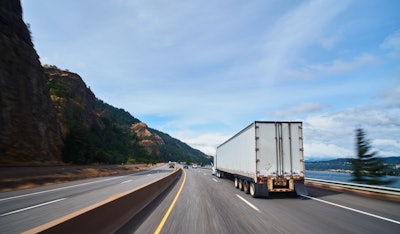
The broader supply chain industry is facing unprecedented challenges from all directions. Businesses are scrambling to get backlogs cleared to meet global demand. Citing supply chain disruptions, the IMF recently downgraded its forecast for global economic growth in 2022 from 4.9 to 4.4% . CBRE reported a tight 4% vacancy rate for industrial space, helping to fuel higher rents while interest, aided by transportation logjams, doesn’t seem to be lessening anytime soon. What can each business link in the chain do, within their own walls, to improve their performance in this turbulent environment? The following are examples of common challenges that we encounter in our work and ideas for how companies can use continuous improvement tools to unlock efficiencies and improve business performance.
1. Capacity Constraints
Capacity constraints usually present themselves in “not enough” statements: “We don’t have enough (time, space, equipment, people.)” The impact on a business can be anything from missed revenue opportunities, important projects waiting too long to be completed, or wasting time and money building unnecessary space.
For one client, a major printing and finishing business managing high end products with precision requirements, this translated to an inability to meet customer volume demand. They wanted to optimize operations to increase capacity by at least 30% with existing space and equipment, but solutions weren’t obvious. There were parts everywhere, numerous products, various sizes of products, and multiple workflows for the products. There was a culture of producing in high volume with a set minimum order quantity, believing that this would offset long setup times because of the complexity of the machinery involved.
CI Solutions and approaches
- Start by mapping the process and identify what is clearly waste.
- Keep an eye out for hints. Half of the warehouse was full of product and supplies that were at least two years old, suggesting over-processing or overproduction.
- Facilitate a team through a Value Stream Map and Timwoods analysis.
- Walk through the process to find places where you are making and processing more than a client or customer requires. Where is the work in process accumulating?
- Find the constraint and concentrate on that.
What we found:
In this case, the constraint was the gluing process, a slow process that was further weighed down by working on product that was overproduced. It was uncovered in the value stream map analysis. Additionally, there was no clear process for purging the excess product, leading to buildup in the warehouse of out-of-date materials. Armed with the right information, we were able to relieve the pinch point in production and free up capacity on the line and in the warehouse. By the end of the project, we had exceeded the original goal of a 30% capacity improvement, without a significant investment in capital equipment.
2. Changeover Reduction
Changeover time is a measurement of how long it takes to transition a machine or production line from working on one product to another. Long changeover rates waste equipment and personnel time, and in some cases increase the lead time to the customer. Reducing that single metric can help a company save money and increase production.
As an example, we worked with a home improvement supplier that was a major manufacturer of cartridges for sealants and adhesives used in construction. Long changeover times on machinery between runs led teams to overproduce certain products as a perceived safe guard for meeting inventory needs. Extra complexity was introduced with dyes used to color the products, requiring attention to detail.
CI Solutions and approaches
- Get everyone involved in the process in the room and set ambitious but achievable goals.
- Use Kaizen to get results quickly and leverage your team’s deep understanding.
- Utilize the six-step changeover reduction process:
Step 1 - Observe and Document the Process
Step 2 - Convert Internal Activities to External
Step 3 - Streamline Remaining Internal Activities
Step 4 - Eliminate Adjustments
Step 5 - Observe and Document the NEW Process
Step 6 - Develop Changeover Standard
What we found:
The changeover process was evaluated for opportunities to externalize internal steps. Once the Kaizen was completed custom parts were built to support the newly designed changeover process, and the average time decreased from 90 minutes to less than five.
3. Quality Improvement
Quality improvements can focus on a broad range of activities and generally seek to impact efficiency, effectiveness, and culture. High rates of defects or rework as well as non-standardized, unreliable or missing processes can all be signals that your organization could benefit from quality improvement.
A logistics company handling the relabeling of goods for private label customers was experiencing a 15% defect rate when they brought us in to help. Morale was low. With the lack of a clear understanding of the root cause, involved parties had taken to pointing fingers and increased frustrations.
CI Solutions and approaches
- The Gemba Walk. Gemba is a Japanese word, meaning “the real place.” A Gemba Walk is a way to gather information through observation and interaction with workers.
- Speak with the frontline workers and learn from their experience. By talking with the people who are doing with work and observing the process, you can gain a much deeper understanding of the current situation than you would from a typical meeting.
- Map the key movements, in this case: Spaghetti Map the journey of the labels.
- Use data as currency to open minds to the root causes.
What we found:
Speaking with frontline workers showed that what needed to be mapped was the labels, not the people handling them. Gathering data and documenting the printing and labeling practices revealed conflicts in both resourcing and process. Dedicated resources and a process redesign virtually eliminated the defects and the low morale that had resulted. This project both solved the business problem at hand and engaged the workforce in making a positive change.
In Conclusion
In the current climate, with long lead times for adding employees and dizzying demand for production, capacity is at a premium. Removing waste, while easier said than done, is always impactful and can be implemented in many ways, immediately. Identifying and freeing up resources that are burdened with non-value-added constraints empowers employees who are underutilized while being very busy. Every business operator, before looking beyond their service doors, can ask themselves “What problems are costing us efficiencies that are within our control to improve?”