual or small team can acquire on their own terms, which paints a very narrow picture of the current state of any given market. In order to get an accurate, top-down market view, an investment in Big Data is usually required. In most cases, this is an expensive proposition, and one most procurement teams are not capable of taking advantage of due to limited resources to properly analyze it.
There are, however, third-party technology solutions available. Procurement teams should seek out data integration solutions that leverage API to determine an accurate state of the market for each individual component on an OEM’s bill of material. The scope of this material can include tens of millions of data sheets, order quantities, component lead times, pricing, product descriptions, packaging protocols, and much more.
Access to Big Data does not have to be restricted to only the largest OEMs, nor does it require a significant investment to be accessible. Leveraging the right data integration solution ensures that manufacturers can have access to the data they need to properly plan and make the decisions necessary to move forward in this difficult environment.
Moving to a just in case model
Third-party inventory management solutions allow organizations in industries ranging from consumer electronics to healthcare to automotive to preserve their supply chains and maintain business continuity through any known risk, including semiconductor shortages. Instead of operating under a just-in-time inventory model, many OEMs are moving to a just-in-case model, via utilizing a third-party’s purchasing power to acquire all the inventory necessary to meet their production demands — without sacrificing any upfront working capital. Large, bulk purchases on the front end also put into play significant purchasing discounts from the manufacturer that are not available in a just-in-time-inventory model, a feature that can be extremely valuable to OEM supply chains.
Taken together, these trends all indicate that the supply chain professionals driving manufacturers’ response to the chip shortage are taking seriously the need to expand, innovate, and embrace the new technologies available in the marketplace. Inherently, this environment will favor the largest manufacturers, who can afford such investments. Small to mid-size manufacturers, however, should be aware of alternative solutions in order to maintain pace — or risk being overtaken. Third-party partners, for example, are ideal for adding additional innovations to any manufacturing supply chain, without the need for upfront capital investment.