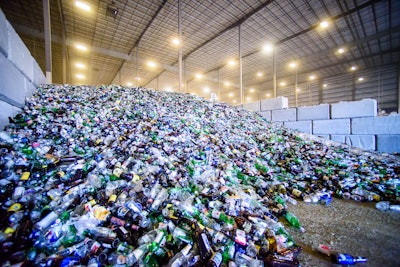
Founded in 1896, Strategic Materials is the largest recycler of glass in North America. With nearly 50 plants, Strategic Materials supplies recycled glass to manufacturers of glass containers, fiberglass insulation, highway bead, decorative glass, glass fillers and other specialty glass.
For Strategic Materials, quality is a primary measure of success. Yet, when it came to sharing quality data between plants, the company faced a challenge—each plant collected information using their own methods and nomenclature. That disparate data was then exported into Excel spreadsheets that didn’t align with any other plant’s information—making cross-site comparisons nearly impossible.
Brad Bell, Director of Quality and Continuous Improvement at Strategic Materials, wanted a quality system that would quickly and easily unite data from all plants—and he selected InfinityQS Enact. Within three months, the product was collecting and analyzing data across 12 Strategic Materials plants.
The company is now using Enact in 31 plants.
“All our recycling data now lives in one central location, so I don’t have to pull up Excel sheet A, B and C, and manually enter data. Without total visibility, continuous improvement initiatives were difficult to implement—and required extensive management time,” adds Bell.
Enterprise visibility = improved quality
Bell’s monthly routine used to involve gathering together each plant’s quality data— in separate Excel files—which he then had to reorganize into a meaningful format so he could better understand each plant’s performance.
According to Bell, “it was very time consuming and inefficient.”
Detecting quality issues as they happened—not after the fact—was critical to Bell, and digging through Excel documents made it difficult to monitor process capabilities. First, he would reformat each plant’s data, and then he would pour the retooled data into Minitab to review quality performance.
“It wasn’t in real-time, and everything was lagging as a result,” says Bell.
Enact provides Bell with a cross-plant reporting system that shows the real-time data needed to make process corrections.
“We have so much more visibility into our process quality capabilities since we started using Enact. We use the system to closely monitor performance on a day-to-day basis,” says Bell. “With Enact, we are able to quickly make improvements and see those improvements take hold—and when we spot something slipping back, we can immediately raise a red flag.”
A quick rollout was critical
For Strategic Materials, a seamless implementation was key. Enact was initially implemented at 12 critical plants, broken down by region. Bell first targeted plants with complex processes: sites with the highest volume and risk in terms of customer satisfaction.
Says Bell, “Once Enact was implemented and everybody was using it correctly, the four quality managers in charge of those plants served as support people—not just for entering data into the software, but helping our assigned plants drive process capabilities on their individual processes.”
According to Bell, “We rolled Enact right out—quickly—and then we expanded upon it.”
Strategic Materials developed a suite of standardized processes—building data collections and process models in Enact for standard lines as a group.
“Each plant has slightly different functionality and different features to measure, so we modified from there. But the basis of our processes is now the same across the board,” says Bell.
Enact enables Strategic Materials to collect manufacturing data the same way— across all plants.
“Enact provides the flexibility needed to differentiate between plants,” says Bell. “We can now easily add those features into the system as needed.”
Reducing costs and improving quality
Manufacturers need real-time data. It isn’t useful to learn days—or even weeks—later that a process was out of specification. All quality professionals know that being responsive and proactive is the best way to fully utilize collected manufacturing data.
Each Strategic Materials recycling plant has an established number of processes depending on what type of glass they recycle. Before Enact, personnel would enter quality data into one separate Excel file per process. Creating and managing these files was time-consuming and created data management headaches—plus, it wasn’t easy to detect when a production run was out of specification.
“We still have a lot more to learn, and we don’t yet use all the great features in the system, but Enact makes it easy to build out and use data collections,” says Bell.
The real-time data visibility provided by Enact helps stop problems in their tracks—before they escalate—reducing waste and improving product quality.
Consistent and reliable data entry
Strategic Materials needed to standardize their quality programs and processes across all plants: from nomenclature to data collection to analysis. With Enact in place, the Strategic Materials management team has total assurance that quality data gets entered into the system when checks are due.
“Now I can make sure operators are entering data exactly when they’re supposed to,” says Bell.
This provides the confidence Bell and his quality team need to trust that the data they share with management is accurate.
For a quality program to succeed, plant floor personnel need to report precise results—the good, the bad, or the different—in an effort to drive continuous improvement. When rolling out Enact, Bell explained to the quality technicians that no matter how out of specification data is, it is not viewed by management as a reflection of job performance.
“Standardizing how and when operators enter data into Enact ensures the accuracy and integrity of our quality data. Plus, once an operator enters information and saves it, that data can only be modified by management-level users,” Bell adds.
Inspiring customer confidence and opening new markets
The glass recycled by Strategic Materials comes from a wide variety of colored bottles and jars. Once recycled, the company supplies glass products to many types of container manufacturers.
As part of the recycling process, all incoming glass is checked for both color characteristics and contamination levels. A variety of characteristics are measured during this phase, including the level of organic material present in the glass being recycled. Enact helps Bell’s quality team monitor and manage these characteristics extremely closely, make immediate changes to processes when needed, and view recent data to ensure that quality is trending in the right direction.
Many Strategic Materials clients are very particular about both color and contamination level; as such, having a quality system that documents these parameters is vital to maintaining and expanding business.
Says Bell, “Enact enables us to demonstrate to both current and future customers that the changes we have made have been sustained for a specific amount of time—inspiring confidence that they can reliably increase the volume of product they purchase from us.”
Going above and beyond In specification
For Strategic Materials, being as close to target as possible means they can easily prove—to current and future customers alike—that they are a consistent, worry-free supplier who produces a higher quality product than the competition. This sets Strategic Materials apart, leads to increased orders, and creates additional revenue streams.
Built to collect quality data and conduct deep-dive analyses, Enact provides a richer way of understanding your processes—and shows you how to improve them. The true power hidden in your quality data lies is the ability to spot trends and respond quickly—and to make required process tweaks in the moment, preventing out of specification product from leaving the plant.
When choosing Enact, Strategic Materials resonated with three main benefits: a low per-license cost, fast and easy implementation with minimal IT requirements and total visibility into all quality data.
When combined with reliably keeping their products in specification, Enact provides everything Strategic Materials needs to ensure success
The right system for the job
There is no doubt about it—using the right tool produces the best results. Often, manufacturers who use ERP or MES systems are tempted to use the “quality” module included with their solution, yet rarely is this module operator-friendly, capable of collecting a wide range of data, and able to analyze real-time and historical quality and process information.
To expose opportunities for improvement, manufacturers need to collect and analyze tremendous amounts of quality data—line by line, plant by plant and across plants.
Says Bell, “We pushed hard for a cloud-based system for three reasons: ease of implementation, expanded data visibility, and ease of use for plant personnel.”
Enact gives manufacturers the power to analyze holistic quality data, exposing areas for improvement. For example, a majority of your quality data might be in specification— and your company may be generally satisfied with those results. But if you could instead analyze data and figure out ways to move in-specification processes a bit closer to target, you could improve process capability and efficiencies—and drive increased company revenue.