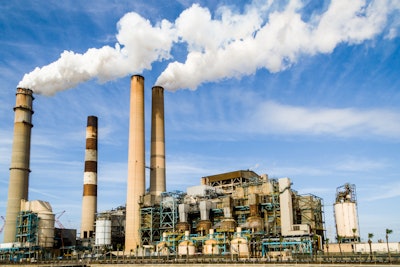
While China and the United States are different regarding consumer behavior, the fact that the country has experienced—and is now recovering from—the Coronavirus (COVID-19) outbreak first and its subsequent lockdowns could provide insight on what to expect in the future in terms of the supply chain. New cases of the virus in China have reportedly been down drastically in the last few weeks, allowing the country’s workforce to come back and start the supply chain back up again.
Employee rates in China are now greater than 70% right now, according to a report from Coresight. Industries such as finance, auto, catering, hospitality and supermarkets/shopping malls are seeing the highest number of returning staff. March 28 saw manufacturing plants and industrial enterprises are operating at a rate of 98.65%, excluding Hubei.
With employees back and consumer demand spiking up thanks to pent up buying needs and wants, China’s supply chain is on track for a bounce back. But, it is not without its changes or setbacks.
Warehouses are needing to sterilize entire facilities and wait for quarantine time periods to be cleared depending on when staff members contracted the virus. Regions need to wait a full 28 days with no new cases reported before returning. Those that do return are running with reduced staff members. With pockets of COVID-19 popping back up in various regions of China, stability is far away.
To help mitigate strain on the supply chain and reduce costs, brands operating locally in China are focusing on direct-to-consumer options in addition to product bundling.
The United States will likely follow suit in the coming months. Coresight also predicted that online ordering in the U.S. market can more than double as consumers seek ways around having to shop in stores.
A Supply Chain in the Dark
While retailers and supply chain warehouses cannot predict what exactly will be needed, precautions need to be taken now. Suppliers need to have full visibility on whether they have the scalability to keep up with demand. Communication will be extremely important, especially as current contracts are in flux due to the pandemic causing many companies to enact a force majeure clause.
"Right now, we are in a position where it is difficult for 3PLs and warehouse decision-makers to predict what they’ll need, and when,” says Ian Lifshitz, vice president, sustainability and stakeholder relations, North America, Asia Pulp & Paper. “The questions they should be thinking of now as they evaluate their supply chains is whether or not their suppliers are scaled appropriately and able to operate self-sufficiently."
Prior the pandemic, the supply chain related on historical figures to help guide businesses and operations moving forward but this virus has eradicated the usefulness of those numbers now. Artificial intelligence (AI) could be a way for suppliers to better predict how to move forward.
Those affected most are industries with smaller suppliers who lack the scale to maintain operations during an outbreak. The personal protective equipment (PPE) sector fits in this category, putting serious strain on medical staff, and also sees many products coming from Wuhan, China, adding to the stress on its supply chain.
“With manufacturing fully resuming in most parts of China in the last three to four weeks, the supply situation for medical supplies where finished production or raw material production occurs mainly in China has somewhat eased,” says Prashant Yadav, affiliate professor at INSEAD. “However, Wuhan still hasn’t fully come back to the same scale of manufacturing yet. Hubei province is a major manufacturing center for pharmaceutical ingredients, and textiles for personal protective equipment (PPE). This means the supply situation for medical products which are most needed for COVID-19 in the U.S. and EU is still facing significant supply constraints.
“In addition, air cargo capacity leaving out of Shanghai, Beijing and Guangzhou is still 20% lower than normal, resulting in significant delays in getting PPE supplies from China to the U.S.," adds Yadav.
Beacons of Hope for Help
In addition to AI, other factors that companies in the supply chain will need to rely on right now is fast decision making from leaders, robotics to help protect warehouse and even transportation workers since equipment cannot contract the virus and risk management.
Vice president of global supply chain solutions at Anaplan Evan Quasney believes that logisticians, cloud-based control towers and supplier collaboration solutions will shine during this time period.
“U.S. supply chains will face continued disruption moving forward,” Quasney says. “Coronavirus is challenging companies to pivot strategically and operationally at the same time, and supply chain leaders need to make complex decisions at rapid pace. Breaking down siloed decision making is more critical than ever before. Companies who collaborate across functions but also with their entire ecosystem (suppliers, partners, manufacturers, retailers, etc.) will optimize efficiencies and impact at a critical time.
In the near-term, historical demand will not be a reliable predictor for forecasting performance. This will be a strike against historical forecasting models and a boon for market intelligence-driven forecasting and proper implementation of forecast value add, ads Quasney.
I also expect to see sharp sustained demand for logisticians, cloud-based control towers, and supplier collaboration solutions that extend through an entire supply ecosystem. This will give business leaders stronger visibility so they can better meet demand requirements in the future.”