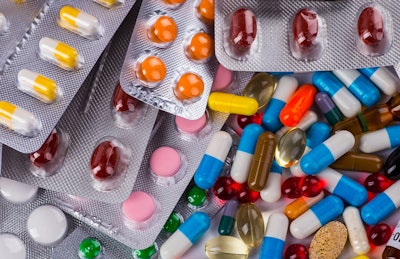
With so much at stake, the pharmaceutical supply chain needs special care and attention. The patient relies on medication for healing and recovery, and the industry has strict regulatory requirements that must be met.
This puts a lot of weight and responsibility on the pharmaceutical supply chain. Medications and supplies must be transported safely and often within a certain temperature range, while also meeting the regulatory requirements and satisfying the demands of patients and their providers. This can include requirements in different countries, challenges with cold storage infrastructure, and unanticipated delays.
Understanding patient centricity
Patient centricity has many definitions, but the earliest was put forth by AstraZeneca, patients, and caregivers: Patient centricity is putting the patient first in an open and sustained engagement of the patient to respectfully and compassionately achieve the best experience and outcome for that person and their family.
This collaborative effort identified five values important to patients seeking to have control with their health:
- Inclusiveness
- Sharing goals that are patient- and family-centric
- Empowering patients
- Showing respect, compassion, and openness
- Partnering
Pharmaceutical companies must focus on delivering products better to provide meaningful and impactful experiences, according to Guy Yeoman, Vice President of Patient Centricity at AstraZeneca.
Essentially, this means using common language and keeping patients included in the process from the start. Providers and pharmaceutical companies need to work with patients to develop solutions that are mutually agreeable.
Demand drivers of patient centricity
Like most other industries, the customer – or patient, in this case – is the focus. There are a number of factors that contribute to this new demand for patient-focused pharmaceutical supply chains.
Technology
Advanced technologies drive patient-centricity. Because patients have better access to information, they’re more knowledgeable and taking a more active role in their health. Enhanced communications among patients, advocacy groups, and pharmaceutical companies, allowing their voices to be heard.
In addition, technologies like advanced analytics and artificial intelligence are allowing for evaluation of data sets that can improve pharmaceutical design.
Regulatory agencies
Another driver is regulatory agencies, which have taken measures to include the patient in the development and approval processes for pharmaceuticals. The U.S. Food and Drug Administration (FDA) and the European Medicines Agency (EMA) are both working to include patient opinions in pharmaceutical development, including measures like holding meetings with patient groups.
Patient control
The pharmaceutical industry is also recognizing that, if they intend to create medications that improve or extend the lives of patients, then patients should have a say in how those medications are delivered. Gone are the days of pharmaceutical companies choosing what’s best for the patient.
Patient-centric supply chain
In the traditional view, the patient is at the end of the supply chain. Pharmaceutical discovery, development, manufacturing, distribution, and sales all come first.
In the patient-centric view and the increasing demand for personalized medicine and new, highly individualized therapies, the supply chain needs to begin and end with the patient.
One of the clearest indications of the shift is the increasing lifespan of the population. Medications are often a vital part of a patient’s day-to-day life – lifesaving, at times – and they can’t struggle with delays or inconveniences.
Patients need their medications delivered to them, at the time they need, and in ways that are convenient for them to use, along with being cost-effective. This requires visibility and transparency across the supply chain.
The globalization of supply chains created obstacles for this goal, but it also improves the possibility of end-to-end visibility. Cloud-based management solutions are helping with adaptive management and responsiveness, while digital technologies aid in cold-chain shipment monitoring and in-home collection of samples.
Damaged products and medicines that aren’t maintained within the required temperature ranges can cause life-threatening situations or subject patients to pain or discomfort until the medication arrives. Reliability is crucial in transporting healthcare products, and the supply chain needs to reflect its importance.
Planning for a patient-centric pharmaceutical supply chain
A patient-centric supply chain requires a lot of upfront effort and a shift in the way pharmaceutical companies and logistics companies manage them. Patients and the medications they need are diverse, and both patients and healthcare providers have different demands and expectations.
Considering the appropriate infrastructure within the network
Medications often need cold storage or controlled temperatures for safety and regulatory requirements. It’s important for pharmaceutical companies to consider third-party logistics providers and their infrastructure and transportation network, such as controlled temperature zones and coolers at ports and airports, for storage.
Global logistics companies with air, ocean freight, and land transportation options, as well as contract logistics, allow for security and flexibility in pharmaceutical distribution. With multiple transportation options and alternative solutions, you have a cost-effective, end-to-end solution for the pharmaceutical supply chain.
Staying aware of regulatory requirements from origin to destination
With a global supply chain for pharmaceuticals, medications may pass through many interim locations between origin and destination, all of which may have their own requirements. It’s vital to consider the requirements throughout the transportation process and avoid any barriers at customs, such as missing product labels or paperwork, that can cause delays.
Pharmaceutical companies need to consider the local, federal, and individual country’s regulatory requirements. A third-party logistics provider can offer customs brokerage services that can ensure all of this is tightened up and minimize delays throughout the transportation process.
Traceability according to regulations set forth by the WHO
The World Health Organization (WHO) estimates that roughly 50 percent of product recalls are a result of mislabeling and artwork errors. The Falsified Medicines Directive in the European Union requires pharmaceutical companies to use serialization codes on every applicable medication (with few exceptions).
WHO is becoming stricter on end-to-end batch traceability, so it’s an ever-more-important factor in the pharmaceutical supply chain.
Contingency planning is necessary to adapt to supply chain disruptions, delays, and disasters
In risk management, contingency planning is a course of action designed to help an organization respond effectively to a significant future event or situation that may or may not happen. This is commonly used in logistics to control supply chain activities and navigate delays and disruptions.
For example, a pharmaceutical company may use a carrier that’s been grounded, and a contingency plan would allow them to reroute those shipments to a different carrier. This prevents a small and unexpected delay from becoming a major disruption.
Contingency planning also helps with major disasters, such as natural disasters like hurricanes or tornadoes. Pharmaceutical companies may have manufacturing facilities in these areas, or medications may need to pass through areas affected by natural disasters. Planning is the only means to effectively navigate these situations and minimize delays and disruptions.
Keeping the patient first
Patient-centric supply chains are about more than meeting consumer demand – it’s about protecting the life of a human being. Medications may have a significant impact on quality of life and safety, and they need their transportation and care to reflect that.
Pharmaceutical companies can partner with third-party logistics suppliers that use temperature-controlled infrastructure for a secure supply chain and fewer losses and delays. Special handling and monitoring should be included for pharmaceuticals (and any deliveries in the healthcare industry), to adapt to changing conditions and deliver products safely and securely.