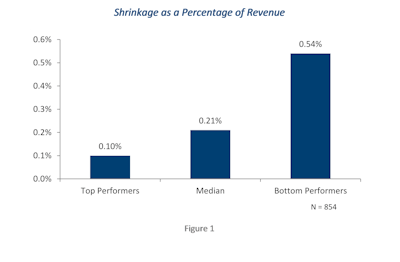
To preserve financial health and profit margins, organizations should seek to minimize shrinkage, calculated as the costs associated with breakage, theft and deterioration of inventories. Excess shrinkage can drive up inventory carrying costs, which are often taken into account when an organization sets prices, especially for high-value items. However, in a competitive market with high levels of price sensitivity, there may not be much room to raise prices, leaving organizations with pressure on their margins.
Implementing proper protection practices, such as controlled access, can help reduce theft and fraud, but inventory carrying costs also are impacted by shrinkage due to the obsolescence of various types of inventories (e.g., raw material, work in progress, finished goods and field samples). Therefore, inventory decisions should consider multiple types of relevant costs and associated risks.
How big is the shrinkage problem? As Figure 1 shows, for bottom performers in APQC’s Open Standards Benchmarking database, it can be 0.54 percent of revenue or more. If an organization moved from the bottom to the middle level of performance, that would be a savings of 0.33 percent of revenue. For a $2 billion organization, the savings potential from reduced shrinkage is $6,600,000 per year—money that can be better spent on improving performance and otherwise impacting profitability.
To take performance to the next level with best practices, as indicated in Supply Chain Management Process Standards, Second Edition, from the Council of Supply Chain Management Professionals using the APQC Process Classification Framework, organizations should review and adjust inventory targets or goals weekly or monthly based on product life-cycle, activity-based costing throughput, and variability in different inventory items. It is important that the organization categorize 100 percent of total inventory—active, usable, excess, obsolete—for appropriate action.
Another practice that can help control shrinkage is a formal excess and obsolete (E&O) process, where inventory is tracked monthly and aggressively reduced using industry appropriate methods (e.g., promotions, auctions or brokers). Organizations should also consider disposal and aftermarket techniques to deal with obsolete, stale and damaged inventories.
Thoroughly evaluating shrinkage includes looking at the actions of employees and suppliers to identify fraudulent behavior, as well as badly defined or documented processes that might lead to higher errors or inventory problems at multiple points in the process.
Focusing on minimizing shrinkage as a percentage of revenue can help organizations control costs and improve profit margins. The savings can be significant and impact an organization’s competitive position and success in the market.